The stock ring filer just had too much end play in the shaft that holds the abrasive disk. So I stopped
by the local bearing supply and picked up a couple of bushings. If I wanted to wait it might have been
easier to buy a metric size bushing, but they weren't in stock so I bought the fractional size. The only
thing wrong is both the OD and ID were not correct. So I reamed the hole in the aluminum frame to accept
the larger OD of the bushing and turned the shaft on a lathe to fit the ID of the bushing.
I used JB weld to make the bushings permanent so I left it sticking out far enough to keep the shaft from moving to
the left and the locating pin would keep it from moving to the right. Since I turned the OD of the shaft down, I
had to drill and tap the 5mm x .8 metric threads, moving it closer to the centerline so it would intersect the
groove again.
There is NO end play now, much nicer !!!
Stock Ring Filer
The pin was moved closer to the centerline of the abrasive wheel shaft.
Finished Ring Filer
Edit on 11/09/2011
I wanted to see if theory and reality were close when it comes to the gap needed on the left stop pin of the ring filer to correct the angle filed on the ring end such that they would be parallel. I knew I couldn't do the math, but I could use Microsoft Visio and let it do the math for me.
I did the drawing to scale so that I could move the ring over until it's CENTER-LINE lined up with the right side of the grinding wheel while also touching the RIGHT stop pin, then measure the gap. I did this for two bore sizes so I could see how much difference the bore made. I used a 4" bore and a 4.5" bore for this test. The difference was only 0.005", hardly worth taking into consideration.
The LEFT STOP PIN needs to be 0.35" to 0.36" in diameter or you could replace it with a pin of 11/32"(0.35437") or 23/64"(.3593"). Dowel pins don't seem to come in those sizes, the only thing I've found so far is "Drill Rod" which would be hard to cut. Or you could do as Grumpy has suggested above and slip some copper tubing over the 1/4" stop pin that is already there.
You can purchase the drill rod for $5-7$ for a 3 foot length from Fastenall.
http://www.fastenal.com/web/search/prod ... evyx&Nty=0
http://www.fastenal.com/web/search/prod ... evyw&Nty=0
by the local bearing supply and picked up a couple of bushings. If I wanted to wait it might have been
easier to buy a metric size bushing, but they weren't in stock so I bought the fractional size. The only
thing wrong is both the OD and ID were not correct. So I reamed the hole in the aluminum frame to accept
the larger OD of the bushing and turned the shaft on a lathe to fit the ID of the bushing.
I used JB weld to make the bushings permanent so I left it sticking out far enough to keep the shaft from moving to
the left and the locating pin would keep it from moving to the right. Since I turned the OD of the shaft down, I
had to drill and tap the 5mm x .8 metric threads, moving it closer to the centerline so it would intersect the
groove again.
There is NO end play now, much nicer !!!
Stock Ring Filer

The pin was moved closer to the centerline of the abrasive wheel shaft.
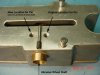

Finished Ring Filer
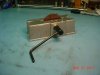
Edit on 11/09/2011
I wanted to see if theory and reality were close when it comes to the gap needed on the left stop pin of the ring filer to correct the angle filed on the ring end such that they would be parallel. I knew I couldn't do the math, but I could use Microsoft Visio and let it do the math for me.
I did the drawing to scale so that I could move the ring over until it's CENTER-LINE lined up with the right side of the grinding wheel while also touching the RIGHT stop pin, then measure the gap. I did this for two bore sizes so I could see how much difference the bore made. I used a 4" bore and a 4.5" bore for this test. The difference was only 0.005", hardly worth taking into consideration.
The LEFT STOP PIN needs to be 0.35" to 0.36" in diameter or you could replace it with a pin of 11/32"(0.35437") or 23/64"(.3593"). Dowel pins don't seem to come in those sizes, the only thing I've found so far is "Drill Rod" which would be hard to cut. Or you could do as Grumpy has suggested above and slip some copper tubing over the 1/4" stop pin that is already there.
You can purchase the drill rod for $5-7$ for a 3 foot length from Fastenall.
http://www.fastenal.com/web/search/prod ... evyx&Nty=0
http://www.fastenal.com/web/search/prod ... evyw&Nty=0
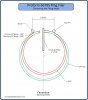
Last edited: