NOT A TA
reliable source of info
Since the Trans Am parts weren't getting picked up for a couple weeks I left them to fully cure before applying the nose bird sticker. I put the sticker on this past weekend to allow time to get another sticker before the pieces get picked up, just in case there was a problem with the sticker, or installer! ahaha Used some tape as register marks to make sure it was straight and used "Slide-On" application gel for large stickers. It came out nice and all the parts look good. I mounted the bumper to a piece of plywood in the hopes it helps keep the bumper from getting damaged before it gets installed. The board is a couple inches bigger than the bumper in all directions.
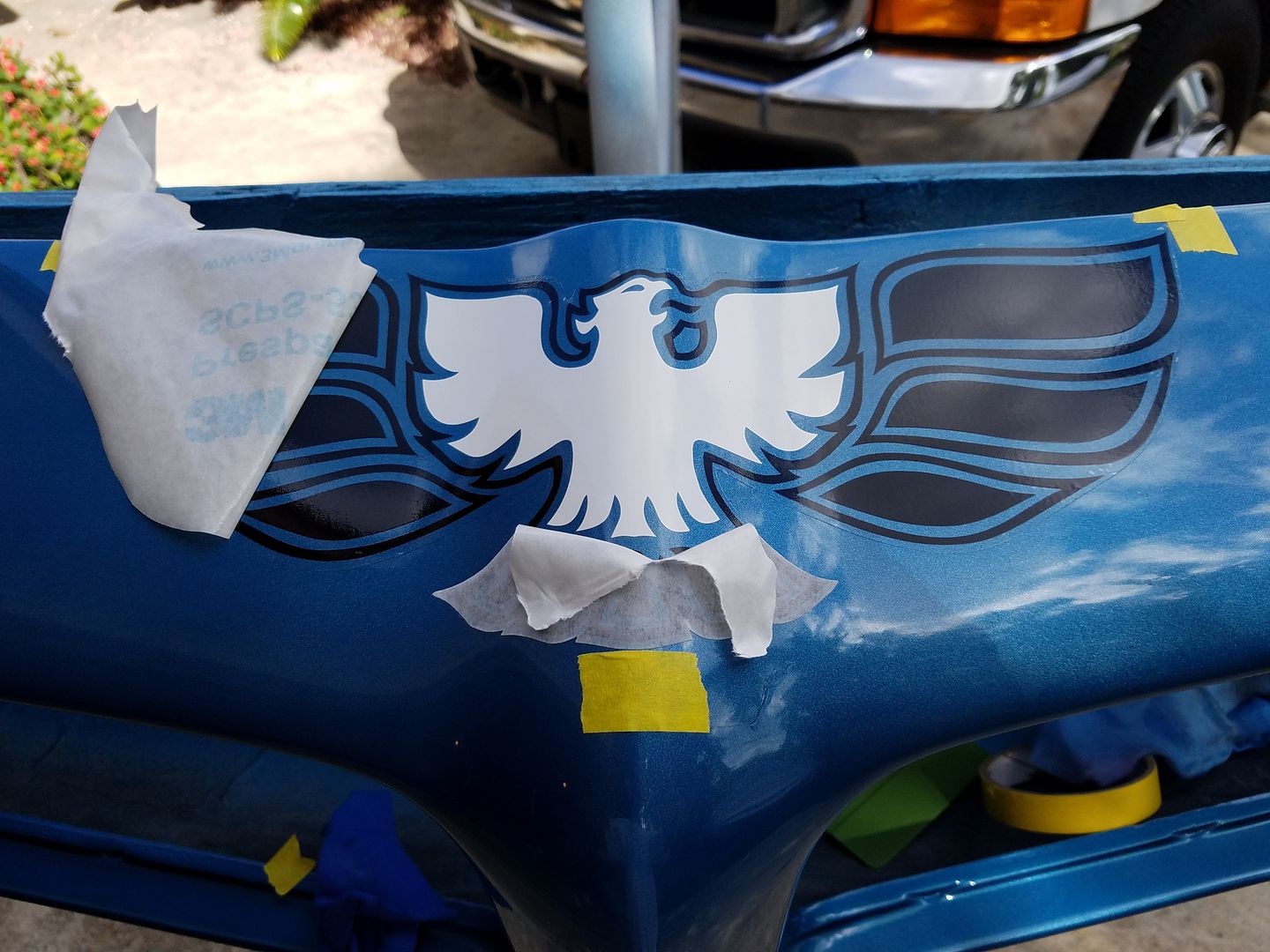
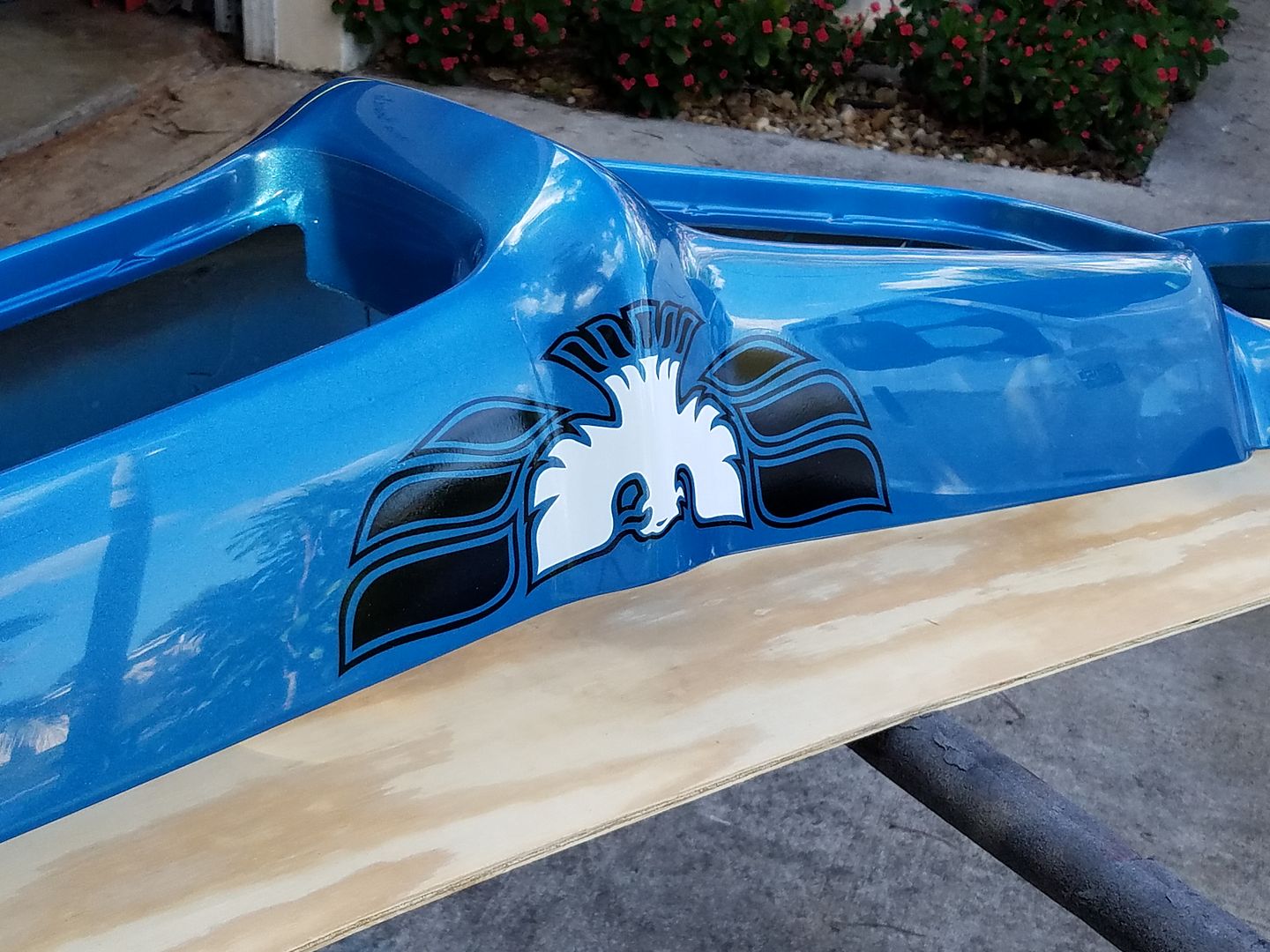
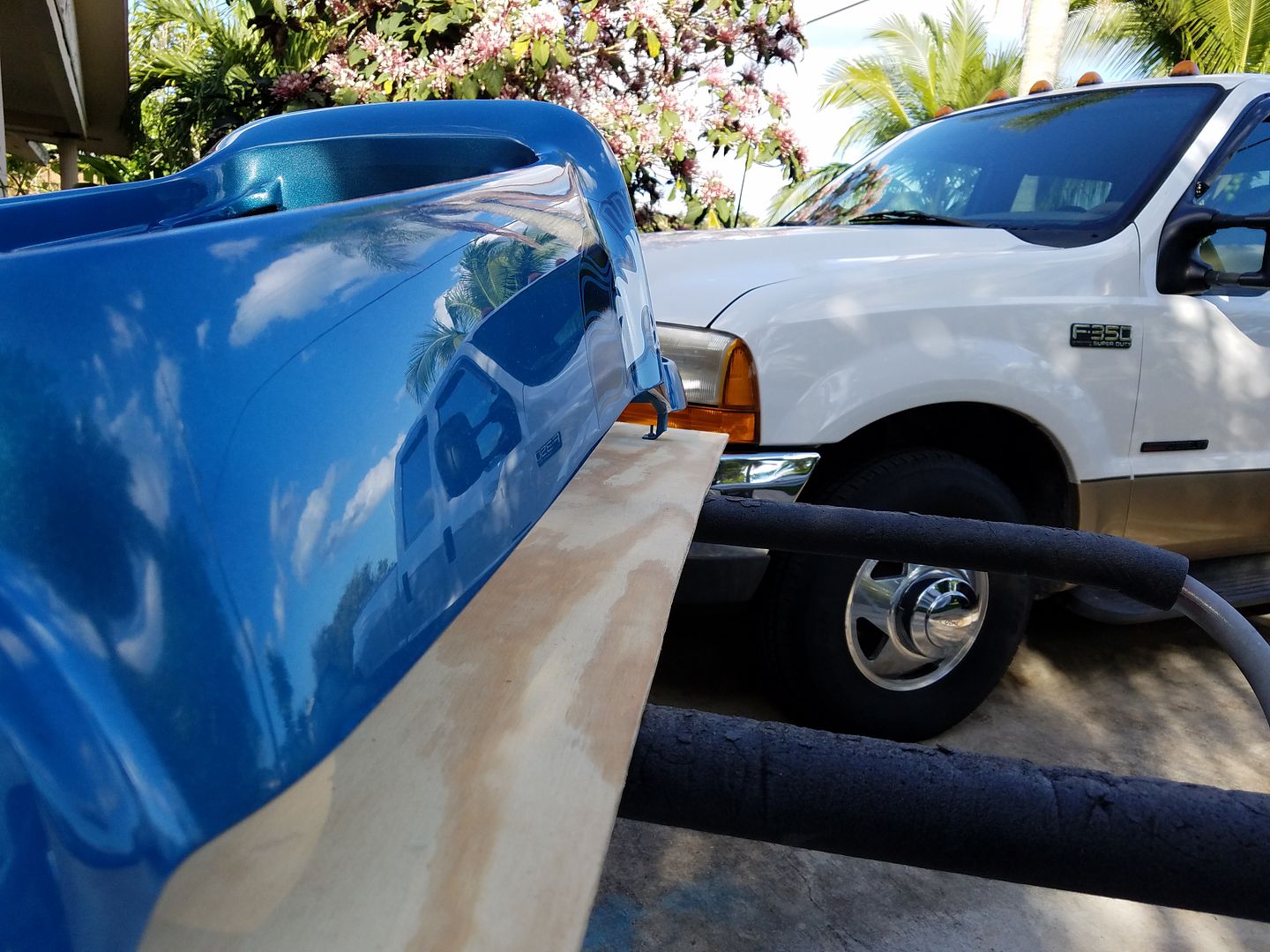
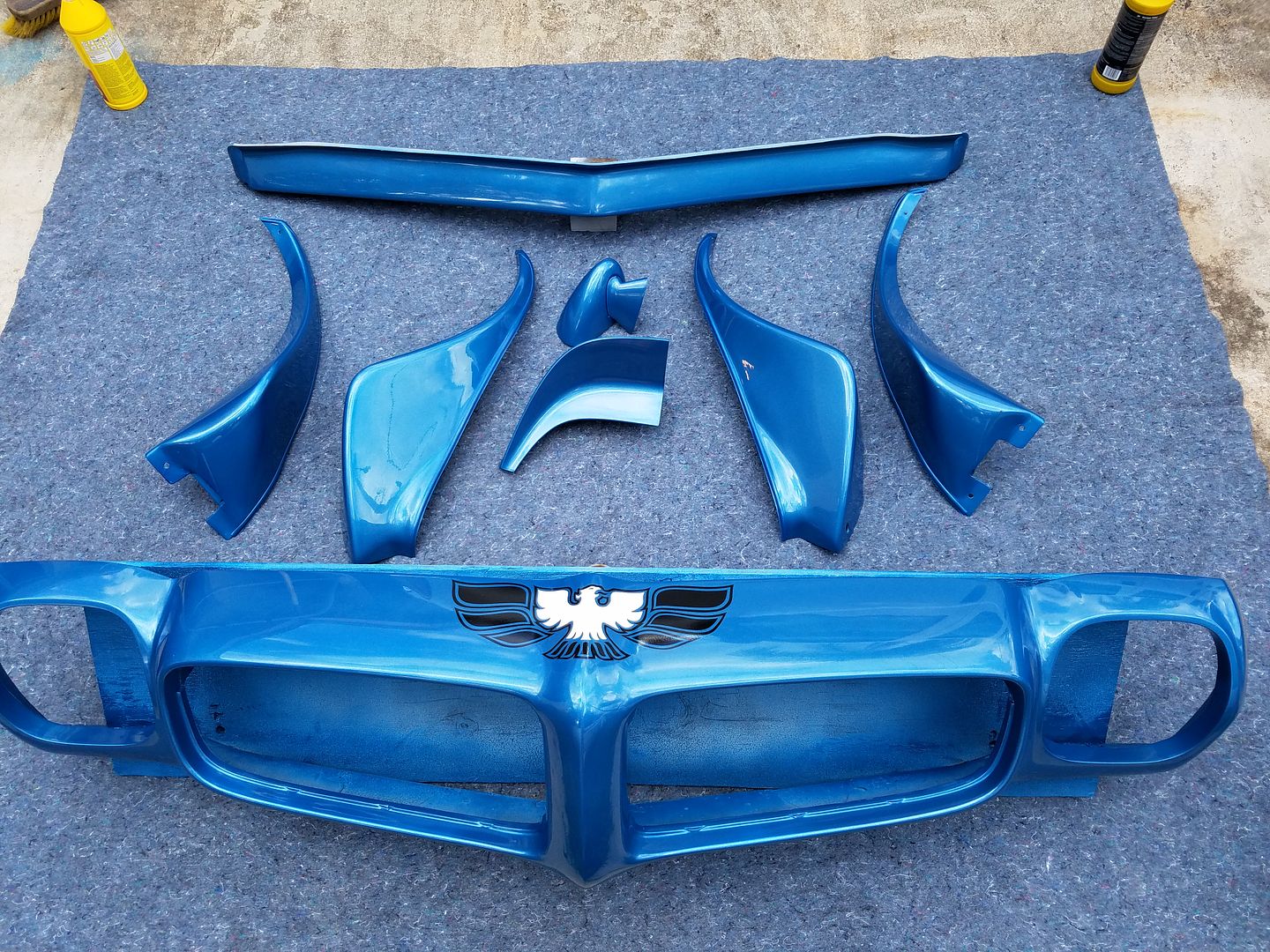
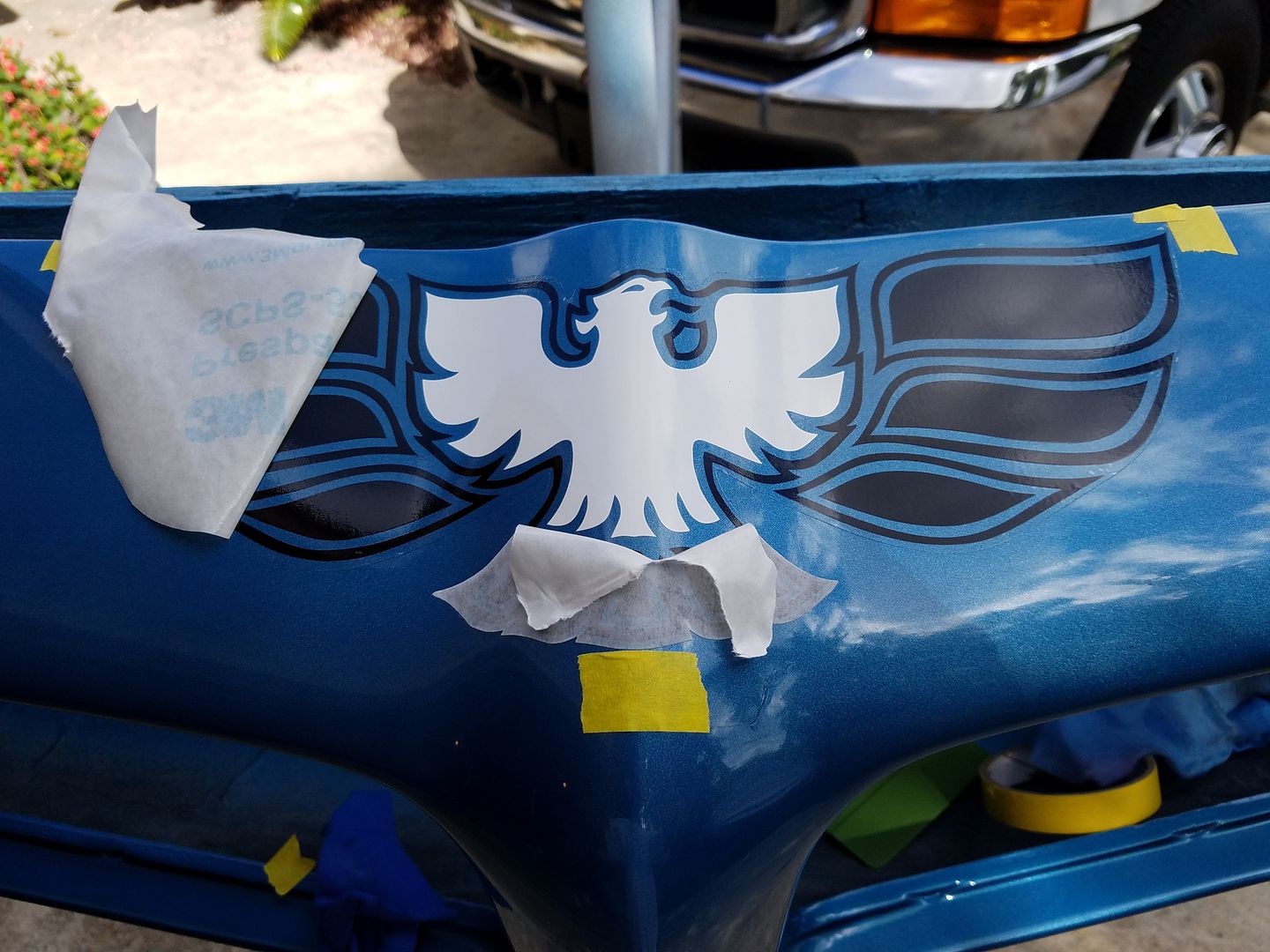
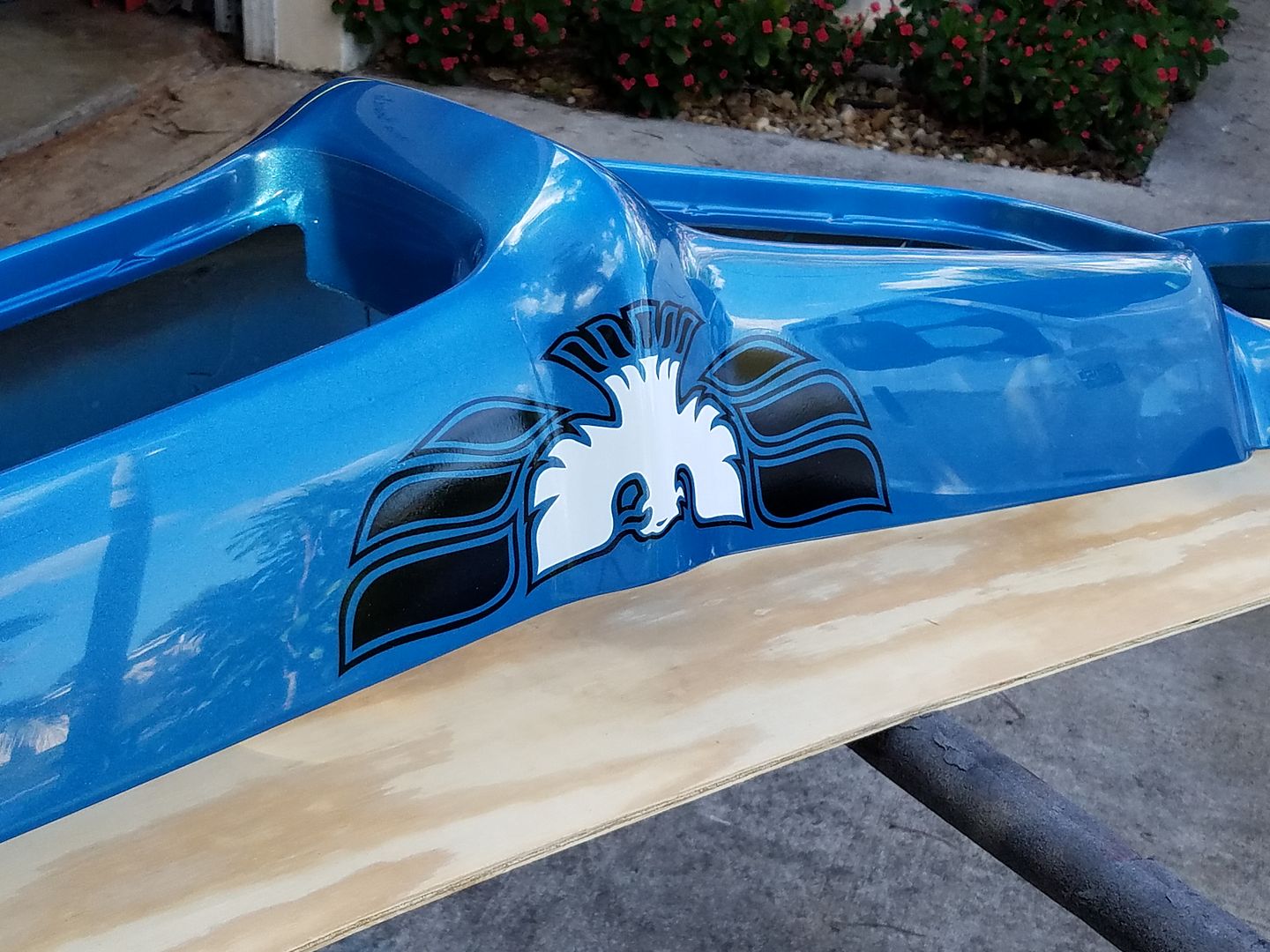
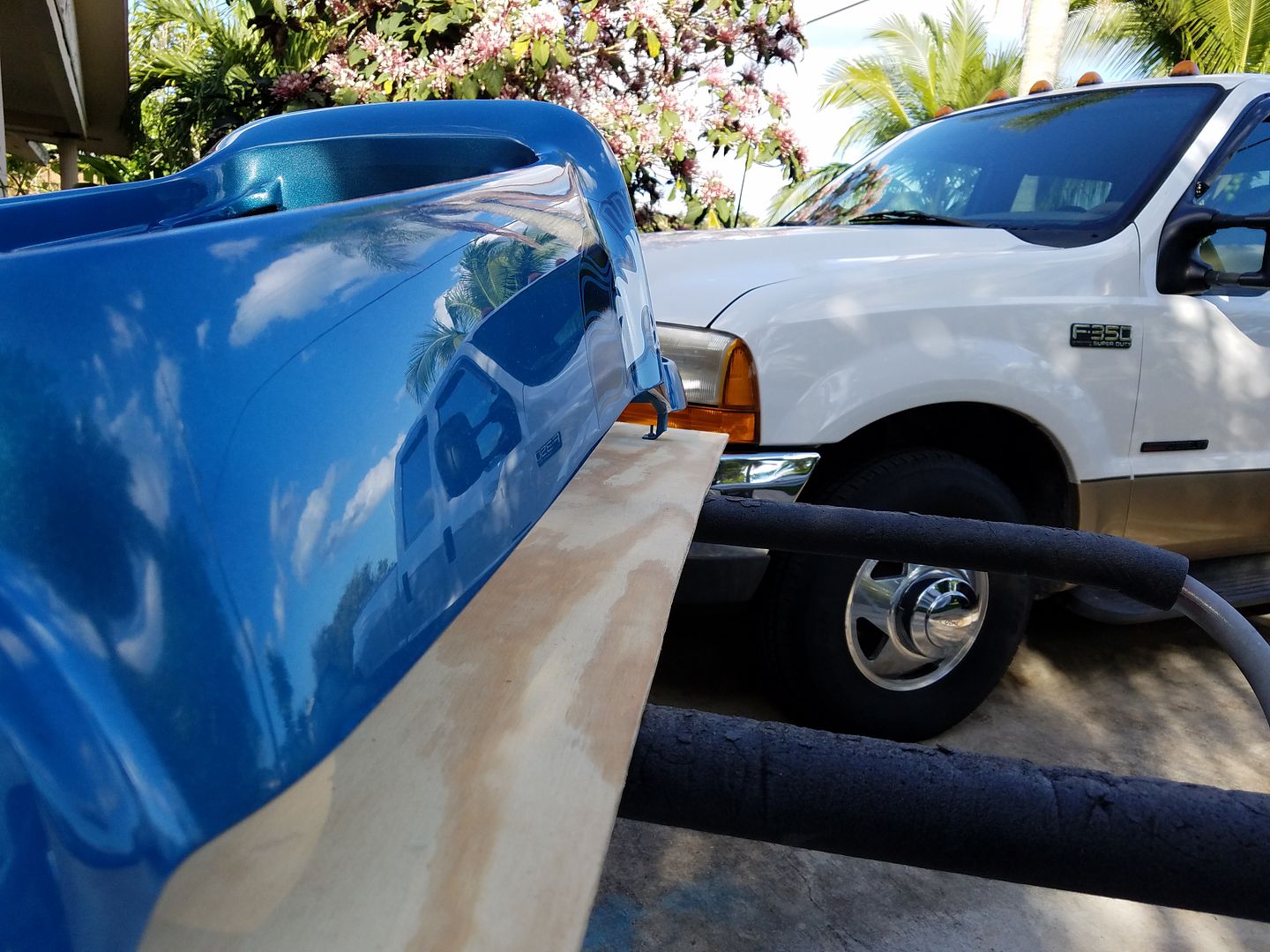
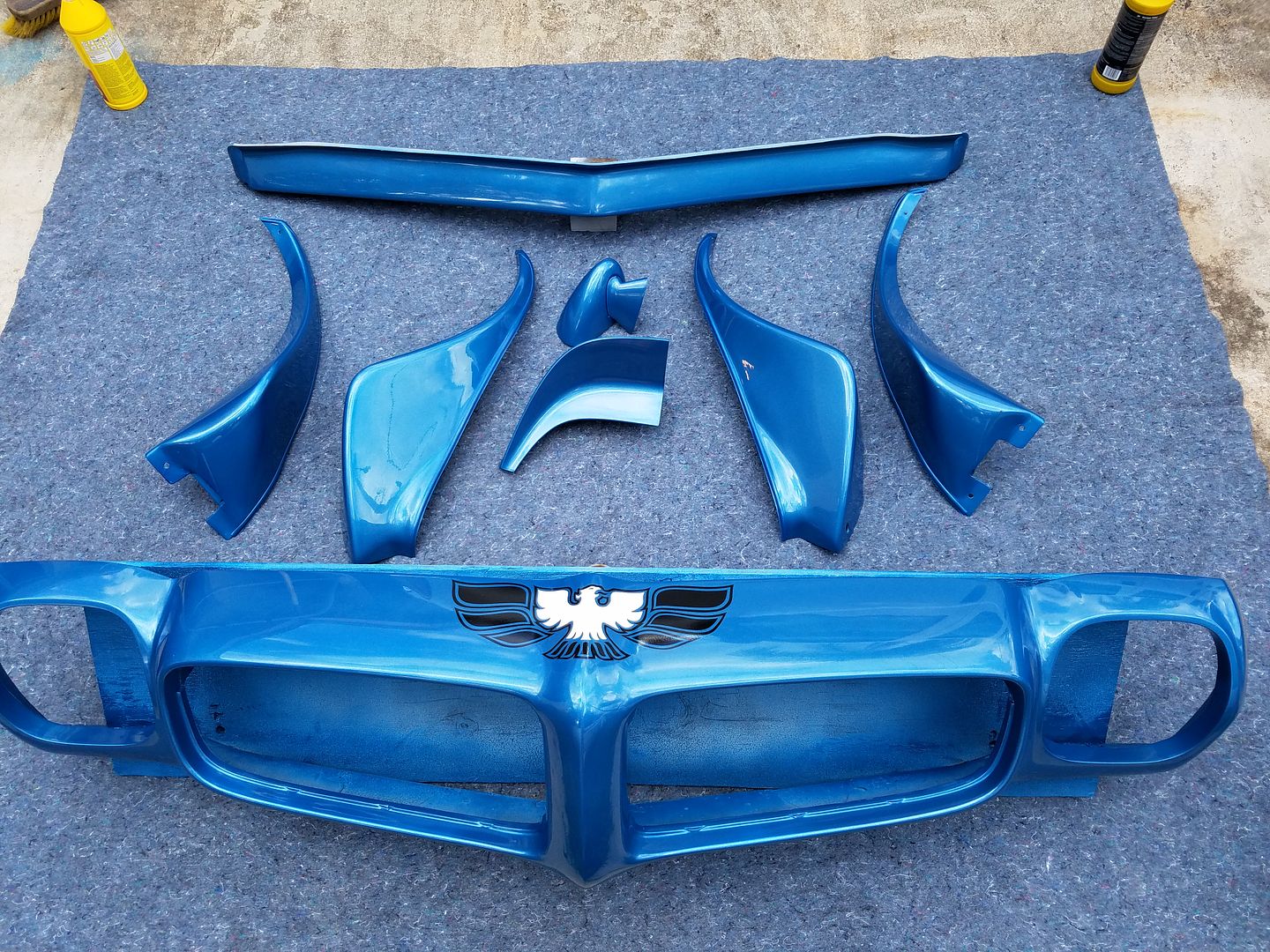