Here is a pic of bearings out of a 327 that came in because of poor leak down tests (THAT WERE POSTED ON A DIFFERENT SITE) only to find it was not plate honed and when we tool off the mains caps this is what we found and this engine only had 400 miles on it.
for some bearings to wear down to the copper backing in the bearing shell while others remain basically untouched indicates a clearance or straightness or binding issue, bearings wear due to lack of lubrication, or clearance problems, now it might be as simple as the bearing shell was cocked in it seat, the main cap was not seated fully,that journal was out of round or over sized, the bearing was bent, or dirt under the shell but theres a reason the bearing wore in that way and the others didn,t, that needs to be looked into.
If the blocks been correctly line honed and the cranks strait Id be looking closely at the journals tapper,surface Finish, run-out and diam. to the central axis concentrically
ok, lets explain that a bit,the basic fact is that for bearings to wear at a different rate in the same engine theres obviously a difference in the clearances, or loads on those bearings surface, from one section to the other or oil flow or the conditions under, which they operate, in an ideal world a barrier film of high pressure oil prevents direct metal to metal contact, between the journals and bearings supporting them.
the journals on the crank, need to be exactly the same diameter from one end to the other and the center of the journal needs to be a consistent distance from the outer surface, it might help if you think of the journal as a beer can and the central axis as a string stretched thru the beer can strung thru two holes drilled in the exact center of each end, then think of what would happen if on one end the holes centered but on the other its a couple thousands off center, the off center end will track in a different rotational arc , , the effective stroke will be slightly longer or shorter or the rod will tend to bear far more load on one side than the other.
if the journal surface is slightly curved or barrel shaped or tapered or slightly hour glass shaped it causes, differences in the working clearances, effective oil flow rates, cooling and problems for the engine maintaining its supporting oil film at consistent pressures and the ability to keep the journal and bearing surfaces from contacting each other.
READ THIS THREAD
viewtopic.php?f=53&t=1168
these might also help
http://www.thirskauto.net/BearingPics.html
viewtopic.php?f=53&t=88&p=112#p112
http://www.bobistheoilguy.com/bearingwe ... alysis.htm
http://web.applied.com/site.cfm/Causeso ... ailure.cfm
you might want to read thru these threads as checking your filter will generally indicate bearing wear before you get other indications like lower oil pressure
viewtopic.php?f=54&t=938
viewtopic.php?f=53&t=204
viewtopic.php?f=54&t=615&hilit=+filter
viewtopic.php?f=54&t=150
viewtopic.php?f=54&t=117
Notes: You will still find some full-grooved main sets offered for older engines where demand is low and the engineering cost to bring the sets to current standards is not warranted (bearings generally represent the technology of the time the engine was developed).
Manufacturers are frequently asked what difference grooving makes. Various forms of main bearing grooving have been used over the years.
It’s essential to understand that bearings depend on a film of oil to keep them separated from the shaft surface. This oil film is developed by shaft rotation. As the shaft rotates, it pulls oil into the loaded area of the bearing and rides up on this film much like a tire hydroplaning on wet pavement.
Grooving in a bearing acts like tread in a tire to break up the oil film. While you want your tires to grip the road, you don’t want your bearings to grip the shaft, so grooving is bad for maintaining an oil film. The primary reason for having any grooving in a main bearing is to provide oil to the connecting rods. Without rod bearings to feed, a simple oil hole would be sufficient to lubricate a main bearing.
Many early engines used full grooved bearings and some even used multiple grooves. Those choices were based on what engineers knew at the time. As engine and bearing technology developed, the negative effect of grooving was recognized and bearing grooving was removed from modern lower main bearings. The result is in a thicker film of oil for the shaft to ride on.
This provides a greater safety margin and improved bearing life. Upper main shells, which see lower loads than the lowers, and hence don’t apply the same load to the oil film, have retained a groove to supply the connecting rods with oil.
In an effort to develop the best possible main bearing designs for high performance engines, manufacturers have investigated the effects of main bearing grooving on bearing performance. The graphs (Figure 1) illustrate that a simple 180° groove in the upper main shell is still the best overall design.
While a slightly shorter groove of 140° provides a marginal gain, most of the benefit is to the upper shell, which doesn’t need improvement. On the other hand, extending the groove into the lower half, even as little as 20° at each parting line (220° in total), takes away from upper bearing performance without providing any benefit to the lower half. It’s also interesting to note that as groove length increases so does horsepower loss and peak oil film pressure, which is transmitted directly to the bearing.
Notes: You will still find some full-grooved main sets offered for older engines where demand is low and the engineering cost to bring the sets to current standards is not warranted (bearings generally represent the technology of the time the engine was developed).
Tech Tip courtesy of MAHLE Clevite Inc.
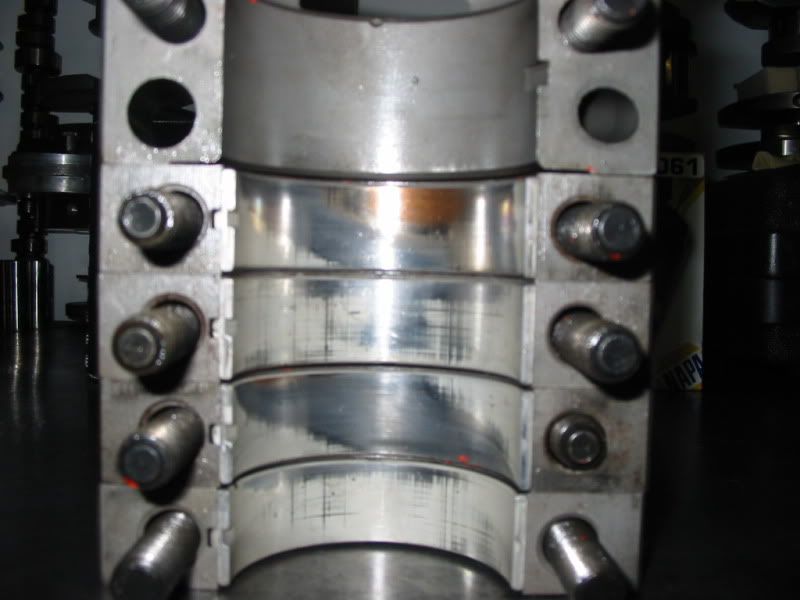
for some bearings to wear down to the copper backing in the bearing shell while others remain basically untouched indicates a clearance or straightness or binding issue, bearings wear due to lack of lubrication, or clearance problems, now it might be as simple as the bearing shell was cocked in it seat, the main cap was not seated fully,that journal was out of round or over sized, the bearing was bent, or dirt under the shell but theres a reason the bearing wore in that way and the others didn,t, that needs to be looked into.
If the blocks been correctly line honed and the cranks strait Id be looking closely at the journals tapper,surface Finish, run-out and diam. to the central axis concentrically
ok, lets explain that a bit,the basic fact is that for bearings to wear at a different rate in the same engine theres obviously a difference in the clearances, or loads on those bearings surface, from one section to the other or oil flow or the conditions under, which they operate, in an ideal world a barrier film of high pressure oil prevents direct metal to metal contact, between the journals and bearings supporting them.
the journals on the crank, need to be exactly the same diameter from one end to the other and the center of the journal needs to be a consistent distance from the outer surface, it might help if you think of the journal as a beer can and the central axis as a string stretched thru the beer can strung thru two holes drilled in the exact center of each end, then think of what would happen if on one end the holes centered but on the other its a couple thousands off center, the off center end will track in a different rotational arc , , the effective stroke will be slightly longer or shorter or the rod will tend to bear far more load on one side than the other.
if the journal surface is slightly curved or barrel shaped or tapered or slightly hour glass shaped it causes, differences in the working clearances, effective oil flow rates, cooling and problems for the engine maintaining its supporting oil film at consistent pressures and the ability to keep the journal and bearing surfaces from contacting each other.
READ THIS THREAD
viewtopic.php?f=53&t=1168
these might also help
http://www.thirskauto.net/BearingPics.html
viewtopic.php?f=53&t=88&p=112#p112
http://www.bobistheoilguy.com/bearingwe ... alysis.htm
http://web.applied.com/site.cfm/Causeso ... ailure.cfm
you might want to read thru these threads as checking your filter will generally indicate bearing wear before you get other indications like lower oil pressure
viewtopic.php?f=54&t=938
viewtopic.php?f=53&t=204
viewtopic.php?f=54&t=615&hilit=+filter
viewtopic.php?f=54&t=150
viewtopic.php?f=54&t=117
Notes: You will still find some full-grooved main sets offered for older engines where demand is low and the engineering cost to bring the sets to current standards is not warranted (bearings generally represent the technology of the time the engine was developed).
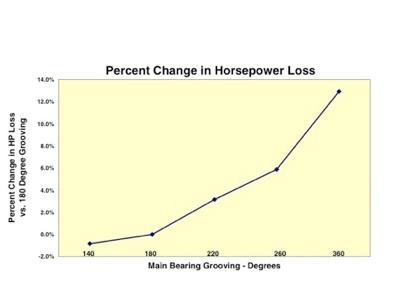
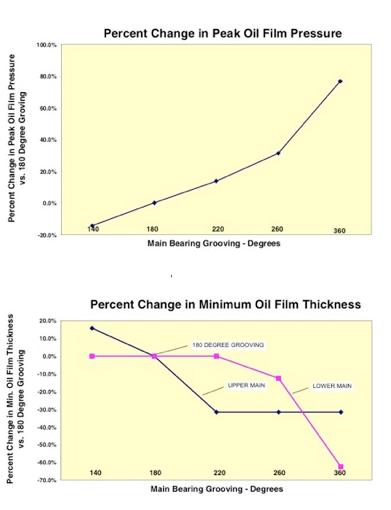
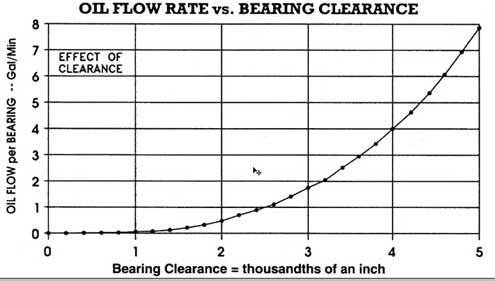
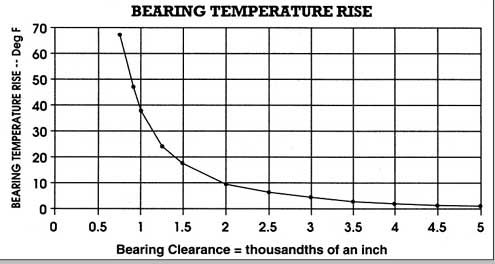
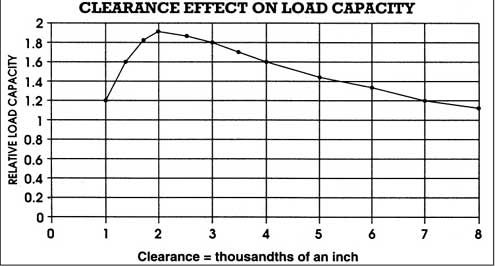
Manufacturers are frequently asked what difference grooving makes. Various forms of main bearing grooving have been used over the years.
It’s essential to understand that bearings depend on a film of oil to keep them separated from the shaft surface. This oil film is developed by shaft rotation. As the shaft rotates, it pulls oil into the loaded area of the bearing and rides up on this film much like a tire hydroplaning on wet pavement.
Grooving in a bearing acts like tread in a tire to break up the oil film. While you want your tires to grip the road, you don’t want your bearings to grip the shaft, so grooving is bad for maintaining an oil film. The primary reason for having any grooving in a main bearing is to provide oil to the connecting rods. Without rod bearings to feed, a simple oil hole would be sufficient to lubricate a main bearing.
Many early engines used full grooved bearings and some even used multiple grooves. Those choices were based on what engineers knew at the time. As engine and bearing technology developed, the negative effect of grooving was recognized and bearing grooving was removed from modern lower main bearings. The result is in a thicker film of oil for the shaft to ride on.
This provides a greater safety margin and improved bearing life. Upper main shells, which see lower loads than the lowers, and hence don’t apply the same load to the oil film, have retained a groove to supply the connecting rods with oil.
In an effort to develop the best possible main bearing designs for high performance engines, manufacturers have investigated the effects of main bearing grooving on bearing performance. The graphs (Figure 1) illustrate that a simple 180° groove in the upper main shell is still the best overall design.
While a slightly shorter groove of 140° provides a marginal gain, most of the benefit is to the upper shell, which doesn’t need improvement. On the other hand, extending the groove into the lower half, even as little as 20° at each parting line (220° in total), takes away from upper bearing performance without providing any benefit to the lower half. It’s also interesting to note that as groove length increases so does horsepower loss and peak oil film pressure, which is transmitted directly to the bearing.
Notes: You will still find some full-grooved main sets offered for older engines where demand is low and the engineering cost to bring the sets to current standards is not warranted (bearings generally represent the technology of the time the engine was developed).
Tech Tip courtesy of MAHLE Clevite Inc.