many guys even those with lifts prefer working under a car with a mechanics roller/creeper ,
http://www.hyjacks.com/H7.HTM
http://www.harborfreight.com/cpi/ctaf/displayitem.taf?Itemnumber=34924
http://www.zr1netregistry.com/jackupzr1.htm
up grade the casters
http://creepersweeper.com/
at some point its just not all that much cheaper to build things that are lower quality, those stands are fine!
Ive had six of the 12 ton jack stands in near constant use for MANY YEARS, trust me! I agree that much of what HF sells is crap, those stands are an exception, go look at them! they are stable, massive and decent designed stands, and yes it helps to have two floor jacks because at the low , first notch setting they are still fairly high from the floor, giving you plenty of access under a corvette or (Z)
http://www.creepex.com/indexEN.html
viewtopic.php?f=27&t=26
http://www.harborfreight.com/cpi/ctaf/d ... mber=66451
http://www.harborfreight.com/cpi/ctaf/d ... mber=93376
theres a hundred versions,they range from about 2 ton-60 ton ratings or more, theres several basic designs,a floor jacks generally prefered but at times clearance issures dictate thier use. ID suggest buying two of the 6-12 ton for any shop but use jack stands to support things once thier up in place
http://www.harborfreight.com/cpi/ctaf/d ... mber=91020
read
viewtopic.php?f=27&t=26
look closely at the FLIMSY JACK STANDS IN THIS PICTURE, Ive seen several of that jack stand design , suddenly fail and collapse
I would strongly advise pitching them in the dumpster if you own any
both the design and quality of manufacture matter its your choice but remember your going to be under the car ,no mater what you select, so be damn sure its sturdy with a healthy safety margin and a wide base,making them hard to tip,and be sure theres a good bit of metal in the design,several good designs , are available
I try to look for and buy American made products any time I can and don,t mind one bit paying an additional 10%-20%-even 30% more because I know from experience that theres frequently a good deal more quality components than in import clone parts, making the parts well worth the cost difference, there not much point in saving 30% on a part or tool that won,t do the job its designed to do, or one that can,t do its job safely!
but in a side by side comparison the import looked to be better made,
So I think your fighting a lost battle here,the last time I researched this, a decent 10-12 ton rated American made jack stand that has a wide base and can get a car frame 20'-24" off the floor safely, is well over 200$ EACH
Ive used 6 12 ton rated jack stands like these for almost 20 years now in my shop they are well made
http://www.homedepot.com/buy/tools-hard ... 70912.html
http://www.northerntool.com/shop/tools/ ... _200330725
(4 of the 12 ton rated HF jack stands, set at the height of the lower jack stand in the picture below set under a corvettes frame hold a corvette securely at the correct height for using a mechanics creeper )
http://www.harborfreight.com/12-ton-jac ... 34924.html
These super heavy duty jack stands will hold most cars and trucks safely over 2 feet off the ground. Perfect for repair work or storage.
Height: 19-1/2'' to 30-1/8''
Base: 12'' x 12-1/2''
Shipping Weight: 69.50 lbs.
theres NOTHING preventing you buying the HF design and drilling a few 5/8" holes to allow inserting a grade 8 bolt in those as a second safety either
http://www.harborfreight.com/12-ton-jac ... 34924.html
"1: why 12 ton? Ain't 6 ton more than enough?
2: how do you jack up the car? do you enroll your wife?
3: what floor jack do you use? Prices vary quite a bit?"
(1)
the 12 ton are BOTH FAR MORE STABLE from tipping or the car shifting, AND on the first notch they are exactly the correct height to allow comfortably accessing the under side of the car, place the 6 ton next to a 12 ton and raise both to the height of the 12 ton stands on the first notch, theres absolutely no comparison in your safety under the car, THERES ABSOLUTELY NO WAY YOU CAN COMPARE THE DEGREE OF STABILITY THE LARGER BASE AND STRONGER MATERIALS THE 12 TON STANDS PROVIDE
(2) your hardly the first guy to run into this, problem, you may need to fabricate or purchase floor jack spacer pads if your floor jack won,t raise the car high enough, I know I did, it was an easy process and I welded up my own, and both bolted and glued a 6: square section of old tire tread to the pads upper surface to prevent scaring the vettes car frame, so I could use the 12 ton jack stands, because my sears floor jacks could just barely reach the required height I fabricated spacers, with out the spacer pads, getting the 12 ton jack stands in place was more of a hassle,obviously this requires a bit of thinking in the procedure in getting the car up safely,to allow the taller jack height under the car frame,
on most floor jacks the lift pad is easily interchangeable , you can buy a replacement jack saddle
and weld a 2"-3" thick pad to the spares and drill and bolt and glue a section of old tire tread you find on any high way or from an old tire you can cut with a sawsall to make a second custom set of jack spacers if your floor jack won,t allow the car to be lifted high enough
one of my old geezer friends found 4 of these plates for $1 each at a yard sale and used a large center bolt, two washers and his shop welder to make a custom floor jack spacer pad for both his floor jacks, I thought that was rather ingenious s
OK first you DON,T raise a car one corner at a time! you drive it up on the inclined ramps to get clearance for the floor jack then slide the floor jack with the spacer if your floor jack requires one under the center of the front (CROSS MEMBER) and lift the front and place BOTH front 12 ton jack stands, under the frame , wide spaced, then the angle of the frame allows you to either use a second floor jack or move the front floor jack to the rear frame of the car, and lift the whole back or move both floor jacks to the rear frame on opposite sides and place both REAR 12 ton jack stands, on the rear frame. now personally I usually leave the rear jack stands and the jack holding the rear up ,and the 12 ton jack stands on the front with the tires hanging just above the inclined ramps, that way theres almost less chance the car can fall, even if some component were to fail.
Ill ALSO point out I have and have always used two floor jacks, twin rhino ramps and 4 12 ton jack stand WHEN I was under the corvette I use those 12 ton stand on when I use a mechanics creeper as I don,t want to be doing bench presses with a vette!:
a couple pictures here, of the finished project from several angles and in use, and a link to the jack and 5" solid rubber caster wheel you used from hf would be even more helpful, I can easily visualize what you did but from long experience helping others I know many guys won,t be able to easily grasp the concept even thought its dirt simple to you and I.
Here Ill try to help
I'm fairly sure hes referring too removing the wheel from the caster and fastening it horizontally as a spacer pad on the jack saddle to gain some additional height
http://www.harborfreight.com/5-in-rubber-heavy-duty-swivel-caster-61648.html
http://www.hyjacks.com/H7.HTM
http://www.harborfreight.com/cpi/ctaf/displayitem.taf?Itemnumber=34924
http://www.zr1netregistry.com/jackupzr1.htm
up grade the casters
http://creepersweeper.com/
at some point its just not all that much cheaper to build things that are lower quality, those stands are fine!
Ive had six of the 12 ton jack stands in near constant use for MANY YEARS, trust me! I agree that much of what HF sells is crap, those stands are an exception, go look at them! they are stable, massive and decent designed stands, and yes it helps to have two floor jacks because at the low , first notch setting they are still fairly high from the floor, giving you plenty of access under a corvette or (Z)
http://www.creepex.com/indexEN.html
viewtopic.php?f=27&t=26
http://www.harborfreight.com/cpi/ctaf/d ... mber=66451
http://www.harborfreight.com/cpi/ctaf/d ... mber=93376
theres a hundred versions,they range from about 2 ton-60 ton ratings or more, theres several basic designs,a floor jacks generally prefered but at times clearance issures dictate thier use. ID suggest buying two of the 6-12 ton for any shop but use jack stands to support things once thier up in place

http://www.harborfreight.com/cpi/ctaf/d ... mber=91020

read
viewtopic.php?f=27&t=26
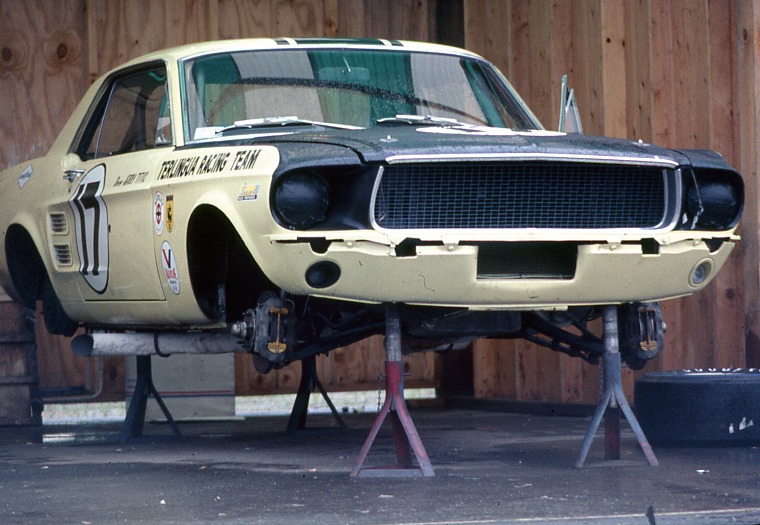
look closely at the FLIMSY JACK STANDS IN THIS PICTURE, Ive seen several of that jack stand design , suddenly fail and collapse
I would strongly advise pitching them in the dumpster if you own any
both the design and quality of manufacture matter its your choice but remember your going to be under the car ,no mater what you select, so be damn sure its sturdy with a healthy safety margin and a wide base,making them hard to tip,and be sure theres a good bit of metal in the design,several good designs , are available
I try to look for and buy American made products any time I can and don,t mind one bit paying an additional 10%-20%-even 30% more because I know from experience that theres frequently a good deal more quality components than in import clone parts, making the parts well worth the cost difference, there not much point in saving 30% on a part or tool that won,t do the job its designed to do, or one that can,t do its job safely!
but in a side by side comparison the import looked to be better made,
So I think your fighting a lost battle here,the last time I researched this, a decent 10-12 ton rated American made jack stand that has a wide base and can get a car frame 20'-24" off the floor safely, is well over 200$ EACH
Ive used 6 12 ton rated jack stands like these for almost 20 years now in my shop they are well made
http://www.homedepot.com/buy/tools-hard ... 70912.html
http://www.northerntool.com/shop/tools/ ... _200330725
(4 of the 12 ton rated HF jack stands, set at the height of the lower jack stand in the picture below set under a corvettes frame hold a corvette securely at the correct height for using a mechanics creeper )
http://www.harborfreight.com/12-ton-jac ... 34924.html
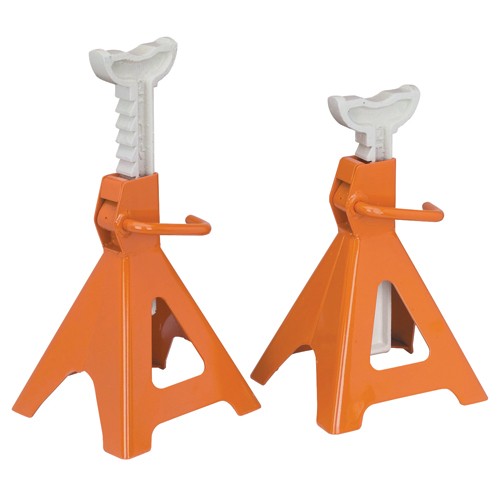
These super heavy duty jack stands will hold most cars and trucks safely over 2 feet off the ground. Perfect for repair work or storage.
Height: 19-1/2'' to 30-1/8''
Base: 12'' x 12-1/2''
Shipping Weight: 69.50 lbs.
theres NOTHING preventing you buying the HF design and drilling a few 5/8" holes to allow inserting a grade 8 bolt in those as a second safety either
http://www.harborfreight.com/12-ton-jac ... 34924.html
"1: why 12 ton? Ain't 6 ton more than enough?
2: how do you jack up the car? do you enroll your wife?
3: what floor jack do you use? Prices vary quite a bit?"
(1)
the 12 ton are BOTH FAR MORE STABLE from tipping or the car shifting, AND on the first notch they are exactly the correct height to allow comfortably accessing the under side of the car, place the 6 ton next to a 12 ton and raise both to the height of the 12 ton stands on the first notch, theres absolutely no comparison in your safety under the car, THERES ABSOLUTELY NO WAY YOU CAN COMPARE THE DEGREE OF STABILITY THE LARGER BASE AND STRONGER MATERIALS THE 12 TON STANDS PROVIDE
(2) your hardly the first guy to run into this, problem, you may need to fabricate or purchase floor jack spacer pads if your floor jack won,t raise the car high enough, I know I did, it was an easy process and I welded up my own, and both bolted and glued a 6: square section of old tire tread to the pads upper surface to prevent scaring the vettes car frame, so I could use the 12 ton jack stands, because my sears floor jacks could just barely reach the required height I fabricated spacers, with out the spacer pads, getting the 12 ton jack stands in place was more of a hassle,obviously this requires a bit of thinking in the procedure in getting the car up safely,to allow the taller jack height under the car frame,
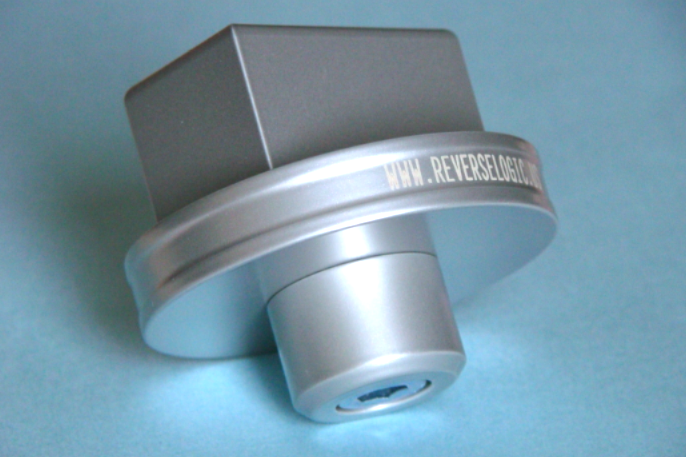
on most floor jacks the lift pad is easily interchangeable , you can buy a replacement jack saddle
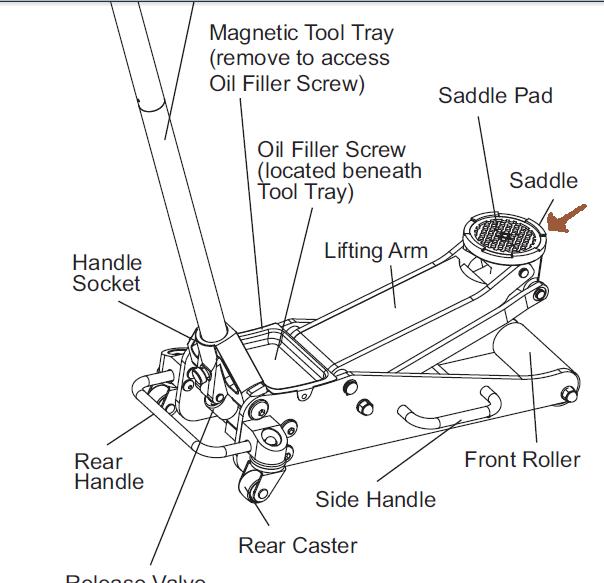
and weld a 2"-3" thick pad to the spares and drill and bolt and glue a section of old tire tread you find on any high way or from an old tire you can cut with a sawsall to make a second custom set of jack spacers if your floor jack won,t allow the car to be lifted high enough
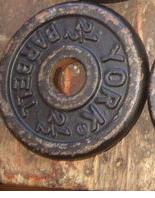
one of my old geezer friends found 4 of these plates for $1 each at a yard sale and used a large center bolt, two washers and his shop welder to make a custom floor jack spacer pad for both his floor jacks, I thought that was rather ingenious s
OK first you DON,T raise a car one corner at a time! you drive it up on the inclined ramps to get clearance for the floor jack then slide the floor jack with the spacer if your floor jack requires one under the center of the front (CROSS MEMBER) and lift the front and place BOTH front 12 ton jack stands, under the frame , wide spaced, then the angle of the frame allows you to either use a second floor jack or move the front floor jack to the rear frame of the car, and lift the whole back or move both floor jacks to the rear frame on opposite sides and place both REAR 12 ton jack stands, on the rear frame. now personally I usually leave the rear jack stands and the jack holding the rear up ,and the 12 ton jack stands on the front with the tires hanging just above the inclined ramps, that way theres almost less chance the car can fall, even if some component were to fail.
Ill ALSO point out I have and have always used two floor jacks, twin rhino ramps and 4 12 ton jack stand WHEN I was under the corvette I use those 12 ton stand on when I use a mechanics creeper as I don,t want to be doing bench presses with a vette!:
70CHEVELLE said:After installing my new rear suspension with sway bar, I realized my floor Jack would hit the sway bar before contacting the differential. Some guys I talked to say they just jack it on the sway bar, but I just couldn't do that. So I looked at Harbor Freight and bought a 2.5 ton aluminum low profile floor Jack. It looked like it may work right out of the box, but it didn't. It still hit the sway bar first. Better than my original jack but still no good. After looking around the local home improvement store, I ended up back at Harbor Frieght. I bought a 5" solid hard rubber caster wheel. Brought it home, removed the wheel, cut the small rubber "hub" off one side, and proceeded to mount it to the jack lift pad. I drilled and tapped two holes in the jack pad, drilled two holes in the rubber wheel, and sunk two allen head bolts into the wheel so they didn't protrude. The caster wheel is about 1 1/4" thick and now clears the sway bar by about a 1/4". I'm only using it to lift the car to then place jack stands under the frame when I need to do any work on it. I just thought I would share my modification.
a couple pictures here, of the finished project from several angles and in use, and a link to the jack and 5" solid rubber caster wheel you used from hf would be even more helpful, I can easily visualize what you did but from long experience helping others I know many guys won,t be able to easily grasp the concept even thought its dirt simple to you and I.
Here Ill try to help
I'm fairly sure hes referring too removing the wheel from the caster and fastening it horizontally as a spacer pad on the jack saddle to gain some additional height
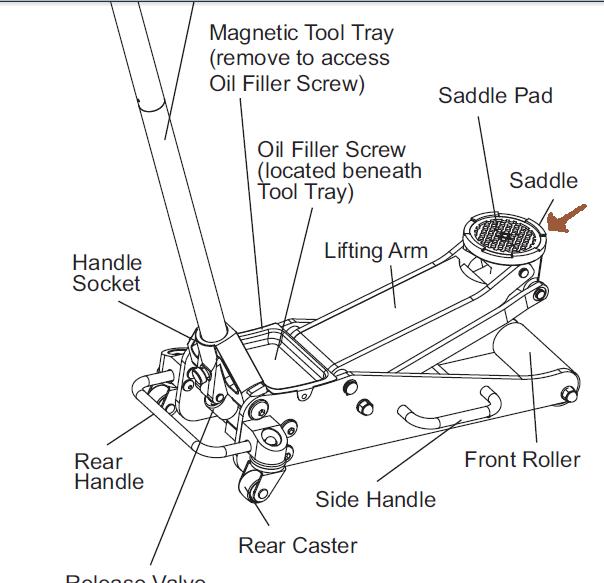
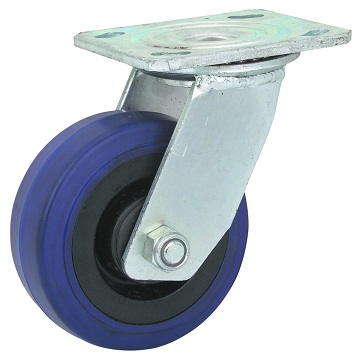
http://www.harborfreight.com/5-in-rubber-heavy-duty-swivel-caster-61648.html
Last edited by a moderator: