Yes, black clipped tiewraps give a neat appearance.
Long time gone between months of remodeling, travel and minor hand surgery. But hey it's a hobby right?
I've picked up again on that long awaited startup.
Finishing up rebuilding the Holley 850VS. That and the installation of flex supply lines to each bowl finishes the fuel system. Rather than a single fuel rail I prefer two individual lines from regulator to carb.
I've mentioned that in the past I had a forever problem with slow overheat or barely keeping cool, especially in summer. So I'm paying extra attention to all cooling factors.
I've already installed slightly different head gaskets based on Felpro tech advice and a higher volume water pump. Radiator is an aluminum crossflow 2 row with 1in tubes. Should be more efficient than a smaller tube 3 row, using 15lb cap, 160d thermostat and overflow container.
Here's something I noticed. I had always used a single belt, since no ac or PS. In the pic you can hopefully see that the belt only contacts about 25% of the WP pulley. It's a new pulley but same thing with old steel pulley. I think that partial slippage may have caused the WP to not run consistently, causing less circulation.
What I decided to do was add a second belt in the next set of grooves. Belt from BAL to WP only. This would ensure that there was no slippage but that belt would need a tensioner. General idea below.
I found a decent quality idler/tensioner Hayden 5950 to use. You can sort of see it here, sorry for dark background.
I'm making a support bracket for it, as it needs solid attachment to resist pull and twist. Using .25 thick steel.
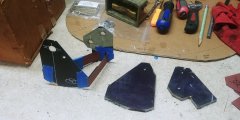
I'm not interested in a serpentine system because of cost, this v belt setup will work fine. I think that older vettes had something similar but it's expensive for just a basic pulley.
I'll be using twin Spal fans but for start up I'm installing a simple steel fan with thermo clutch. All the electrical is in place - this is just for convenience.
I'm also paying attention to the HEI advance curve as it can also impact tuning. Last time I graphed out a number of different curves, using the Dave Ray method of controlling the adjustable vac advance canister. Startup will be set to a basic curve then I'll tune it further along with carb adjustment/tuning as needed.