theres plenty of fluid dynamics math and research out there to show that the distances the exhaust travels between exhaust pulses and the diam. and length are easily calculated, and past that length the second previous pulse has little effect compared to the current and previous pulse energy and reflective wave
and lets not forget the cam timing displacement and intake port all effect the cylinder scavenging the headers can effectively provide also
heres some tools to help, if your building your own custom exhaust
http://www.metalgeek.com/static/cope.pcgi
http://pipemastertools.com/store/page1.html
http://www.engr.colostate.edu/~allan/fluids/page7/PipeLength/pipe.html
http://www.rbracing-rsr.com/runnertorquecalc.html
http://www.veryuseful.com/mustang/tech/ ... enging.pdf
http://victorylibrary.com/mopar/header-tech-c.htm
http://www.headerdesign.com/
http://www.pontiacracing.net/js_header_length1.htm
http://www.slowgt.com/Calc2.htm#Header
what goes in needs to exit with minimal flow restriction, an (X) pipe and dual 3" exhaust helps
http://garage.grumpysperformance.com/index.php?threads/calculating-header-design.185/
USE THE CALCULATORS to match port size to intended rpm levels... but keep in mind valve lift and port flow limitations
http://www.wallaceracing.com/runnertorquecalc.php
http://www.wallaceracing.com/ca-calc.php
http://www.wallaceracing.com/area-under-curve.php
http://www.wallaceracing.com/chokepoint.php
http://www.wallaceracing.com/header_length.php
http://www.circletrack.com/enginetech/1 ... ch_engine/
http://www.pontiacracing.net/js_header_length1.htm
http://www.wallaceracing.com/header_length.php
http://www.wallaceracing.com/Calculators.htm
https://robrobinette.com/et.htm
https://www.gregraven.org/hotwater/calculators/qm-from-wt-hp.php
http://www.bgsoflex.com/auto.html
http://www.mk5cortinaestate.co.uk/calculator5.php
http://www.can-of-whoopass.com/index.php?pageID=car_stuff&calculator=primaries
example , my 383 vette has a cam with exhaust cam timing that opens at 83degs bbdc, thats 97 degs atdc, http://www.cranecams.com/?show=browseParts&action=partSpec&partNumber=119661&lvl=2&prt=5
Bore: (Inches) 4.03"<BR>Exhaust Valve Opening Point: (Degrees ATDC) 97 degs
Peak Power RPM: 5500rpm Calculated information appears below
Header Pipe Diameter: (Inches) 1.84"<
Header Pipe Length: (Inches) 37.65
Collector Diameter: (Inches) 3.5
Collector Length: (Inches) 18.82
so ideally the (X) is placed at that point to maximize scavenging but that's not always possible due to clearance, and if you choose to place an (H) just before the mufflers its mostly to reduce resonance or noise not increase scavenging but it tends to reduce the restriction to flow
http://www.team-integra.net/sections/articles/showArticle.asp?ArticleID=50
"I could put BOTH and X and an H- pipe in the system.
Would this be a waste of effort???
Does the H-pipe equalize the pulses to the extent that a downstream X-pipe no longer functions as it should?"
if you place TWO it tends to mellow the exhaust tone and reduce resonance in the car and depending on the location and pipe diam. and length it usually does help the cylinder scavenging a bit more than one alone, but again the closer to the exhaust headers the better off you'll be and ideally the (X) should be closer to the engine than the (H) but that being said up front, I installed an 3"(H) just behind/under the bell housing rear , where the headers ended,and a second 3"(H) just in front of the mufflers on a friends GTO 3" full exhaust and a very nice rumble/lopey idle and a good wide power curve for his 455 pontiac was the result, were both pleased
you may want to keep in mind the HEADERS and the primairy diam. amd length and the collector design are what effects the cylinder scavaging , the exhaust past that is basically designed to supply a level of noise reduction and a low resistance to flow path for the exhaust to safely exit the car, if the headers are designed correctly the engines exhaust system past the collectors just needs to be designed to reduce noise and provide that low resistance exit path.
the (H) or(X) reduces the restriction to flow and blends the exhaust pulses to reduce the noise, if the exhaust past the collector does act as a collector extension on the headers is usually a bit smaller and restrictive than ideal.
in an ideal world the restriction to flow past the header collector would be very similar to running open headers and the main function of the exhaust would be only noise reduction, and exiting the exhaust where it would not re-enter the crew compartment. but the truth is most exhaust system pipes are too small in dia. to allow that so the (h) or (X) provides a way to reduce flow restriction by increasing the cross sectional area of the exhaust path,and blend and cancel out the pulses that make the noise
the IDEA of the (H) pipe is to allow some of the flow mass in the orrignating flow route to exit the original exhaust thus lowering the resistance,to flow the restriction presented by the single pipes cross sectional area provided,and pressure dropping off,and due to a significant percentage of that mass exiting and taking the lower resistance secondary route lowers pressure and the disruption of the sound waves tends to lower the sound of the exhaust also.
keep in mind properly designed headers and collectors provide the cylinder scavenging and there length and dimensions are calculated to maximize that scavenging effect the exhaust past the collectors is basically designed for noise abatement and safely exiting the exhaust gases.
you get very little scavenging effect from anything past the collectors if the systems designed correctly.
you might also consider the fact that flow restriction tends to increase with the rpm band, your stock exhaust is probably fine at the 1500rpm-4000rpm band it was designed for but when your expecting to zing the rpms up in the 4500rpm-6500rpm or above range the headers and collectors, and exhaust behind them,that are used effect a much bigger part of the potential power curve
__________
________most guys I talk and deal with,seem to think that slapping a set of headers on their car is all that's required to boost performance....ANY HEADERS! ...and they fail to realize that both the header design and the exhaust system behind them require a good deal of thought if you want the maximum benefits, and that simply hooking a restrictive exhaust system to the collectors on the best headers will negate most of their potential benefits.
most commercial headers are designed mostly for ease of manufacturing and ease of installation,little thought goes into maximizing the cylinder scavenging which is their main function.
your fooling yourself if you think headers will provide a big boost in hp/tq without the low restriction exhaust behind them,and in most cases that requires a larger diam. exhaust system and adding an (X) to the system and extending the header collectors at their full diam. up till at least the exit of the (X) so the twin exhaust pipes cross sectional area can provide that reduced restriction to flow, rather than the reducers many guys install to the collector exits to adapt them to the stock exhaust system
If your wondering why exhaust valves are smaller and exhaust ports normally flow less, its because they are flow rated with the same flow bench and at the same pressure drop as the intake ports (normally at 28" of water) your not alone in that question.
but EXHAUST PORTS operate in the real world at far higher pressure than intake ports do which alters the resulting flow significantly
the reason is that unlike the intake charge thats forced in by outside air pressure when the valves open on a cylinder with a lower than the outside air pressure, because the the pistons descending, and rapidly creating a partial vacuum which basically is limited to 14.7 psi at sea level change in internal vs external pressure to fill the cylinders the exhaust has THREE separate processes helping the exhaust exit
ONE
the burnt cylinder gases are under far greater pressure, easily 300psi-600psiwhen the valve opens
TWO
the piston on the exhaust stroke physically forces out the gases as it rotates to TDC, sweeping the cylinder volume out the exhaust
three
the headers if tuned correctly have a low pressure wave pulse bouncing back to reach the exhaust valve as it opens to help scavenge, and drag out the exhaust as it try's to follow the inertia of the previous exhaust pulse.
http://www.auto-ware.com/combust_bytes/pv.htm
http://performancetrends.com/blog/?p=53
read these links
http://www.popularhotrodding.com/engine ... index.html
http://autoclub.rso.siuc.edu/frange.html
viewtopic.php?f=56&t=1303&hilit=coke
http://www.pontiacstreetperformance.com ... haust.html
viewtopic.php?f=56&t=260
viewtopic.php?f=56&t=789
example of a well laid out exhaust (MELROSE)
but even that system could be hurt if you slap restrictive mufflers on it
a well thought thru design on an (X) pipe and cut outs
and lets not forget the cam timing displacement and intake port all effect the cylinder scavenging the headers can effectively provide also
heres some tools to help, if your building your own custom exhaust
http://www.metalgeek.com/static/cope.pcgi
http://pipemastertools.com/store/page1.html
http://www.engr.colostate.edu/~allan/fluids/page7/PipeLength/pipe.html
http://www.rbracing-rsr.com/runnertorquecalc.html
http://www.veryuseful.com/mustang/tech/ ... enging.pdf
http://victorylibrary.com/mopar/header-tech-c.htm
http://www.headerdesign.com/
http://www.pontiacracing.net/js_header_length1.htm
http://www.slowgt.com/Calc2.htm#Header
what goes in needs to exit with minimal flow restriction, an (X) pipe and dual 3" exhaust helps
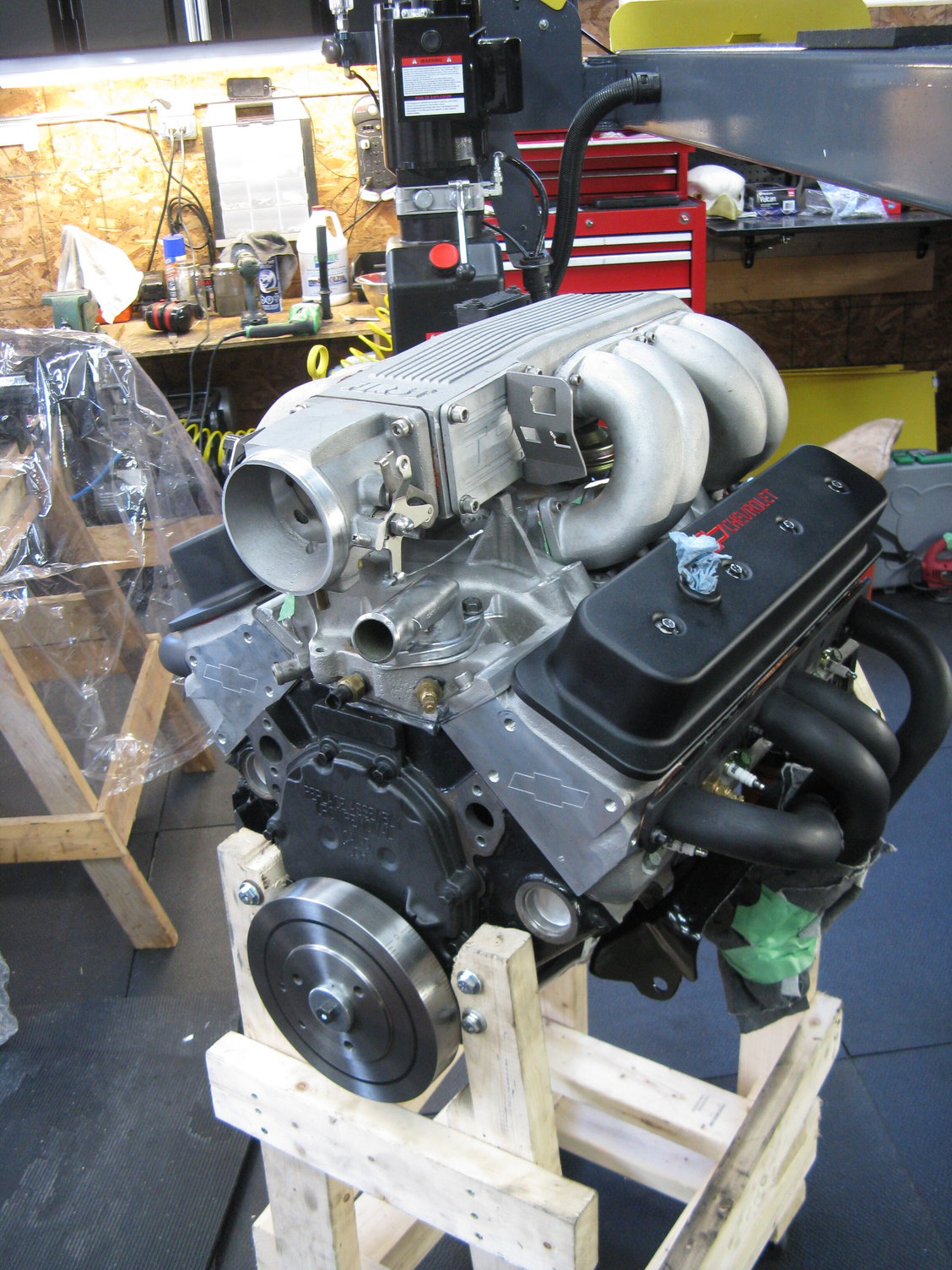
http://garage.grumpysperformance.com/index.php?threads/calculating-header-design.185/
USE THE CALCULATORS to match port size to intended rpm levels... but keep in mind valve lift and port flow limitations
http://www.wallaceracing.com/runnertorquecalc.php
http://www.wallaceracing.com/ca-calc.php
http://www.wallaceracing.com/area-under-curve.php
http://www.wallaceracing.com/chokepoint.php
http://www.wallaceracing.com/header_length.php
http://www.circletrack.com/enginetech/1 ... ch_engine/
http://www.pontiacracing.net/js_header_length1.htm
http://www.wallaceracing.com/header_length.php
http://www.wallaceracing.com/Calculators.htm
https://robrobinette.com/et.htm
https://www.gregraven.org/hotwater/calculators/qm-from-wt-hp.php
http://www.bgsoflex.com/auto.html
http://www.mk5cortinaestate.co.uk/calculator5.php
http://www.can-of-whoopass.com/index.php?pageID=car_stuff&calculator=primaries
example , my 383 vette has a cam with exhaust cam timing that opens at 83degs bbdc, thats 97 degs atdc, http://www.cranecams.com/?show=browseParts&action=partSpec&partNumber=119661&lvl=2&prt=5
Bore: (Inches) 4.03"<BR>Exhaust Valve Opening Point: (Degrees ATDC) 97 degs
Peak Power RPM: 5500rpm Calculated information appears below
Header Pipe Diameter: (Inches) 1.84"<
Header Pipe Length: (Inches) 37.65
Collector Diameter: (Inches) 3.5
Collector Length: (Inches) 18.82
so ideally the (X) is placed at that point to maximize scavenging but that's not always possible due to clearance, and if you choose to place an (H) just before the mufflers its mostly to reduce resonance or noise not increase scavenging but it tends to reduce the restriction to flow
http://www.team-integra.net/sections/articles/showArticle.asp?ArticleID=50
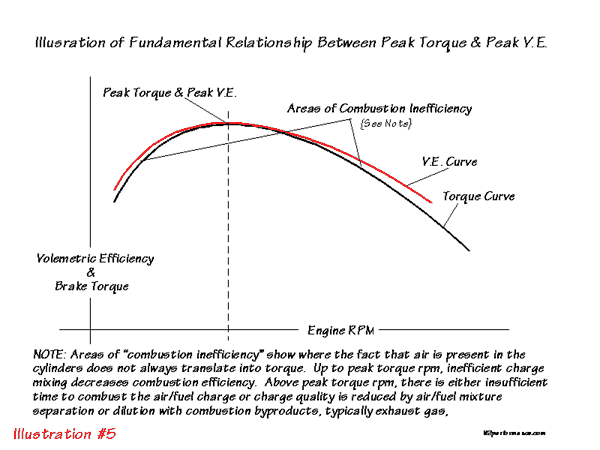
"I could put BOTH and X and an H- pipe in the system.
Would this be a waste of effort???
Does the H-pipe equalize the pulses to the extent that a downstream X-pipe no longer functions as it should?"
