ok how do i adjust them now?
http://www.thedirtforum.com/chevyvalves.htm
http://www.2quicknovas.com/happyvalves.html
https://www.craftsman.com/products/craftsman-mach-series-14-piece-3-8-t-handle-driver-and-bit-set
http://www.centuryperformance.com/valveadjustment.asp
http://www.boostandfuel.com/support/setting_valves.htm
http://www.carcraft.com/techarticles/87998/index2.html
http://www.angelfire.com/fl4/pontiacdude428/valveadj.html
btw if your totally new at this the tappet feeler gauge measures the lash clearance between the valve and rocker on solid lifter cams
I just don,t think adjusting the valves without the oil pressure and the block up to operating temp. is the best way to adjust valves , but yes you can do it just fine with several methods discribed above
how do you adjust valves at idle without the mess of oil getting all over the engine and headers
HIT A FEW YARD SALES, SWAP MEETS UNTILL YOU FIND A DIRT CHEAP SET OF TALL CAST VALVE COVERS LIKE THESE, the CONDITION THEY ARE IN ,WITHIN REASONABLE LIMITS OF COURSE IS NOT THAT IMPORTANT
you simply cut the ribbed center section out of the valve cover, and glue the synthetic valve cover gaskets on them in the normal location,
when you go to adjust the valves you first remove the standard valve covers and install your VALVE ADJUSTMENT COVERS, they retain about 80%-90% of the oil that would normally be lost over the edge of the cylinder head while adjusting a running engine, they also catch much of the splashed oil, just leave a 1/4"-3/8" of the rolled top for strenth around the perimiter of the top surface. I bought my set for $10, they were old and slightly discolored but I could not care less! I took them home and used a drill and saber saw to remove the center ribbed area, theres several brands that are very similar in appearance, all will work! and Ive used them for over 25 years, if I remember correctly they are mickey thompson brand
now if the lifters are hydrolic of course you just back the adjustment nuts off the rocker studs with a wrench, slowly until the rocker JUST starts clicking , then slowly tighten the nut just up to the point that the clicking stops then add 1/4 to 3/8 turn to preload the lifter and move to the next rocker and repeat, the only differance with solid lifters is you use a feeler gauge inserted between the valve tip and rocker after they click slightly,to measure the lash distance recomended on the cam spec. card (normally .016-.028 thousands) and you tighten them just to the point at idle that the clicking stops... then you remove the feeler gauge and move to the next rocker
if your useing jam nuts dont forget to lock the allen key
Valve Adjustment: ENGINE OFF!
with #1 cylinder Intake Valve at full valve lift .... Adjust #6 Intake Valve
with #8 cylinder Intake Valve at full valve lift .... Adjust #5 Intake Valve
with #4 cylinder Intake Valve at full valve lift .... Adjust #7 Intake Valve
with #3 cylinder Intake Valve at full valve lift .... Adjust #2 Intake Valve
with #6 cylinder Intake Valve at full valve lift .... Adjust #1 Intake Valve
with #5 cylinder Intake Valve at full valve lift .... Adjust #8 Intake Valve
with #7 cylinder Intake Valve at full valve lift .... Adjust #4 Intake Valve
with #2 cylinder Intake Valve at full valve lift .... Adjust #3 Intake Valve
Exhaust Valve Adjustment: ENGINE OFF!
If you have noticed, this is the same procedure as the intake valves listed above, just that you are now adjusting the exhaust valves the same way.
with #1 cylinder Exhaust Valve at full valve lift .... Adjust #6 Exhaust Valve
with #8 cylinder Exhaust Valve at full valve lift .... Adjust #5 Exhaust Valve
with #4 cylinder Exhaust Valve at full valve lift .... Adjust #7 Exhaust Valve
with #3 cylinder Exhaust Valve at full valve lift .... Adjust #2 Exhaust Valve
with #6 cylinder Exhaust Valve at full valve lift .... Adjust #1 Exhaust Valve
with #5 cylinder Exhaust Valve at full valve lift .... Adjust #8 Exhaust Valve
with #7 cylinder Exhaust Valve at full valve lift .... Adjust #4 Exhaust Valve
with #2 cylinder Exhaust Valve at full valve lift .... Adjust #3 Exhaust Valve
or if your really lazy (you can use this method on hydraulic lifters)install the tall cut valve covers and just turn the engine about 20 degrees or 1/8th turn,(start anywhere )and take the slack out of any loose rockers, repeat for 720 degrees,(twice around) then go back and give each rocker nut one turn OUT(LOOSER) and start the engine,(yeah it will be messy and noisy) and then go back and turn each rocker IN (TIGHTER) until it just quits clicking plus 1/3rd of a turn past that point
BTW many chevy rocker studs use a thread pitch of about .040 thousands per turn so once your very familiar with your solid lifter engines needs and the cam lash clearance you need and once you verify the pitch rate of the threads you can adjust solids surprisingly close to correctly by running them in till they quit clicking, then OUT about 1/3-1/2 a turn to get the correct lash rather than IN like on a hydraulic lifter to add preload,naturally you'll need to verify with a feeler gauge.
NATURALLY you need to know the threads per inch on the rocker studs and a quick check with your calculator will give you the necessary info on the clearance a full turn of the adjustment nut advances or loosens the rocker, and be aware that this is not exact but a fast way to get close at the track
http://www.ratwell.com/technical/HydraulicLifters.html
standard hydraulic lifter
http://www.thedirtforum.com/chevyvalves.htm
http://www.2quicknovas.com/happyvalves.html
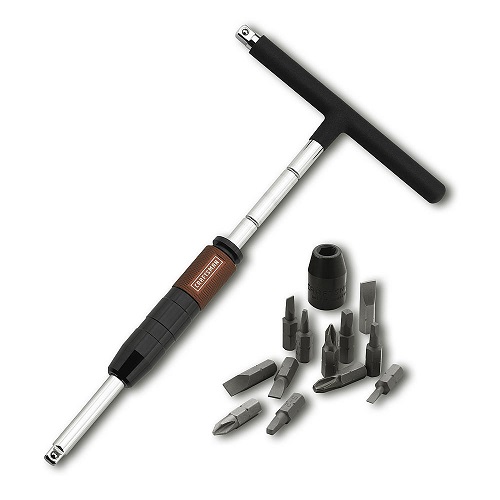
https://www.craftsman.com/products/craftsman-mach-series-14-piece-3-8-t-handle-driver-and-bit-set
http://www.centuryperformance.com/valveadjustment.asp
http://www.boostandfuel.com/support/setting_valves.htm
http://www.carcraft.com/techarticles/87998/index2.html
http://www.angelfire.com/fl4/pontiacdude428/valveadj.html
btw if your totally new at this the tappet feeler gauge measures the lash clearance between the valve and rocker on solid lifter cams
I just don,t think adjusting the valves without the oil pressure and the block up to operating temp. is the best way to adjust valves , but yes you can do it just fine with several methods discribed above
how do you adjust valves at idle without the mess of oil getting all over the engine and headers
HIT A FEW YARD SALES, SWAP MEETS UNTILL YOU FIND A DIRT CHEAP SET OF TALL CAST VALVE COVERS LIKE THESE, the CONDITION THEY ARE IN ,WITHIN REASONABLE LIMITS OF COURSE IS NOT THAT IMPORTANT
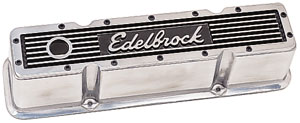
you simply cut the ribbed center section out of the valve cover, and glue the synthetic valve cover gaskets on them in the normal location,
when you go to adjust the valves you first remove the standard valve covers and install your VALVE ADJUSTMENT COVERS, they retain about 80%-90% of the oil that would normally be lost over the edge of the cylinder head while adjusting a running engine, they also catch much of the splashed oil, just leave a 1/4"-3/8" of the rolled top for strenth around the perimiter of the top surface. I bought my set for $10, they were old and slightly discolored but I could not care less! I took them home and used a drill and saber saw to remove the center ribbed area, theres several brands that are very similar in appearance, all will work! and Ive used them for over 25 years, if I remember correctly they are mickey thompson brand
now if the lifters are hydrolic of course you just back the adjustment nuts off the rocker studs with a wrench, slowly until the rocker JUST starts clicking , then slowly tighten the nut just up to the point that the clicking stops then add 1/4 to 3/8 turn to preload the lifter and move to the next rocker and repeat, the only differance with solid lifters is you use a feeler gauge inserted between the valve tip and rocker after they click slightly,to measure the lash distance recomended on the cam spec. card (normally .016-.028 thousands) and you tighten them just to the point at idle that the clicking stops... then you remove the feeler gauge and move to the next rocker
if your useing jam nuts dont forget to lock the allen key
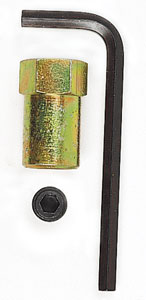
Valve Adjustment: ENGINE OFF!
with #1 cylinder Intake Valve at full valve lift .... Adjust #6 Intake Valve
with #8 cylinder Intake Valve at full valve lift .... Adjust #5 Intake Valve
with #4 cylinder Intake Valve at full valve lift .... Adjust #7 Intake Valve
with #3 cylinder Intake Valve at full valve lift .... Adjust #2 Intake Valve
with #6 cylinder Intake Valve at full valve lift .... Adjust #1 Intake Valve
with #5 cylinder Intake Valve at full valve lift .... Adjust #8 Intake Valve
with #7 cylinder Intake Valve at full valve lift .... Adjust #4 Intake Valve
with #2 cylinder Intake Valve at full valve lift .... Adjust #3 Intake Valve
Exhaust Valve Adjustment: ENGINE OFF!
If you have noticed, this is the same procedure as the intake valves listed above, just that you are now adjusting the exhaust valves the same way.
with #1 cylinder Exhaust Valve at full valve lift .... Adjust #6 Exhaust Valve
with #8 cylinder Exhaust Valve at full valve lift .... Adjust #5 Exhaust Valve
with #4 cylinder Exhaust Valve at full valve lift .... Adjust #7 Exhaust Valve
with #3 cylinder Exhaust Valve at full valve lift .... Adjust #2 Exhaust Valve
with #6 cylinder Exhaust Valve at full valve lift .... Adjust #1 Exhaust Valve
with #5 cylinder Exhaust Valve at full valve lift .... Adjust #8 Exhaust Valve
with #7 cylinder Exhaust Valve at full valve lift .... Adjust #4 Exhaust Valve
with #2 cylinder Exhaust Valve at full valve lift .... Adjust #3 Exhaust Valve
or if your really lazy (you can use this method on hydraulic lifters)install the tall cut valve covers and just turn the engine about 20 degrees or 1/8th turn,(start anywhere )and take the slack out of any loose rockers, repeat for 720 degrees,(twice around) then go back and give each rocker nut one turn OUT(LOOSER) and start the engine,(yeah it will be messy and noisy) and then go back and turn each rocker IN (TIGHTER) until it just quits clicking plus 1/3rd of a turn past that point
BTW many chevy rocker studs use a thread pitch of about .040 thousands per turn so once your very familiar with your solid lifter engines needs and the cam lash clearance you need and once you verify the pitch rate of the threads you can adjust solids surprisingly close to correctly by running them in till they quit clicking, then OUT about 1/3-1/2 a turn to get the correct lash rather than IN like on a hydraulic lifter to add preload,naturally you'll need to verify with a feeler gauge.
NATURALLY you need to know the threads per inch on the rocker studs and a quick check with your calculator will give you the necessary info on the clearance a full turn of the adjustment nut advances or loosens the rocker, and be aware that this is not exact but a fast way to get close at the track
http://www.ratwell.com/technical/HydraulicLifters.html
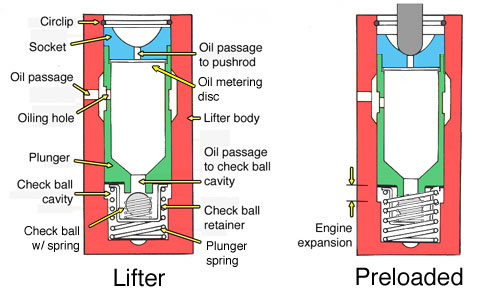
standard hydraulic lifter
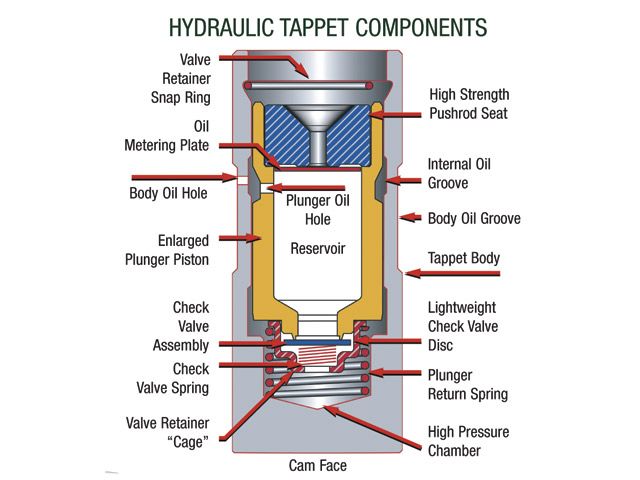
Last edited by a moderator: