Grumpy, Here's one for you...
SBC 383 stroker using a Victor Jr. intake, Holley mechanical 750 double pumper, isky hydraulic roller cam and Dart 205 aluminum (Conquest) heads, along with 6 inch rods, forged wiesco pistons, at about a 10.5:1 compression ratio...
On the carb, what should I start with on the jetting, and also cams/squirters or other recommendations on running in the carb properly... This will be a track day road course car. Also running a carter helper pump from the fuel cell out to a surge canister, then onto a Mallory pump to a return style regulator with vaccum port.
Mike[/QUOTE]
I usually start at what ever point, (jets/power valves )the carb came with and let the plugs and a/f ratio and an IR temp gun on the headers tell me the necessary changes, if I had to guess Id start with 70 jets and 5.5 pvs front and rear, fuel pressure at 5 psi and set the floats to the bottom of the inspection ports and go from there!
read thru this stuff below while keeping in mind the basic goal is a 13.5-14.5:1 mid rpm cruise a/f ratio and about that same ratio at idle, with about 12.8:1-13.5:1 at wide open throttle, a vacuum gauge and a fuel pressure gauge,(I like to try for 5.0- 5.5 psi on the FP regulator) having your floats set correctly(just damp lower sight hole threads) and your ignition timing correct (all in at about 3200rpm at about 36-38 degrees total advance)and about 6-10 degrees BTDC at 900rpm idle)are mandatory
http://www.bob2000.com/carb.htm
http://www.mortec.com/carbtip1.htm
MORE USEFUL INFO
viewtopic.php?f=44&t=773
viewtopic.php?f=44&t=777
ID buy TWO of these
http://store.summitracing.com/partd...&N=700+4294861568+4294860208+115&autoview=sku
accellerator pump cams
http://store.summitracing.com/partdetai ... toview=sku
http://store.summitracing.com/partdetai ... toview=sku
http://store.summitracing.com/partdetai ... toview=sku
viewtopic.php?f=50&t=383&p=1637&hilit=infrared#p1637
viewtopic.php?f=81&t=1189&p=2447&hilit=sparkplug#p2447
LEARING TO READ PLUGS AND HAVING A INFRARED TEMP GUN, AND AN AIR/FUEL RATIO METER HELPS DURING TUNING
SBC 383 stroker using a Victor Jr. intake, Holley mechanical 750 double pumper, isky hydraulic roller cam and Dart 205 aluminum (Conquest) heads, along with 6 inch rods, forged wiesco pistons, at about a 10.5:1 compression ratio...
On the carb, what should I start with on the jetting, and also cams/squirters or other recommendations on running in the carb properly... This will be a track day road course car. Also running a carter helper pump from the fuel cell out to a surge canister, then onto a Mallory pump to a return style regulator with vaccum port.
Mike[/QUOTE]
I usually start at what ever point, (jets/power valves )the carb came with and let the plugs and a/f ratio and an IR temp gun on the headers tell me the necessary changes, if I had to guess Id start with 70 jets and 5.5 pvs front and rear, fuel pressure at 5 psi and set the floats to the bottom of the inspection ports and go from there!
read thru this stuff below while keeping in mind the basic goal is a 13.5-14.5:1 mid rpm cruise a/f ratio and about that same ratio at idle, with about 12.8:1-13.5:1 at wide open throttle, a vacuum gauge and a fuel pressure gauge,(I like to try for 5.0- 5.5 psi on the FP regulator) having your floats set correctly(just damp lower sight hole threads) and your ignition timing correct (all in at about 3200rpm at about 36-38 degrees total advance)and about 6-10 degrees BTDC at 900rpm idle)are mandatory
http://www.bob2000.com/carb.htm
http://www.mortec.com/carbtip1.htm
MORE USEFUL INFO
viewtopic.php?f=44&t=773
viewtopic.php?f=44&t=777
ID buy TWO of these
http://store.summitracing.com/partd...&N=700+4294861568+4294860208+115&autoview=sku
accellerator pump cams

http://store.summitracing.com/partdetai ... toview=sku
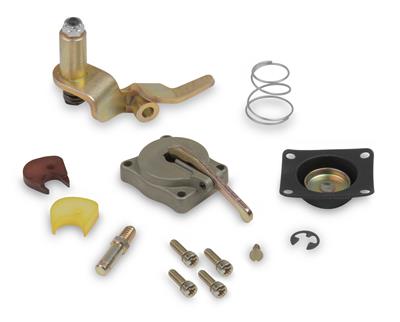
http://store.summitracing.com/partdetai ... toview=sku
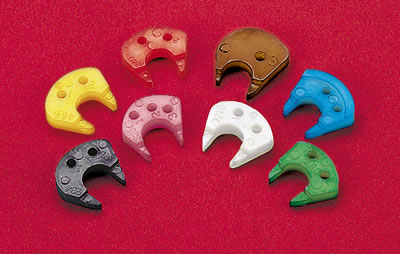
http://store.summitracing.com/partdetai ... toview=sku
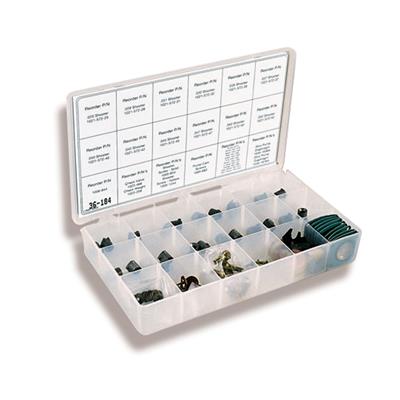
viewtopic.php?f=50&t=383&p=1637&hilit=infrared#p1637
viewtopic.php?f=81&t=1189&p=2447&hilit=sparkplug#p2447
LEARING TO READ PLUGS AND HAVING A INFRARED TEMP GUN, AND AN AIR/FUEL RATIO METER HELPS DURING TUNING