if you place TWO it tends to mellow the exhaust tone and reduce resonance in the car and depending on the location and pipe diam. and length it usually does help the cylinder scavenging a bit more than one alone, but again the closer to the exhaust headers the better off you'll be and ideally the (X) should be closer to the engine than the (H) but that being said up front, I installed an 3"(H) just behind/under the bell housing rear , where the headers ended,and a second 3"(H) just in front of the mufflers on a friends GTO 3" full exhaust and a very nice rumble/lopey idle and a good wide power curve for his 455 pontiac was the result, were both pleased
you may want to keep in mind the HEADERS and the primairy diam. amd length and the collector design are what effects the cylinder scavaging , the exhaust past that is basically designed to supply a level of noise reduction and a low resistance to flow path for the exhaust to safely exit the car, if the headers are designed correctly the engines exhaust system past the collectors just needs to be designed to reduce noise and provide that low resistance exit path.
the (H) or(X) reduces the restriction to flow and blends the exhaust pulses to reduce the noise, if the exhaust past the collector does act as a collector extension on the headers is usually a bit smaller and restrictive than ideal.
in an ideal world the restriction to flow past the header collector would be very similar to running open headers and the main function of the exhaust would be only noise reduction, and exiting the exhaust where it would not re-enter the crew compartment. but the truth is most exhaust system pipes are too small in dia. to allow that so the (h) or (X) provides a way to reduce flow restriction by increasing the cross sectional area of the exhaust path,and blend and cancel out the pulses that make the noise
the IDEA of the (H) pipe is to allow some of the flow mass in the orrignating flow route to exit the original exhaust thus lowering the resistance,to flow the restriction presented by the single pipes cross sectional area provided,and pressure dropping off,and due to a significant percentage of that mass exiting and taking the lower resistance secondary route lowers pressure and the disruption of the sound waves tends to lower the sound of the exhaust also.
keep in mind properly designed headers and collectors provide the cylinder scavenging and there length and dimensions are calculated to maximize that scavenging effect the exhaust past the collectors is basically designed for noise abatement and safely exiting the exhaust gases.
you get very little scavenging effect from anything past the collectors if the systems designed correctly.
you might also consider the fact that flow restriction tends to increase with the rpm band, your stock exhaust is probably fine at the 1500rpm-4000rpm band it was designed for but when your expecting to zing the rpms up in the 4500rpm-6500rpm or above range the headers and collectors, and exhaust behind them,that are used effect a much bigger part of the potential power curve
__________
________most guys I talk and deal with,seem to think that slapping a set of headers on their car is all that's required to boost performance....ANY HEADERS! ...and they fail to realize that both the header design and the exhaust system behind them require a good deal of thought if you want the maximum benefits, and that simply hooking a restrictive exhaust system to the collectors on the best headers will negate most of their potential benefits.
most commercial headers are designed mostly for ease of manufacturing and ease of installation,little thought goes into maximizing the cylinder scavenging which is their main function.
your fooling yourself if you think headers will provide a big boost in hp/tq without the low restriction exhaust behind them,and in most cases that requires a larger diam. exhaust system and adding an (X) to the system and extending the header collectors at their full diam. up till at least the exit of the (X) so the twin exhaust pipes cross sectional area can provide that reduced restriction to flow, rather than the reducers many guys install to the collector exits to adapt them to the stock exhaust system
If your wondering why exhaust valves are smaller and exhaust ports normally flow less, its because they are flow rated with the same flow bench and at the same pressure drop as the intake ports (normally at 28" of water) your not alone in that question.
but EXHAUST PORTS operate in the real world at far higher pressure than intake ports do which alters the resulting flow significantly
the reason is that unlike the intake charge thats forced in by outside air pressure when the valves open on a cylinder with a lower than the outside air pressure, because the the pistons descending, and rapidly creating a partial vacuum which basically is limited to 14.7 psi at sea level change in internal vs external pressure to fill the cylinders the exhaust has THREE separate processes helping the exhaust exit
ONE
the burnt cylinder gases are under far greater pressure, easily 300psi-600psiwhen the valve opens
TWO
the piston on the exhaust stroke physically forces out the gases as it rotates to TDC, sweeping the cylinder volume out the exhaust
three
the headers if tuned correctly have a low pressure wave pulse bouncing back to reach the exhaust valve as it opens to help scavenge, and drag out the exhaust as it try's to follow the inertia of the previous exhaust pulse.

http://www.auto-ware.com/combust_bytes/pv.htm
http://performancetrends.com/blog/?p=53
read these links
http://www.popularhotrodding.com/engine ... index.html
http://autoclub.rso.siuc.edu/frange.html
viewtopic.php?f=56&t=1303&hilit=coke
http://www.pontiacstreetperformance.com ... haust.html
viewtopic.php?f=56&t=260
viewtopic.php?f=56&t=789
example of a well laid out exhaust (MELROSE)

but even that system could be hurt if you slap restrictive mufflers on it
a well thought thru design on an (X) pipe and cut outs
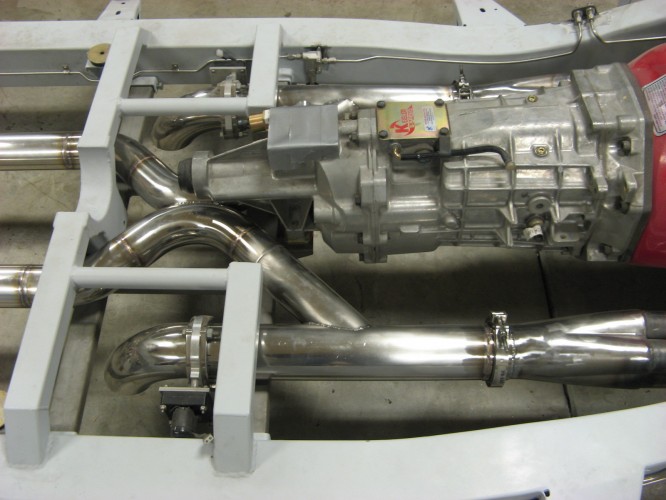
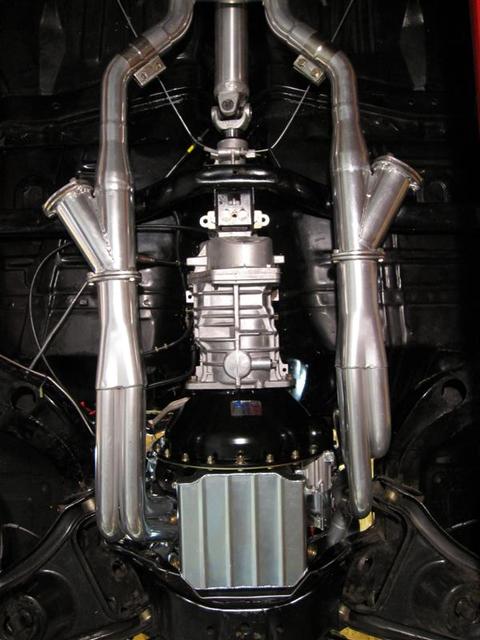
Last edited by a moderator: