Good spark plug wire usually has less than about 400-500ohms ohms resistance per ft.
Your correct that less resistance tends to allow more SPARK energy a crossed the plug gap, which in most cases is best set in the .040-.045 range in my experience, for HEI ignitions and .030 plug gap for a VERTEX MAG .spark plug wire designs vary a great deal between manufacturers and use different materials.
finding headers that fit your car and provide both easy access and the maximum clearance between the header tubes and ignition wire will generally require some research, BEFORE you purchase the headers!
Avoiding the problem by purchasing a quality header design goes a long way toward preventing issues with ignition wire and plug boots being damaged due to close contact with hot headers.
Most header manufacturers design headers they market to fit the maximum number of applications, to reduce the number of designs and part numbers needed in inventory, as a result most header designs are a compromise to allow fast and rather in expensive costs during their construction, and generally they get designed to fit the engines production cylinder head for the year and model of the car listed, and very few designs with work correctly with many after market cylinder heads, many of which were designed well after that car was produced.
the less expensive brands of header manufacturers also tend to use a bit smaller diameter, shorter primary tube and collector lengths and and thinner gauge tubing and flanges, and as a result many after marker extended sump oil pans, starters, and long oil filters cause clearance issues so do the required research before YOU spend your hard earned cash, and remember a low initial price may not be a bargain!
you might want to watch these video,s on swapping to low resistance ignition wire
http://www.summitracing.com/parts/msd-3508
Q. What should the Ohms per foot be on my wires?
A. ThunderVolt 50 = 40 Ohms
ThunderVolt 8.2 = 40 Ohms
StreeThunder = 500 Ohms
409 Pro Race = 350 Ohms
8mm Spiro Pro = 350 Ohms
8mm Pro Wire Resistor Core = 3,500 Ohms
Full Metal Jacket = 350 Ohms
Extreme Service = 350 Ohms
SST = 500 Ohms
8mm High Energy = 5,000 Ohms
good plug wires usually read less than 500 ohms per foot, less than about 2000 ohms is still decent for some wire designs but if the wire reads something like 36 k ohms plus your usually dealing with less than ideal wires
ID also mention that the older solid copper core ignition wire from the muscle car era, won,t work correctly on the more modern computer controlled cars as its electrical interference tends to cause the more current computer control systems to run poorly, if you can hear the ignition run in the radio static its a sure bet its having some effect on the control computer ability to read and send data from the sensors, and more than likely can eventually damage the computer, so select the type of ignition wire with significant sheilding
routing the wires so they don,t contact headers is critical to long term lifespan, and yes the thicker insulation and higher quality wires do tend to be less likely to arc to each other, or burn as easily.
some applications require the carbon core wires with the metallic outer core design to reduce EMF interference.
THE MOST COMMON SCREW-UP I SEE IS GUYS HAVING IGNITION WIRE THAT GETS MELTED ON HEADERS, ITS THE HEADER DESIGN MORE THAN ALMOST ANY OTHER FACTOR THAT CAUSES THIS, SO BEFORE BUYING HEADERS TRY TO FIND A SIMILAR SET THATS BEEN INSTALLED AND CHECK THE PLUG & WIRE CLEARANCE/ACCESS, doing that, so you can avoid badly designed headers, can save you years of grief
TAYLOR,MSD,MOROSO all make decent wire and you don,t need to go crazy on the price or diam.
, most of the spiral core 8mm-10.4 mm work fine,any of the above listed brands, I prefer the TAYLOR wires personally
do yourself a favor & read the linked info
http://www.thermotec.com/products/14200 ... hield.html
Spark Plug Wire Heat Shield
The Spark Plug Wire Heat Shield offers the ultimate protection for spark plug wires and boots from conductive and radiant heat, which is a problem.
The dual-purpose sleeve has a surface that reflects over 90% of radiant heat up to 2000º, while the inside silica-based fabric prevents conductive heat from penetrating.
Part Numbers
Part Number Description
14200 2 pc. 6" X 2-1/2"
http://cableorganizer.com/insultherm-spark/
http://www.magnecor.com/magnecor1/truth.htm
http://www.taylorvertex.com/Products/index.cgi/main3
getting the timing to retarded or f/a mix too lean and exhaust temps climb, usually resulting in burnt ignition wires or plug boots
It really looks like those headers ,in the picture you posted that, your using were designed for use with the angle plug heads,
and use of the strait plug heads causes the spark plug to header tube,
and related ignition wire clearance issues.
this is, unfortunately a very common miss match of components.
look at the heads and the exhaust header tube routing and the difference in clearance,
that the designed angle plug heads use would make on spark plug to header tube clearance.
one of the least understood yet common problems is that the header manufacturers seldom bother to tell you what cylinder heads were used during the header design phase of production of the headers and damn few people purchasing headers bother to do the research or ask detailed questions until they run into problems caused by the design miss match, and yes its very common to find headers designed for strait plug heads can cause similar issues if used with angle plug heads , but thats slightly less common
RELATED THREADS
http://garage.grumpysperformance.com/index.php?threads/installing-hard-to-access-plugs.962/
http://garage.grumpysperformance.com/index.php?threads/building-custom-headers.961/#post-56850
http://garage.grumpysperformance.com/index.php?threads/straight-vs-angle-plug-sbc-heads.2712/
http://garage.grumpysperformance.com/index.php?threads/why-use-anti-seize-paste.9424/
http://garage.grumpysperformance.co...ition-wires-getting-the-header-clearance.840/
http://garage.grumpysperformance.com/index.php?threads/straight-vs-angle-plug-sbc-heads.2712/
http://garage.grumpysperformance.co...-guys-that-just-slap-on-factory-headers.3155/
http://www.summitracing.com/parts/TAY-99610/
while wrapping the plug boot like above appears to be a splendid idea for reflecting heat and might work perfectly I suspect theres at least some potential the metallic heat reflective tape could potentially provide an electrically conductive short circuit path for ignition voltage
the ceramic boots at least in theory , when combined with heat reflective / insulating socks, like pictured below might produce a less likely electrical ground path
Id at least suggest increasing the potential distance an electrical arc might potentially jump and use of an over the boot surface non-electrically conductive sock to be used under the heat reflective layer some what similar to these pictured below
these work on BBC combos with an HEI distributor, and headers
BE AWARE, that theres a significant variation in spark plug location between different cylinder head designs,made by different manufacturers ,and theres both strait and angle plug heads and even the angle plug heads vary a good deal between designs, and many headers won,t work with a few cylinder heads in some applications so its almost mandatory that you call and talk too the tech support guys from both the cylinder head and headers manufacturers, to ask if any specific combo has a history of clearance issues BEFORE purchasing your headers or cylinder heads or both.
http://www.summitracing.com/parts/TAY-84606/
http://www.summitracing.com/parts/TAY-91002/
http://www.summitracing.com/parts/TAY-79667/
http://garage.grumpysperformance.com/index.php?threads/installing-hard-to-access-plugs.962/
ITS extremely important that you ask questions and get accurate answers , BEFORE purchasing headers about what style cylinder heads the headers are designed to fit, below is pictured a set of headers obviously designed for factory strait plug heads but bolted to a set of angle plug heads making spark plug access and wiring a clearance and heat , destroying ignition wire nightmare
angle plug
Accel Extreme 9000 Ceramic Wire Sets
ACCEL now offers the cure for burnt spark plug wire boots with Extreme 9000 Ceramic Wire kits. The 8mm Ferro-Spiral core wire now has ceramic boots on the spark plug end of the wires that will withstand up to 2,000° F. If you are running headers with close tolerances, an engine bay with little room, or an RV with boots that melt because of heat, these wire kits are the answer. and yeah! youll still need the heat resistant plug boots to prevent the wires from melting past the ceramic plug boot
FOR PLUGS...
this is an all to common issue because header manufacturers rarely check spark plug clearance with anything other than factory original cylinder heads for a listed application and even with factory original cylinder heads for a listed application, I occasionally see headers with what can only be described as PISS POOR CLEARANCE, for plugs , ignition wire and plug boots.
Report this image
the typical woven or aluminum foil reflective boot covers for protecting plug boots help but depending on the application they may not be adequate protection, it helps but over time heat still can burn thru the ignition wire insulation, the ceramic plug boots plus the shorter plugs and the heat resistant flex wire shields may be required on some headers to provide the required heat protection, and clearance, to the ignition wire
Report this image
use of shorter plugs helps in some applications,cutting a standard spark plug socket to a significantly shorter length and use of an open end of flex wrench eases access
BTW, its not really all that rare to find that the headers you have present a spark plug wire clearance issue,
SPACING THE HEADER FLANGE A BIT FURTHER AWAY FROM THE CYLINDER HEAD WITH A SPACER PLATE CAN AT TIMES BE HELPFUL
that makes installing the spark plug boots in such a way that they don,t contact the hot metal surfaces almost impossible , this can sometimes be helped a great deal by the addition of a header flange, or SPACER PLATE, that MATCHES YOUR PARTICULAR ENGINES CYLINDER HEAD EXHAUST PORT AND HEADERS,
thats significantly thicker being welded to the existing header flange , to space it out further away from the cylinder heads, obviously you don,t want to do this without testing all the clearances so installing the extra header flange with an exhaust gasket on both the cylinder head surface and between the header flange spacer and the existing headers as a test is strongly suggested as a test.
THIS IS ALSO USEFUL AT TIMES TO ADAPT THE ENGINE TO A DIFFERENT BOLT PATTERN OR SPACING
http://www.jegs.com/i/JEGS-Performance-Products/555/30790/10002/-1?parentProductId=977236
heres where you get spacer header flange plates
http://www.jegs.com/p/JEGS-Performance-Products/JEGS-Header-Exhaust-Flanges/1127498/10002/-1
http://www.summitracing.com/search/Part-Type/Header-Flanges/
http://www.hedmanhusler.com/Hedder-Flanges-without-Stubs
http://rehermorrison.com/product/adapter-plates/
bosch, AC delco, NGK all work
set the gap at .043-.045 and don,t forget to use anti-seize on the plug threads
http://store.summitracing.com/partdetail.asp?autofilter=1&part=LCT-37616&N=700+115&autoview=sku
I prefer TAYLOR wires
http://www.summitracing.com/parts/TAY-80617/
a V.O.M meter and this tool can come in handy
http://www.harborfreight.com/cpi/ctaf/D ... mber=97577
http://garage.grumpysperformance.com/index.php?threads/installing-hard-to-access-plugs.962/
viewtopic.php?f=80&t=10730&p=46843#p46843
Your correct that less resistance tends to allow more SPARK energy a crossed the plug gap, which in most cases is best set in the .040-.045 range in my experience, for HEI ignitions and .030 plug gap for a VERTEX MAG .spark plug wire designs vary a great deal between manufacturers and use different materials.
finding headers that fit your car and provide both easy access and the maximum clearance between the header tubes and ignition wire will generally require some research, BEFORE you purchase the headers!
Avoiding the problem by purchasing a quality header design goes a long way toward preventing issues with ignition wire and plug boots being damaged due to close contact with hot headers.
Most header manufacturers design headers they market to fit the maximum number of applications, to reduce the number of designs and part numbers needed in inventory, as a result most header designs are a compromise to allow fast and rather in expensive costs during their construction, and generally they get designed to fit the engines production cylinder head for the year and model of the car listed, and very few designs with work correctly with many after market cylinder heads, many of which were designed well after that car was produced.
the less expensive brands of header manufacturers also tend to use a bit smaller diameter, shorter primary tube and collector lengths and and thinner gauge tubing and flanges, and as a result many after marker extended sump oil pans, starters, and long oil filters cause clearance issues so do the required research before YOU spend your hard earned cash, and remember a low initial price may not be a bargain!
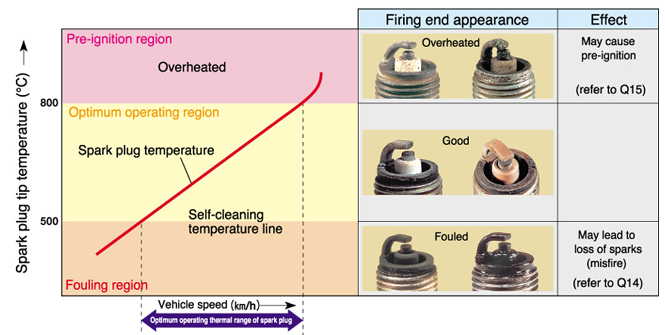
you might want to watch these video,s on swapping to low resistance ignition wire
http://www.summitracing.com/parts/msd-3508
Q. What should the Ohms per foot be on my wires?
A. ThunderVolt 50 = 40 Ohms
ThunderVolt 8.2 = 40 Ohms
StreeThunder = 500 Ohms
409 Pro Race = 350 Ohms
8mm Spiro Pro = 350 Ohms
8mm Pro Wire Resistor Core = 3,500 Ohms
Full Metal Jacket = 350 Ohms
Extreme Service = 350 Ohms
SST = 500 Ohms
8mm High Energy = 5,000 Ohms
good plug wires usually read less than 500 ohms per foot, less than about 2000 ohms is still decent for some wire designs but if the wire reads something like 36 k ohms plus your usually dealing with less than ideal wires
ID also mention that the older solid copper core ignition wire from the muscle car era, won,t work correctly on the more modern computer controlled cars as its electrical interference tends to cause the more current computer control systems to run poorly, if you can hear the ignition run in the radio static its a sure bet its having some effect on the control computer ability to read and send data from the sensors, and more than likely can eventually damage the computer, so select the type of ignition wire with significant sheilding
routing the wires so they don,t contact headers is critical to long term lifespan, and yes the thicker insulation and higher quality wires do tend to be less likely to arc to each other, or burn as easily.
some applications require the carbon core wires with the metallic outer core design to reduce EMF interference.
THE MOST COMMON SCREW-UP I SEE IS GUYS HAVING IGNITION WIRE THAT GETS MELTED ON HEADERS, ITS THE HEADER DESIGN MORE THAN ALMOST ANY OTHER FACTOR THAT CAUSES THIS, SO BEFORE BUYING HEADERS TRY TO FIND A SIMILAR SET THATS BEEN INSTALLED AND CHECK THE PLUG & WIRE CLEARANCE/ACCESS, doing that, so you can avoid badly designed headers, can save you years of grief
TAYLOR,MSD,MOROSO all make decent wire and you don,t need to go crazy on the price or diam.
, most of the spiral core 8mm-10.4 mm work fine,any of the above listed brands, I prefer the TAYLOR wires personally
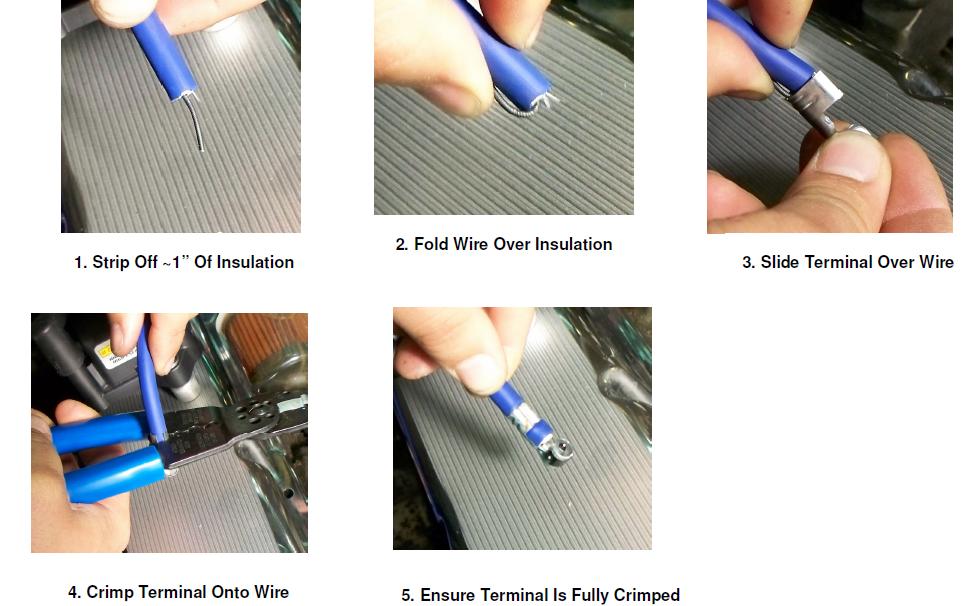
do yourself a favor & read the linked info
http://www.thermotec.com/products/14200 ... hield.html
Spark Plug Wire Heat Shield
The Spark Plug Wire Heat Shield offers the ultimate protection for spark plug wires and boots from conductive and radiant heat, which is a problem.
The dual-purpose sleeve has a surface that reflects over 90% of radiant heat up to 2000º, while the inside silica-based fabric prevents conductive heat from penetrating.
Part Numbers
Part Number Description
14200 2 pc. 6" X 2-1/2"
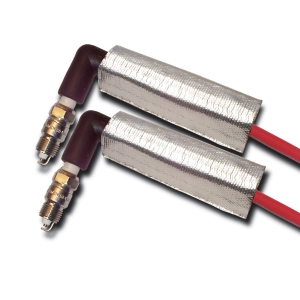
http://cableorganizer.com/insultherm-spark/
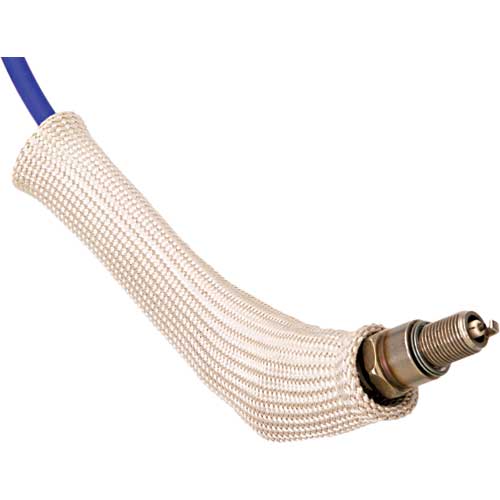
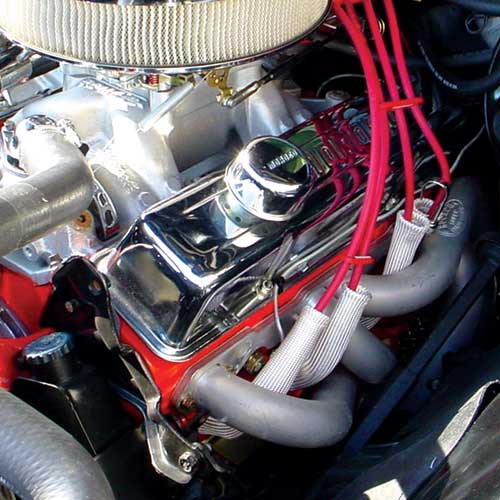
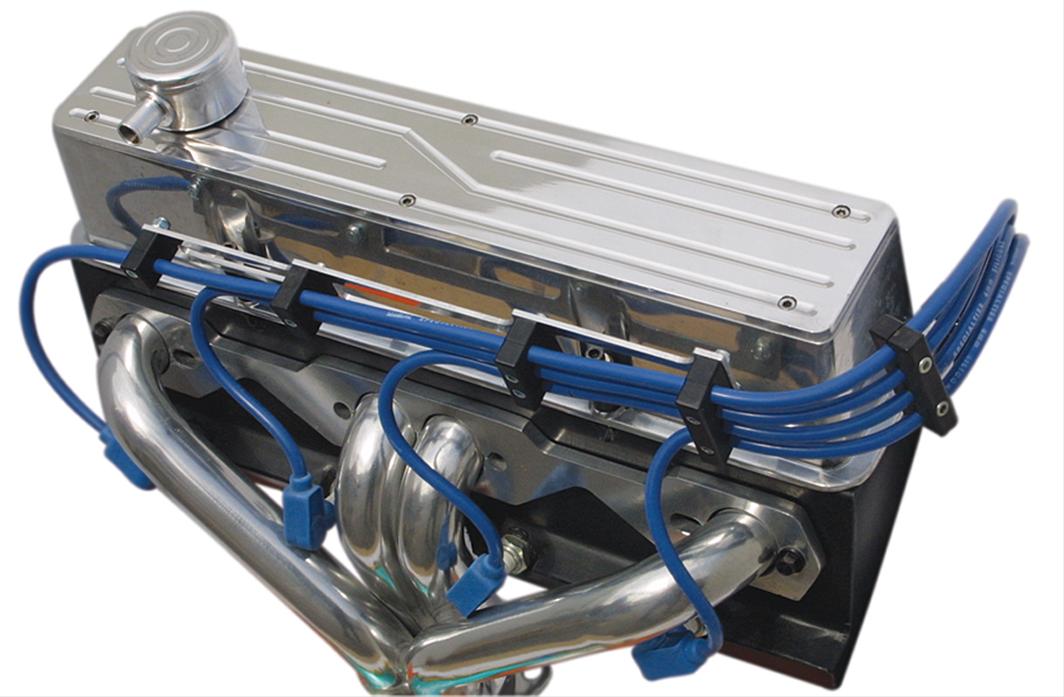
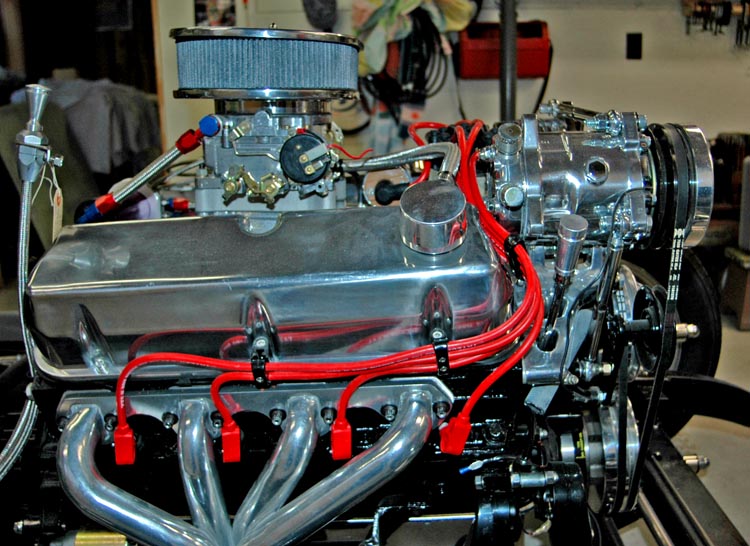
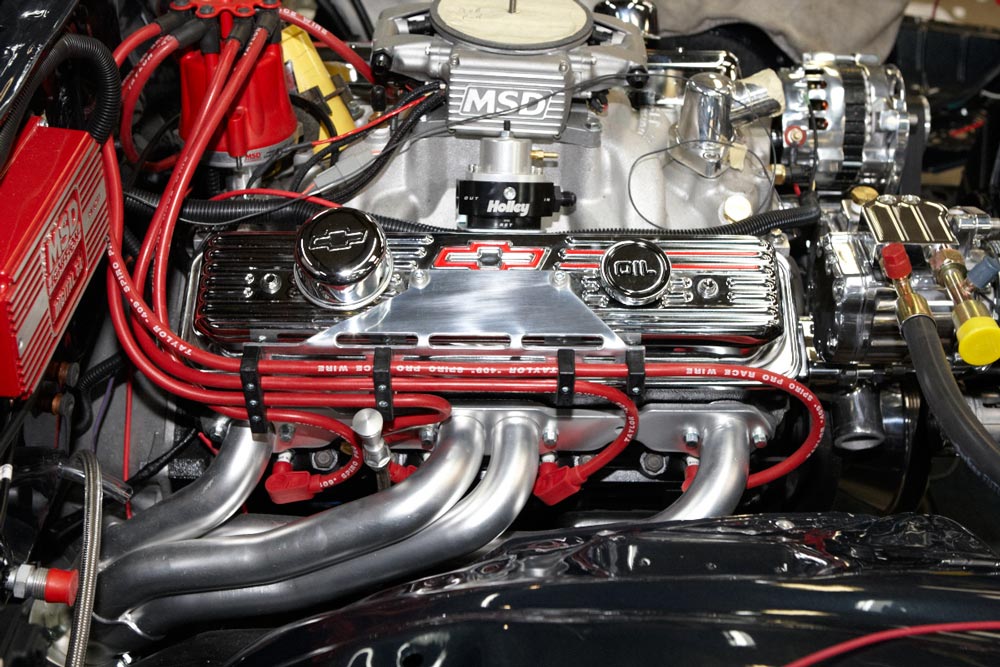
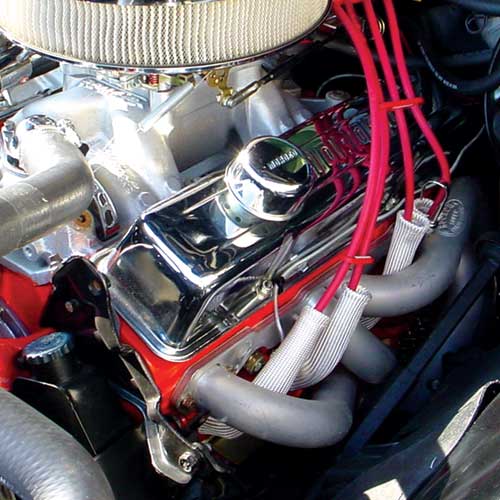
http://www.magnecor.com/magnecor1/truth.htm
http://www.taylorvertex.com/Products/index.cgi/main3
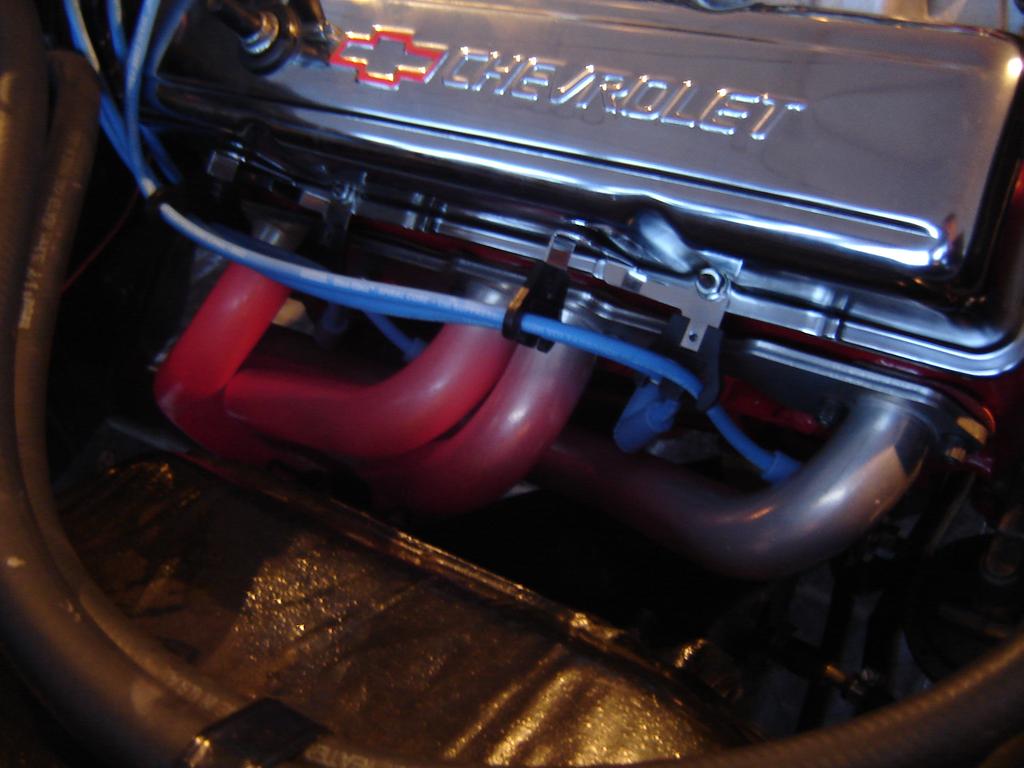
getting the timing to retarded or f/a mix too lean and exhaust temps climb, usually resulting in burnt ignition wires or plug boots
It really looks like those headers ,in the picture you posted that, your using were designed for use with the angle plug heads,
and use of the strait plug heads causes the spark plug to header tube,
and related ignition wire clearance issues.
this is, unfortunately a very common miss match of components.
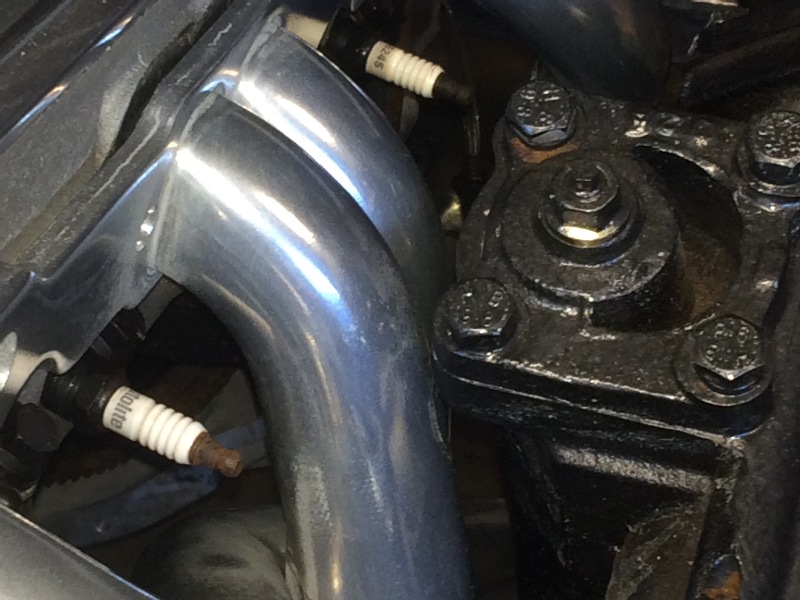
look at the heads and the exhaust header tube routing and the difference in clearance,
that the designed angle plug heads use would make on spark plug to header tube clearance.
one of the least understood yet common problems is that the header manufacturers seldom bother to tell you what cylinder heads were used during the header design phase of production of the headers and damn few people purchasing headers bother to do the research or ask detailed questions until they run into problems caused by the design miss match, and yes its very common to find headers designed for strait plug heads can cause similar issues if used with angle plug heads , but thats slightly less common


RELATED THREADS
http://garage.grumpysperformance.com/index.php?threads/installing-hard-to-access-plugs.962/
http://garage.grumpysperformance.com/index.php?threads/building-custom-headers.961/#post-56850
http://garage.grumpysperformance.com/index.php?threads/straight-vs-angle-plug-sbc-heads.2712/
http://garage.grumpysperformance.com/index.php?threads/why-use-anti-seize-paste.9424/
http://garage.grumpysperformance.co...ition-wires-getting-the-header-clearance.840/
http://garage.grumpysperformance.com/index.php?threads/straight-vs-angle-plug-sbc-heads.2712/
http://garage.grumpysperformance.co...-guys-that-just-slap-on-factory-headers.3155/
http://www.summitracing.com/parts/TAY-99610/
while wrapping the plug boot like above appears to be a splendid idea for reflecting heat and might work perfectly I suspect theres at least some potential the metallic heat reflective tape could potentially provide an electrically conductive short circuit path for ignition voltage
the ceramic boots at least in theory , when combined with heat reflective / insulating socks, like pictured below might produce a less likely electrical ground path
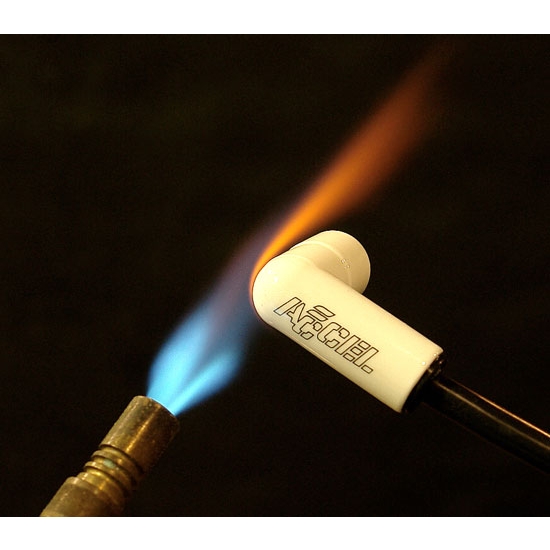
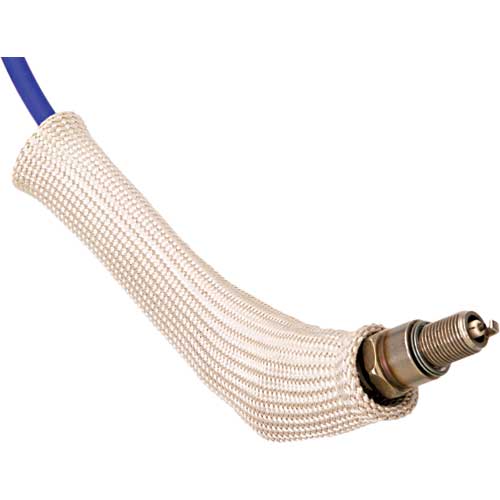
Id at least suggest increasing the potential distance an electrical arc might potentially jump and use of an over the boot surface non-electrically conductive sock to be used under the heat reflective layer some what similar to these pictured below
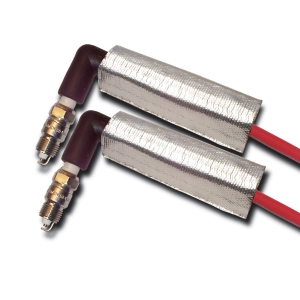
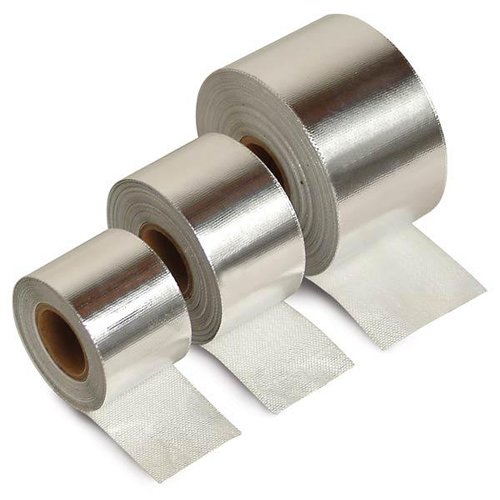
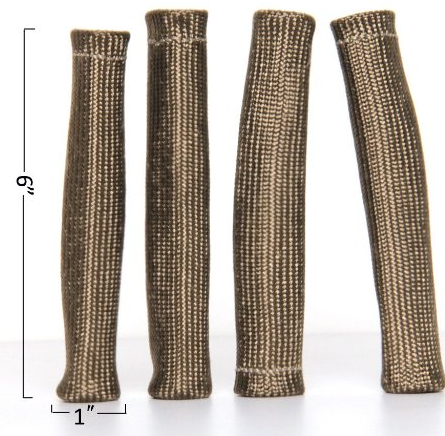
these work on BBC combos with an HEI distributor, and headers
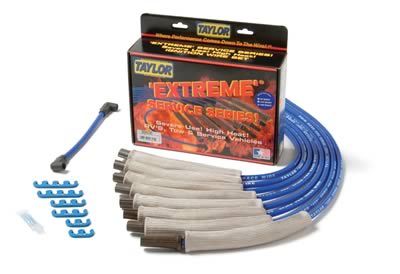
BE AWARE, that theres a significant variation in spark plug location between different cylinder head designs,made by different manufacturers ,and theres both strait and angle plug heads and even the angle plug heads vary a good deal between designs, and many headers won,t work with a few cylinder heads in some applications so its almost mandatory that you call and talk too the tech support guys from both the cylinder head and headers manufacturers, to ask if any specific combo has a history of clearance issues BEFORE purchasing your headers or cylinder heads or both.
http://www.summitracing.com/parts/TAY-84606/
http://www.summitracing.com/parts/TAY-91002/
http://www.summitracing.com/parts/TAY-79667/
http://garage.grumpysperformance.com/index.php?threads/installing-hard-to-access-plugs.962/
ITS extremely important that you ask questions and get accurate answers , BEFORE purchasing headers about what style cylinder heads the headers are designed to fit, below is pictured a set of headers obviously designed for factory strait plug heads but bolted to a set of angle plug heads making spark plug access and wiring a clearance and heat , destroying ignition wire nightmare
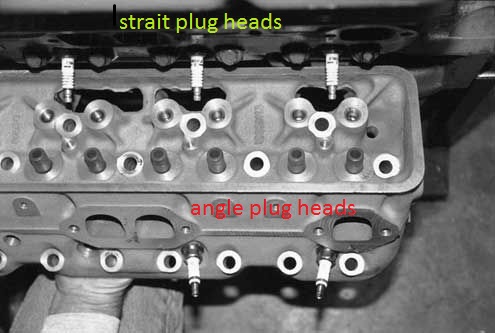
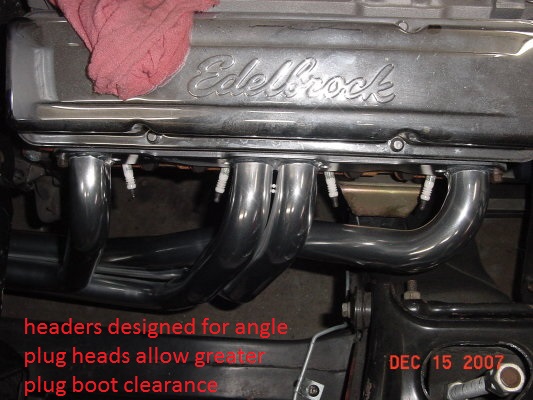
angle plug
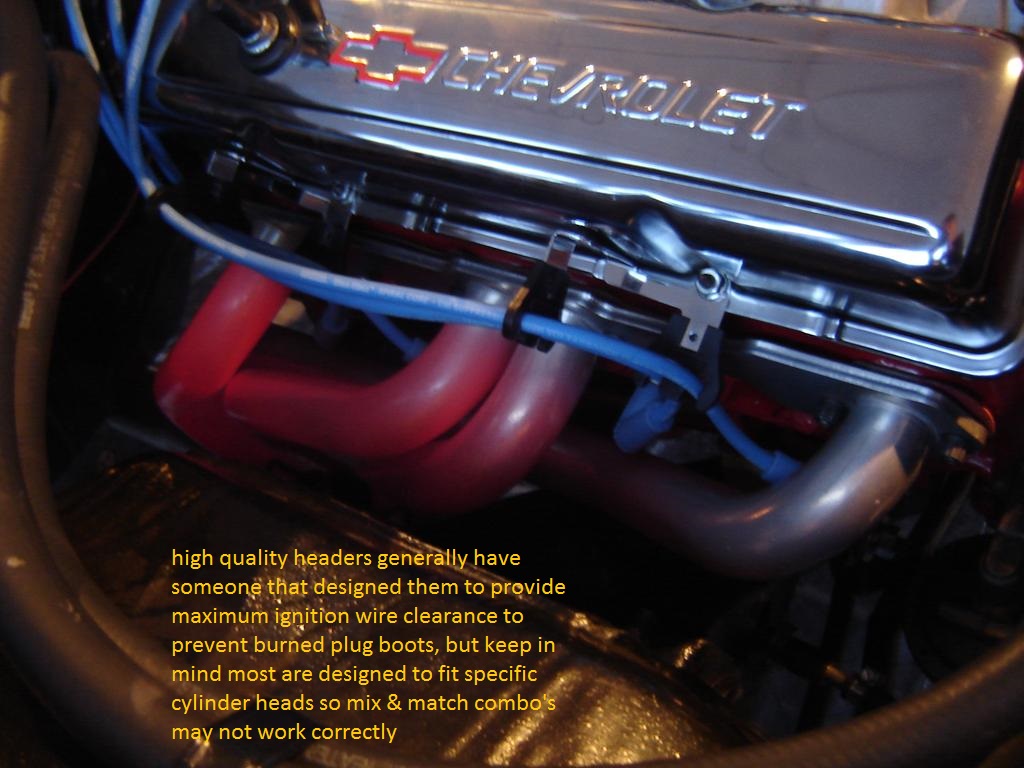
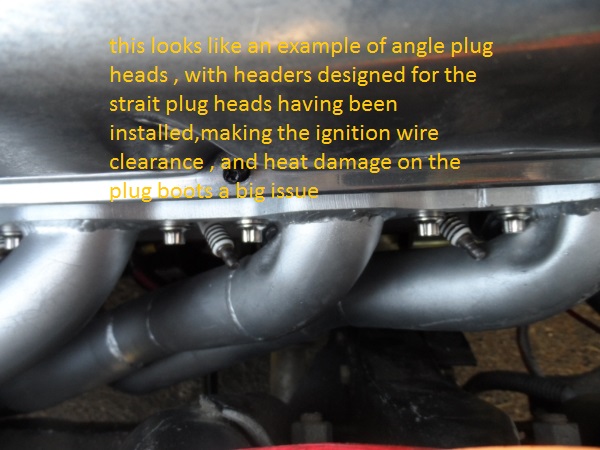
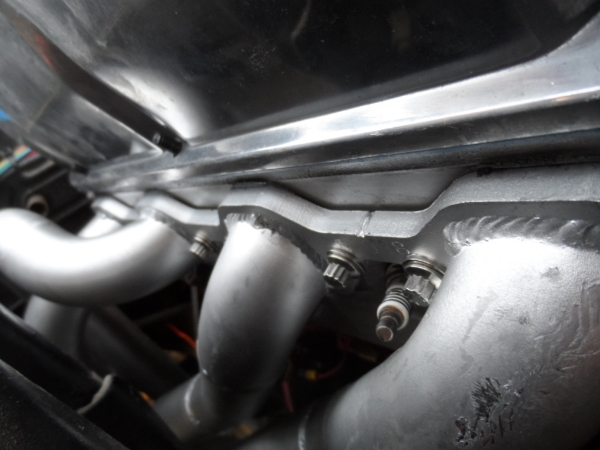
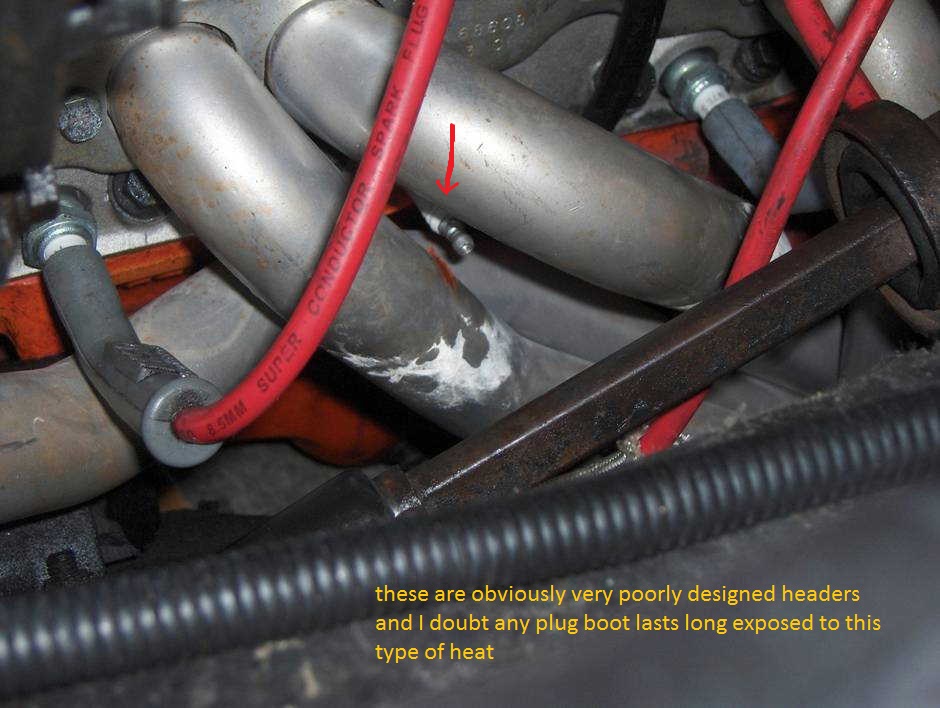
Accel Extreme 9000 Ceramic Wire Sets
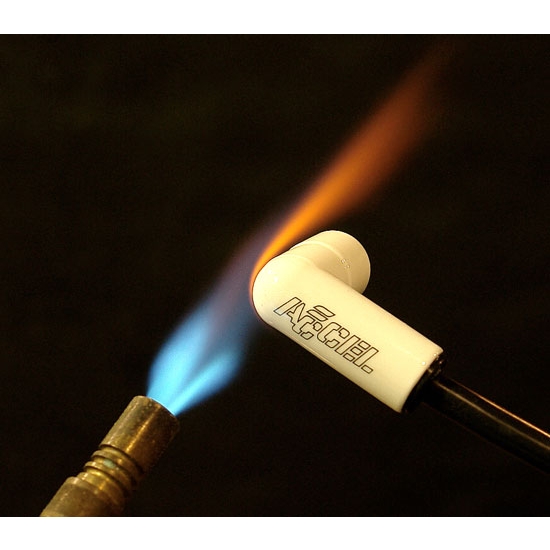
ACCEL now offers the cure for burnt spark plug wire boots with Extreme 9000 Ceramic Wire kits. The 8mm Ferro-Spiral core wire now has ceramic boots on the spark plug end of the wires that will withstand up to 2,000° F. If you are running headers with close tolerances, an engine bay with little room, or an RV with boots that melt because of heat, these wire kits are the answer. and yeah! youll still need the heat resistant plug boots to prevent the wires from melting past the ceramic plug boot
FOR PLUGS...
this is an all to common issue because header manufacturers rarely check spark plug clearance with anything other than factory original cylinder heads for a listed application and even with factory original cylinder heads for a listed application, I occasionally see headers with what can only be described as PISS POOR CLEARANCE, for plugs , ignition wire and plug boots.
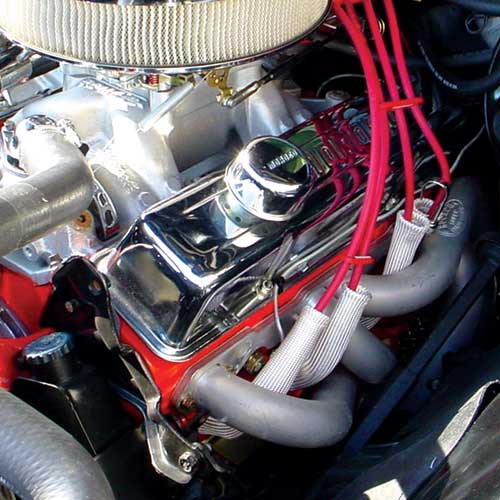
Report this image
the typical woven or aluminum foil reflective boot covers for protecting plug boots help but depending on the application they may not be adequate protection, it helps but over time heat still can burn thru the ignition wire insulation, the ceramic plug boots plus the shorter plugs and the heat resistant flex wire shields may be required on some headers to provide the required heat protection, and clearance, to the ignition wire
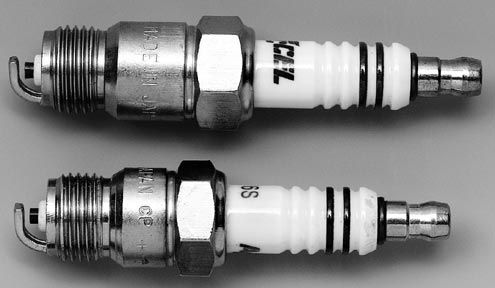
Report this image
use of shorter plugs helps in some applications,cutting a standard spark plug socket to a significantly shorter length and use of an open end of flex wrench eases access
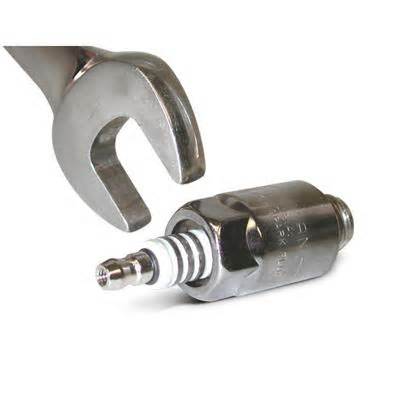
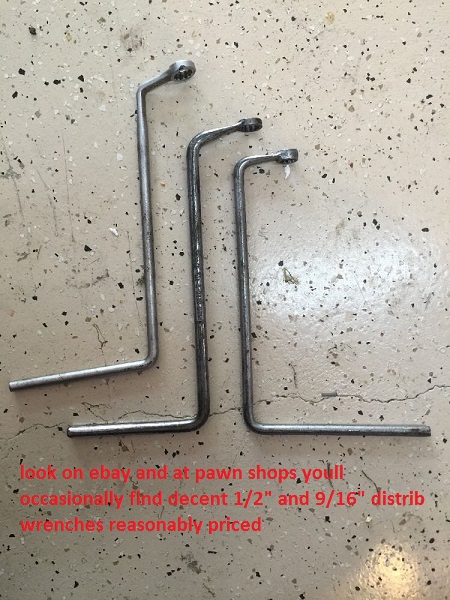
BTW, its not really all that rare to find that the headers you have present a spark plug wire clearance issue,
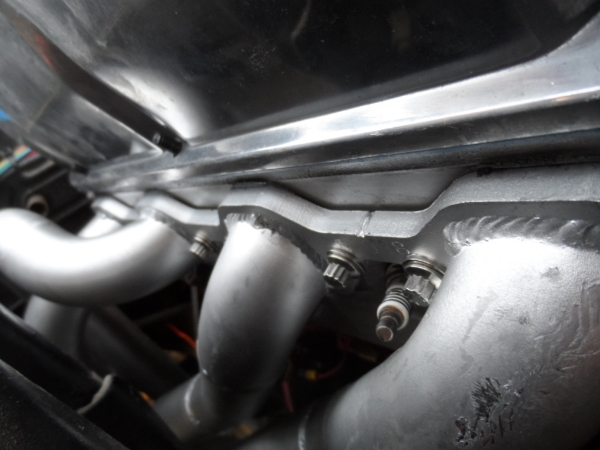
SPACING THE HEADER FLANGE A BIT FURTHER AWAY FROM THE CYLINDER HEAD WITH A SPACER PLATE CAN AT TIMES BE HELPFUL
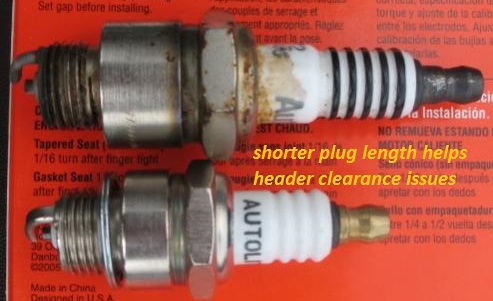
that makes installing the spark plug boots in such a way that they don,t contact the hot metal surfaces almost impossible , this can sometimes be helped a great deal by the addition of a header flange, or SPACER PLATE, that MATCHES YOUR PARTICULAR ENGINES CYLINDER HEAD EXHAUST PORT AND HEADERS,
thats significantly thicker being welded to the existing header flange , to space it out further away from the cylinder heads, obviously you don,t want to do this without testing all the clearances so installing the extra header flange with an exhaust gasket on both the cylinder head surface and between the header flange spacer and the existing headers as a test is strongly suggested as a test.
THIS IS ALSO USEFUL AT TIMES TO ADAPT THE ENGINE TO A DIFFERENT BOLT PATTERN OR SPACING
http://www.jegs.com/i/JEGS-Performance-Products/555/30790/10002/-1?parentProductId=977236
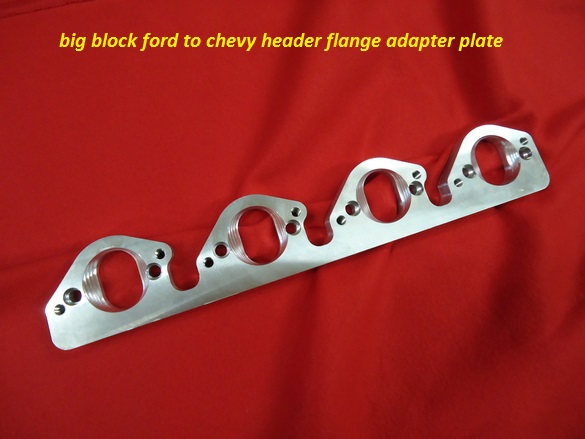
heres where you get spacer header flange plates
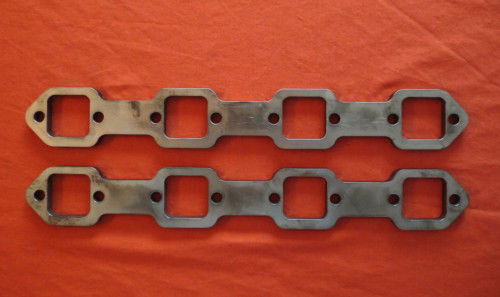
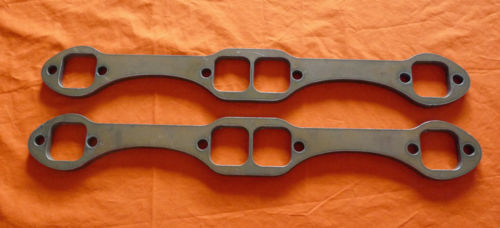
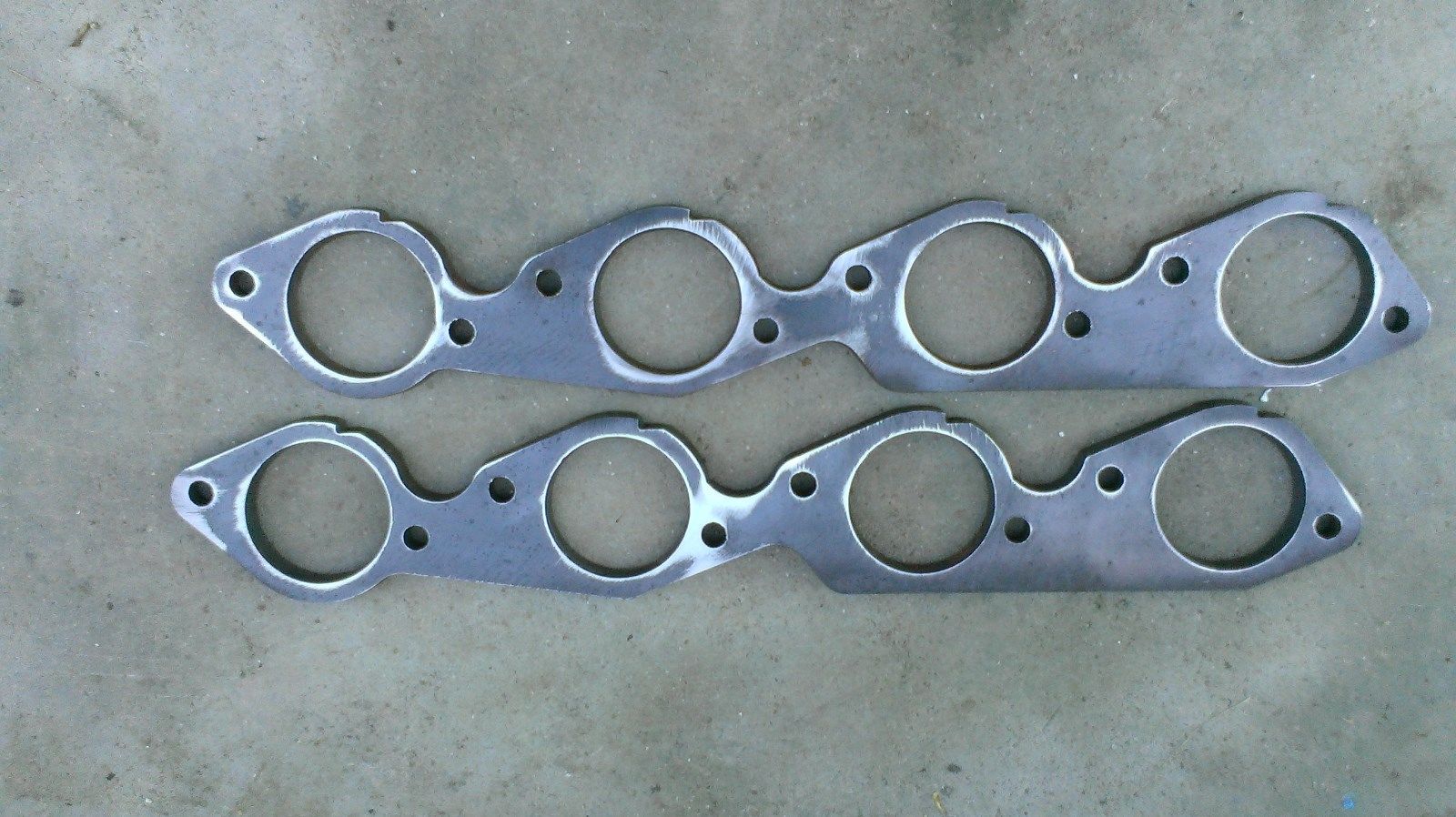
http://www.jegs.com/p/JEGS-Performance-Products/JEGS-Header-Exhaust-Flanges/1127498/10002/-1
http://www.summitracing.com/search/Part-Type/Header-Flanges/
http://www.hedmanhusler.com/Hedder-Flanges-without-Stubs
http://rehermorrison.com/product/adapter-plates/
bosch, AC delco, NGK all work
set the gap at .043-.045 and don,t forget to use anti-seize on the plug threads
http://store.summitracing.com/partdetail.asp?autofilter=1&part=LCT-37616&N=700+115&autoview=sku
I prefer TAYLOR wires
http://www.summitracing.com/parts/TAY-80617/
a V.O.M meter and this tool can come in handy
http://www.harborfreight.com/cpi/ctaf/D ... mber=97577
http://garage.grumpysperformance.com/index.php?threads/installing-hard-to-access-plugs.962/
viewtopic.php?f=80&t=10730&p=46843#p46843
Last edited by a moderator: