READ THE LINKED INFO, as it contains bits of useful pictures and hints you'll want
yes if you own a decent welder and a chop saw, and have a few fabrication skills,
you can surely build a better set of car ramps than you can buy in most cases
but there are options and these look like a decent deal, for a sports car like a corvette or an A.C. cobra clone
www.discountramps.com
http://zr1netregistry.com/jackupzr1.htm
http://zr1netregistry.com/Old_Proj/old_proj14.htm
http://www.corvettegadgetman.com/products3.html
http://www.eagleequip.com/page/EE/PROD/LI-LM/PAD-6000W
http://www.kwiklift.com/Options.htm
http://www.kwiklift.com/Options.htm#SIZE
http://garage.grumpysperformance.co...-diy-project-video-well-worth-watching.15647/
IVE used them, thier less expensive too buy and very easy too use but unless your doing mostly brake jobs and wheel and suspension related work and maybe oil changes their a P.I.T.A. or useless for many jobs and access under the car is very limited and unsafe in my opinion.
I still think the best value for most guys on a tight budget is purchasing's (4) 12 ton jack stands , decent ramps and two floor jacks, you can do 90% of the stuff you want to do on a car if you've got a decent flat concrete pad with those and have well under $600 invested and its easily transported when you move, I used them for many years before I got my lift and still use them frequently today
http://www.harborfreight.com/cpi/ctaf/displayitem.taf?function=Search
12 ton jack stands #34924
normally $80 for two, now on sale for $55 for two
"1: why 12 ton? Ain't 6 ton more than enough?
2: how do you jack up the car? do you enroll your wife?
3: what floor jack do you use? Prices vary quite a bit?"
(1)
the
12 ton are BOTH FAR MORE STABILE from tipping or the car shifting, AND on the first notch they are exactly the correct height to allow comfortably accessing the under side of the car, place the 6 ton next to a 12 ton and raise both to the height of the 12 ton stands on the first notch, theres absolutely no comparison in your safety under the car, THERES ABSOLUTELY NO WAY YOU CAN COMPARE THE DEGREE OF STABILITY THE LARGER BASE AND STRONGER MATERIALS THE 12 TON STANDS PROVIDE
(2)OK first you DON,T raise a vette one corner at a time! you drive it up on the ramps to get clearance for the jack then slide the floor jack under the center of the front (CROSS MEMBER) and lift the front and place BOTH front 12 ton jack stands, under the frame , wide spaced, then the angle allows you to either use a second floor jack or move the front floor jack to the rear of the vette, and lift the whole back and place both REAR 12 ton jack stands, on the rear frame. now personally I usually leave the rear jack stands and the jack holding the rear up ,and the 12 ton jack stands on the front with the tires hanging just above the ramps, that way theres almost no chance the vette can fall, even if some component were to fail.
Ill ALSO point out I have and have always used two floor jacks, twin rino ramps and 4 12 ton jack stand WHEN I was under the corvette as I don,t want to be doing bench presses with a vette!:WTF
(3)theres several deals available, and the quality varies wildly, youll need to shop, http://www2.northerntool.com/product/200345429.htm
this jack looks good in the info they posted, but if you can afford it ID buy two, so you can jack the frame with a buddies help with minimal frame twist.
I have two craftsman floor jacks and while they have worked well for years Id more than likely have purchased those if Id know about them at the time I bought them
http://www.corvettegadgetman.com/products3.html
http://garage.grumpysperformance.co...-diy-project-video-well-worth-watching.15647/
lots of guys think this is a good idea,personally Ive never needed or wanted one but then Ive installed a custom exhaust and in my case its not needed.
I HAVE thought seriously about BUYing or WELDING UP something like these
http://www.discountramps.com
http://www.discountramps.com/low_profile_car_ramp.htm
yes if you own a decent welder and a chop saw, and have a few fabrication skills,
you can surely build a better set of car ramps than you can buy in most cases
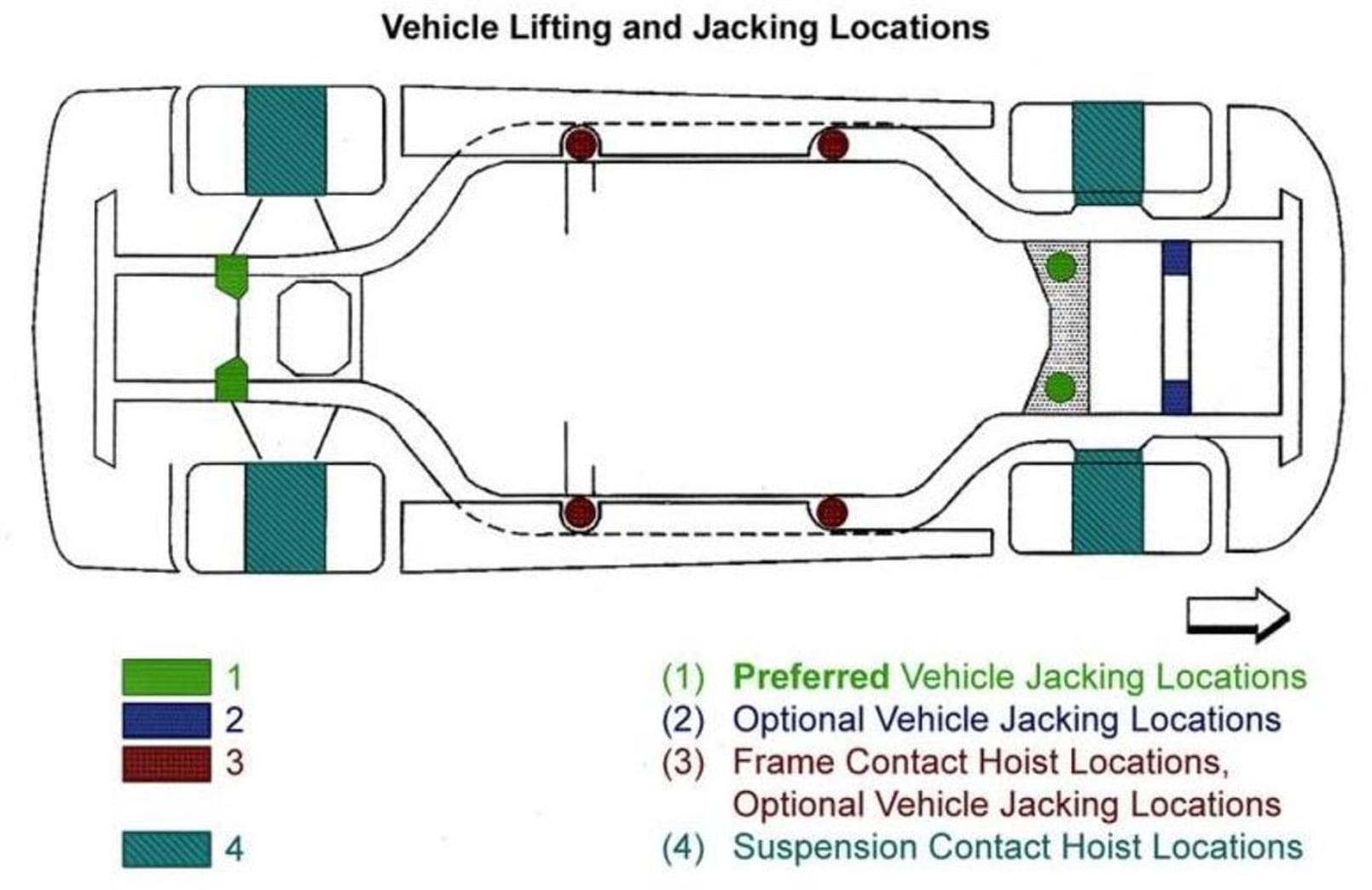
but there are options and these look like a decent deal, for a sports car like a corvette or an A.C. cobra clone
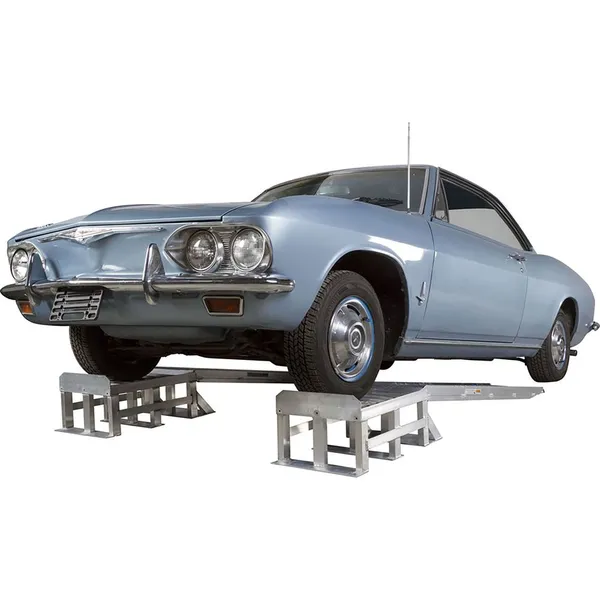
Extra-Long Aluminum 2-Piece Car Service Ramps - 3,000 lbs. per axle Capacity
These extra-long car repair ramps are great for servicing lowered cars and trucks. With a 9-1/2 in. rise and removable ramps, there's plenty of room to get under the vehicle.

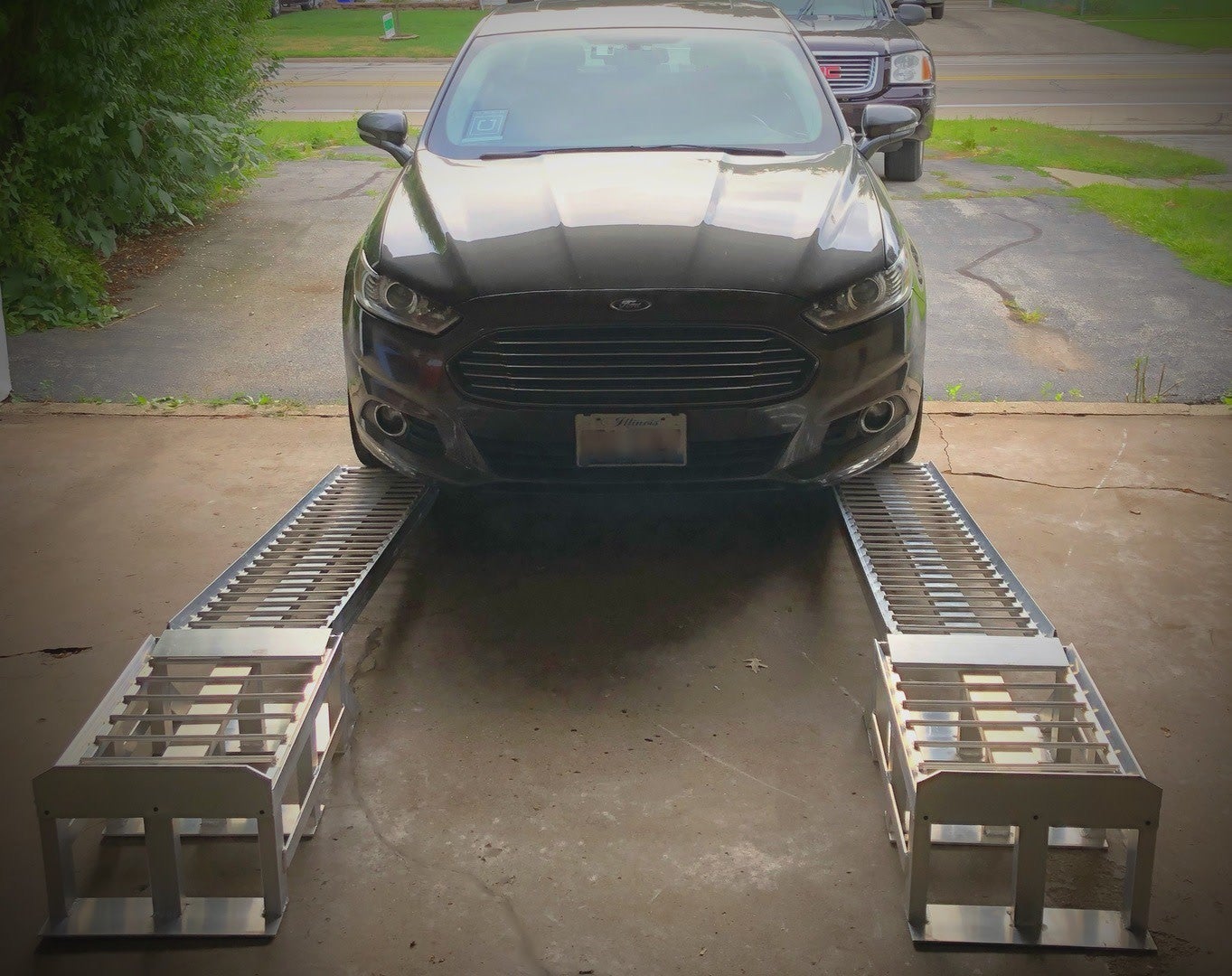
http://zr1netregistry.com/jackupzr1.htm
http://zr1netregistry.com/Old_Proj/old_proj14.htm
http://www.corvettegadgetman.com/products3.html
http://www.eagleequip.com/page/EE/PROD/LI-LM/PAD-6000W

http://www.kwiklift.com/Options.htm
http://www.kwiklift.com/Options.htm#SIZE
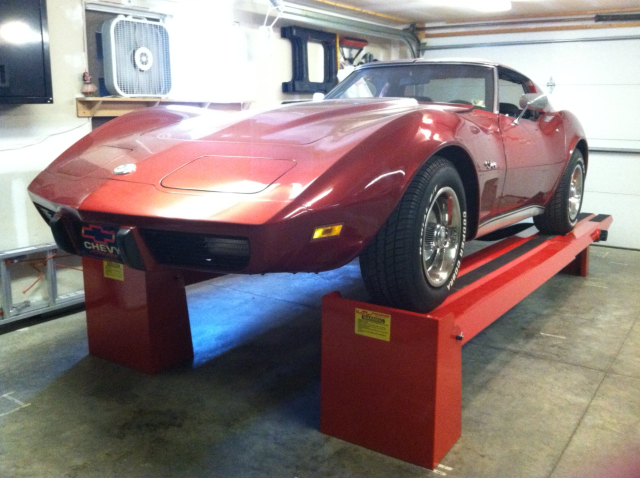
http://garage.grumpysperformance.co...-diy-project-video-well-worth-watching.15647/
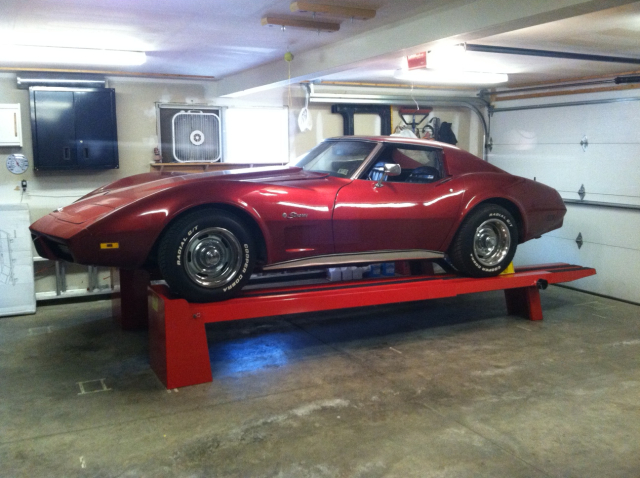
IVE used them, thier less expensive too buy and very easy too use but unless your doing mostly brake jobs and wheel and suspension related work and maybe oil changes their a P.I.T.A. or useless for many jobs and access under the car is very limited and unsafe in my opinion.
I still think the best value for most guys on a tight budget is purchasing's (4) 12 ton jack stands , decent ramps and two floor jacks, you can do 90% of the stuff you want to do on a car if you've got a decent flat concrete pad with those and have well under $600 invested and its easily transported when you move, I used them for many years before I got my lift and still use them frequently today
http://www.harborfreight.com/cpi/ctaf/displayitem.taf?function=Search

12 ton jack stands #34924
normally $80 for two, now on sale for $55 for two
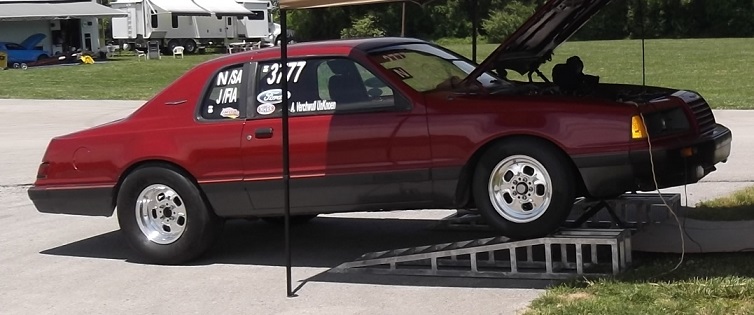

"1: why 12 ton? Ain't 6 ton more than enough?
2: how do you jack up the car? do you enroll your wife?
3: what floor jack do you use? Prices vary quite a bit?"
(1)
the
12 ton are BOTH FAR MORE STABILE from tipping or the car shifting, AND on the first notch they are exactly the correct height to allow comfortably accessing the under side of the car, place the 6 ton next to a 12 ton and raise both to the height of the 12 ton stands on the first notch, theres absolutely no comparison in your safety under the car, THERES ABSOLUTELY NO WAY YOU CAN COMPARE THE DEGREE OF STABILITY THE LARGER BASE AND STRONGER MATERIALS THE 12 TON STANDS PROVIDE
(2)OK first you DON,T raise a vette one corner at a time! you drive it up on the ramps to get clearance for the jack then slide the floor jack under the center of the front (CROSS MEMBER) and lift the front and place BOTH front 12 ton jack stands, under the frame , wide spaced, then the angle allows you to either use a second floor jack or move the front floor jack to the rear of the vette, and lift the whole back and place both REAR 12 ton jack stands, on the rear frame. now personally I usually leave the rear jack stands and the jack holding the rear up ,and the 12 ton jack stands on the front with the tires hanging just above the ramps, that way theres almost no chance the vette can fall, even if some component were to fail.
Ill ALSO point out I have and have always used two floor jacks, twin rino ramps and 4 12 ton jack stand WHEN I was under the corvette as I don,t want to be doing bench presses with a vette!:WTF
(3)theres several deals available, and the quality varies wildly, youll need to shop, http://www2.northerntool.com/product/200345429.htm
this jack looks good in the info they posted, but if you can afford it ID buy two, so you can jack the frame with a buddies help with minimal frame twist.
I have two craftsman floor jacks and while they have worked well for years Id more than likely have purchased those if Id know about them at the time I bought them
http://www.corvettegadgetman.com/products3.html
http://garage.grumpysperformance.co...-diy-project-video-well-worth-watching.15647/
lots of guys think this is a good idea,personally Ive never needed or wanted one but then Ive installed a custom exhaust and in my case its not needed.
I HAVE thought seriously about BUYing or WELDING UP something like these

http://www.discountramps.com

http://www.discountramps.com/low_profile_car_ramp.htm
Last edited by a moderator: