Got a welding question. Need to weld new spring perches and shock tabs on a 3/4 ton truck rearend. Will a 130 amp 110VAC Mig welder turned all the way up have enough penetration or do I need "More Power?" (grunting)
A 110 volt mig is a great tool for sheet metal work and does a decent job on exhaust systems..... but its way out of its league in 1/4:-5/16" frames and suspension components..The bead will not usually have enough heat/penetration.
You will get what LOOKS like a good weld bead -with that 110 volt mig, but the bead will sit on the surface of the axle tube. One or two hard whacks from a ball peen hammer sideways and the weld bead will usually crack or pop off. It will have virtually no penetration
PROPER WELDS REQUIRE a GOOD DEAL OF HEAT, a rear axle assembly can take a great deal of heat to weld brackets correctly because of its mass and size it absorbs a great deal of heat easily before the surfaces flow correctly
IF YOUR NEW TO WELDING IN GENERAL THIS OLD THREAD MAY HELP
http://forums.hybridz.org/showthread.php?t=108912&highlight=tig
http://www.digitalcorvettes.com/forums/showthread.php?t=80762
http://www.digitalcorvettes.com/forums/showthread.php?t=80365
http://www.hobartbrothers.com/aboutus/downloads/
as were talking about that 110 volt mig....
I found this on a welder discusion thread, I thought it might help
Taken directly from a Joe Kalassa , a welding instructor from Lincoln Eletric
"“Some teams fail to achieve proper fusion, which basically happens, for instance, when you take a little 110-volt welding machine and work on heavy things like shock mounts,†Kolasa says. “Some people feel they can do anything they want with one of the smaller machines that is intended for thin materials. If you were to use that machine when it comes to something like a shock mount, you might as well skip welding it and just stick some bubble gum there instead because it won’t work. It’s a misunderstanding of the welding process that comes from a lack of education.â€
BTW my neighbor owns a lincoln 2300 weldpack 110 volt mig/flux welder
its decent for sheet metal repairs after you practice awhile....it will do up to about 1/4 mild steel if you can get to both sides of the seam, but its a joke on somethings like suspension brackets, it just can,t get the heat necessary to form a deep penetrating weld
__________________
example of defective welds, and WHY Id suggest a 220volt/180 amp brand name mig welder and welding class time as a good starting point
http://rides.webshots.com/video/3026513330101149359WVpyxw
acceptable in skilled hands
notice 3/16" suggested
http://www.welders-direct.com/merchant2/merchant.mv?Screen=PROD&Store_Code=WD&Product_Code=K2473-1
better
NOTICE 5/16" suggested
http://www.welders-direct.com/merchant2/merchant.mv?Screen=PROD&Store_Code=WD&Product_Code=907312
slight over kill but nice to have
http://www.welders-direct.com/merchant2/merchant.mv?Screen=PROD&Store_Code=WD&Product_Code=907324
not nearly necessary,for most stuff, but a great asset to a shop, and better with the aux aluminum feed gun,
(being a tool junky I spent the extra cash for the extra features and capacity)
http://www.welders-direct.com/merchant2/merchant.mv?Screen=PROD&Store_Code=WD&Product_Code=907321
you might want to just have a local machine shop with a decent TIG welder weld your brackets/new spring perches and shock tabs keep in mind TIG allows precise application of BOTH heat and fill material in a CONTROLLED manor as to the rates of each seperately.
with MIG your basically squirting molten wire into a joint,and the heats dependant in some degree to the rate the wires applied and the amps, theres less control of heat as the wire can only take so much ampereage before melting, with tig your electric ARC and heat are applied SEPERATELY from the fill rod, you can PREHEAT and REHEAT the joint and apply the fill rod only as needed, and at far higher HEAT levels in a smaller area than an oxy-acetolene torch.\
even a simple 220 volt 250 amp ARC/STICK welder may be VASTLY preferable to a small 110 volt mig in that application
http://www.welders-direct.com/merchant2/merchant.mv?Screen=PROD&Store_Code=WD&Product_Code=K1297
tig
http://www.twi.co.uk/j32k/protected/band_3/jk6.html
my MAIN shop welder for years was a simple arc welder, and it was used on countless spring purches, frames and brackets
http://www.welders-direct.com/merchant2/merchant.mv?Screen=PROD&Store_Code=WD&Product_Code=K1419-5
heres an old post that cover much of the info, LOOK THRU THE LINKS
a decent arc or stick welder will do a good deal of whats likely to need welding, an oxyacetolene torch is versital, a mig is really easy to master and a good tig will handle about anything you can name plus aluminum
http://www.twi.co.uk/j32k/protected/band_3/jk6.html
TIG (Tungsten Inert Gas Welding)

basically youve got a controlable electric arc in a gas shield that you use similar to a oxy-acetolene flame to melt the material and feed a rod of similar material to flow and join the peices
This process is the toughest to learn. The electrode is composed of Tungsten, and a current is flowed through it controlled by either a foot pedal, a hand switch, or a fixed current on the machine itself. I am learning TIG using a foot pedal, the more you press down on the metal, the more amps you get. Once you get enough current flowing to get an appropriate sized weld pool, you start dabbing a filler metal into the puddle as you move the electrode further down the work piece. TIG allows you a great amount of control because you regulate how much current the electrode gets and how much filler metal the weld pool gets. This process is very slow compared to the other types though. in my opinion its by far the best process simply because you can CONTROL BOTH THE HEAT POLARITY AND MATERIAL FEED CONSTANTLY MAKING ADJUSTMENTS IN BOTH SHOULD YOU CHOOSE
MIG - (Metal Inert Gas)
http://www.twi.co.uk/j32k/protected/band_3/jk4.html


MIG is the easiest process of welding. A feeding gun is used to feed a spool of filler metal wire into the weld pool. in effect you feed a charged wire into the weld are where it melts on contact due to the current arc ,Current is usually switched on and off by means of a trigger on the gun. Amps are usually controlled by a dial on the MIG machine itself, meaning that you cannot adjust current in the middle of welding. Though, with some machine you are able to get a foot pedal to control Amps while welding.the better machines allow you to vary the speed of the wire feed but you set the electrical energy (heat with a dial), its extremely fast and simple to use but your basicall shooting molten wire into the area to be welded.
Arc Welding (stick)
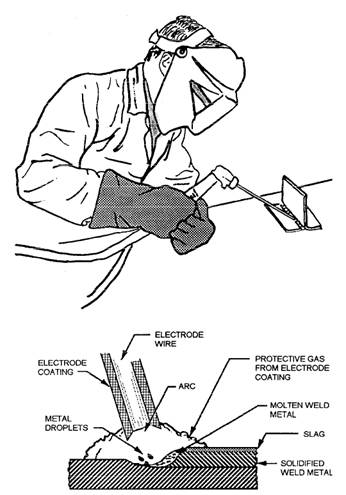
Arc welding is mostly used in industrial applications. An electrode is used to strike an arc, the electrode then melts away to deposit metal into the weld pool. The electrode is coated with a variety of different materials which are used to help keep the weld pool from being contaminated.
TIG and non-flux-cored MIG both use a variety of different shielding gases to help keep the weld pool from being contaminated depending on what metal is being welding
--------------------------------------------------------------------------------
Ive got 4 welders in my shop, the MILLER 330 amp TIG, I have uses ARGON.
but ID bet 70% of the welding get done with my lincoln arc welder, (like this below)
http://www.welders-direct.com/merchant2/merchant.mv?Screen=PROD&Store_Code=WD&Product_Code=K1419-4
ive got a LINCOLN MIG and a HOBART 210 amp also (soon to be replaced with a MILER 252 MIG)
example of how handy it is to have around, I welded up a heavy duty cart for the tig welder to hold the well over 700lbs and the tank of argon , total cost was less than $40 in steel and (4) $12 ...500 lb rated... 8" swivel roller wheels, the factory option cart was over $200
I saved at least $100 PLUS its a much better built cart
http://www.metalmeet.com/
http://www.hobartwelders.com/mboard/
http://www.millermotorsports.com/mboard/forumdisplay.php?f=3
http://www.htpweld.com/
http://www.lincolnelectric.com/
http://www.millerwelds.com/products/
BTW HAVE A GOOD FIRE EXTINGUISHER HANDY and while most of this is OBVIOUS to the more experianced guys, but your need to wear the correct gear and use common sence while welding
at a minimum wear a NON-SYNTHETIC ,(many synthetics melt instantly or are very flameable) VS(cotton, denim, and leather don,t generally flare or burn instantly ), wear long DENIM sleeve shirts, long leg slacks and sturdy leather boots,(cleated thick rubber soles that insulate helps) with the DENIM slacks OVER the boots not tucked loosely into open tops like cowboy boots and a use self darkening helmet, and wearing leather welders gloves and a reversed cotton baseball cap sure won,t hurt if your doing a good deal of welding, simply because YOU WILL EVENTUALLY get radiation burns (fairly quickly from the arc/flash of welding if you don,t ) on exposed skin,
(think of this as a bad sun burn, OR WORSE, that can happen in minutes in some cases) and repeated exposure too radiation burns is never a good idea.
and welders tend to create HEAT, sparks and falling bits of red hot metalic crud that makes sandels, short sleeve shirts and shorts a very dumb idea in most cases. keep a DECENT SIZE CO2 fire extinguisher handy, and a water hose with a spray nozzle that pressurized kept near by is a good idea.
never weld over your head if you can move the part to where you can weld at bench ;level, yeah! it takes longer to remove and install the parts like exhausts or mufflers and yeah! its not always practical, but both safety and weld quality benefit, so if you have the option weld on a bench vs the car!
THINK! before welding, HOT stuff falling on tender bits of your anatomy or starting the car on fires seldom FUN, and clamps, use of a barrier for shielding the stuff near the weld location with a wet towel or sheet of galvanized metal , use a GREAT GROUND, or in rare cases flowing water , it is only comon sence, but be aware that you can also get ELECTRICUTED if your REALLY DUMB, SO THINK IT THRU BEFORE you start, have a buddy help, and know what your doing, before you get in over your skill/knowledge level
if your useing an oxy-acetolene torch, make DAMN SURE the tanks are turned off before putting them away,and the fittings are tight and nothings leaking before use,and be sure local laws don,t prohibit you from home use of a oxy-acetolene welder