now most shops will rotate the cylinder to TDC and install an adapter for an air hose and pump a steady 100-130psi into the cylinder to hold the valves closed, but theres frequently clearance problems with headers and the adapters or hose and since you need to wack the valve retainer with a plastic hammer at times to get them free.......
yeah, IVE use air pressure frequently, BUT IVE NEVER TRUSTED air pressure ....and HATE paying rental fees.....if you don,t have the adapters or compressor,ETC. Ive usually prefered the old method of manually turning the cylinder to bottom dead center and removing the spark plug, then inserting about 10 feet of 3/8" cotton rope into the cylinder(TIE A KNOT in the end to prevent it from falling ALL the way in) then spin the engine MANUALLY (NOT WITH THE STARTER) to as close to TDC,as the crank will spin. this compresses the rope into a wad that supports the valve physically preventing its movement, down into the cylinder, once the valve springs replaced , you rotate the cylinder to BDC and remove the rope, proceed to the next cylinder
BTW I vastly prefer these
http://store.summitracing.com/partdetail.asp?part=PRO-66784&N=-114082+115&autoview=sku
www.summitracing.com
to these
http://store.summitracing.com/partdetail.asp?part=MAN-41830&N=-114082+115&autoview=sku
but if you use an air compressor youll NEED these
http://www.tavia.com/cat15.html
BTW if you go to change the valve springs with the heads still on the engine, most guys use the hose they use to do a compression check and the spark plug adapter and pump the cylinder up with about 125 psi of air to hold the valves shut while they do it, yeah it usually works just fine.
(yeah theres a differant method)
(1)disconnect the battery
(2) remove the spark plugs, and rocker arms
(3)turn the first cylinder to BDC BYE HAND or someplace close to that
(4) insert one end of 5 ft of 3/8" rope into the cylinder thru the sparkplug hole and be sure you tie a KNOT in the other end
(5) rotate BYE HAND,the engine until the rope compresses against the valves holding them in place
(6)REPLACE THE SPRINGS on that cylinder while the valves are held to the combustion chamber roof
(7)rotate the cylinder back to BDC
(8)pull out the rope
(repeat 7 more times)
:laughing:
yeah! the air USUALLY works but I don,t trust it EITHER, I want those valves locked from falling into the cylinder PHYSICALLY

BTW youll want one of these or something similar
http://store.summitracing.com/partdetail.asp?part=SUM-906784&autoview=sku
IVE done it both ways many times, Ive never trusted the air alone but Ive used it without problems in the past, the ropes usually not a problem,, and yeah theres the potential for it to tangle but I have not had that happen either
The first method involves using about 10’ piece of 3/16 nylon rope that you can get at the hardware store. Do not use binding twine or any type of rope that easily breaks apart. Simply remove all the spark plugs and, with the piston at its lowest point of its travel, insert at least 5-6 feet of rope into the cylinder through a spark plug hole:
Then slowly and gently hand-rotate the motor in the direction of normal travel until it won’t turn anymore. Give a slight tug on the rope and it should not want to easily pull out of the cylinder. Then you can install your valve spring compressor and confidently remove the keepers and springs. Once the work is done, turn the motor by hand in the reverse direction and you should have no problem pulling the rope out of the cylinder. This is a very cheap and effective solution.
The second method utilizes a compression tester hose and an air compressor. You only need the hose part and it normally will attach to your compressor air hose fitting. If you determine that your fittings will indeed match, you will need to take one additional step. You must remove the Schrader valve that is found on the “screw-in end†of the compression tester hose. Luckily the valve is the same type as is found in a tire valve stem so the same tool is used for removal:
if the heads are off the engine this style valve spring compressors far easier to use
www.summitracing.com
Now you are set. Remove a spark plug and bring that cylinder to TDC (top dead center.) In this method, I normally leave all other spark plugs in their appropriate cylinders until it is time to work with that particular cylinder. This helps to keep the whole motor from spinning over easily in the next step. Now screw the compressor fitting hose (and adapter, if required) into the spark plug hole and then connect the hose to your compressor air hose:
If you are lucky, the air pressure will not rotate the motor and the piston will remain at TDC. Irregardless, the air pressure will help keep the valves in the upright closed position. When the work is done and the valves are once again supported by their springs and valve locks, you can disconnect the air hose and relieve the air pressure found in the cylinder.
The air hose method can also be considered a poor man's leak-down tester. With the rockers backed off the valves and air pressure applied, listen for air rush at the car and at the exhaust. There should be no sound of air rushing from those 2 areas. A little leakage is normal from the crankcase, but the true amount lost can't determined without using a leak-down tester.
Proper push rod length is absolutely critical for peak performance—minimizing bent or broken valve stems, guide wear, and energy-wasting valve side-loading friction. IF YOU CHANGE VALVE TRAIN COMPONENTS VERIFY YOUR ROCKER GEOMETRY, AND ALL RELATED CLEARANCE ISSUES
With the lifter located on the round base circle, position the Push Rod length Checker (make sure you have the Checker with the proper diameter hole) over the stud. Ideally the Checker should contact the top of the push rod and the valve tip evenly at the same moment, should the Checker contact the push rod first, measure the gap between the front of the checker and the valve tip, and purchase a shorter push rod of the correct length. Should the Checker contact the valve tip first, measure the gap between the back of the Checker and the top of the push rod, and purchase a longer push rod
yeah, IVE use air pressure frequently, BUT IVE NEVER TRUSTED air pressure ....and HATE paying rental fees.....if you don,t have the adapters or compressor,ETC. Ive usually prefered the old method of manually turning the cylinder to bottom dead center and removing the spark plug, then inserting about 10 feet of 3/8" cotton rope into the cylinder(TIE A KNOT in the end to prevent it from falling ALL the way in) then spin the engine MANUALLY (NOT WITH THE STARTER) to as close to TDC,as the crank will spin. this compresses the rope into a wad that supports the valve physically preventing its movement, down into the cylinder, once the valve springs replaced , you rotate the cylinder to BDC and remove the rope, proceed to the next cylinder
BTW I vastly prefer these
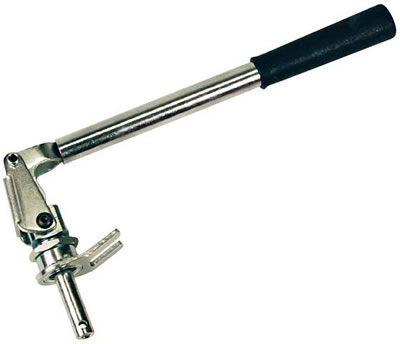
http://store.summitracing.com/partdetail.asp?part=PRO-66784&N=-114082+115&autoview=sku

OTC Tools 4573 OTC Large Valve Spring Compressors | Summit Racing
Free Shipping - OTC Large Valve Spring Compressors with qualifying orders of $109. Shop Valve Spring Compressors at Summit Racing.
to these
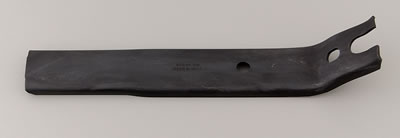
http://store.summitracing.com/partdetail.asp?part=MAN-41830&N=-114082+115&autoview=sku
but if you use an air compressor youll NEED these
http://www.tavia.com/cat15.html
BTW if you go to change the valve springs with the heads still on the engine, most guys use the hose they use to do a compression check and the spark plug adapter and pump the cylinder up with about 125 psi of air to hold the valves shut while they do it, yeah it usually works just fine.
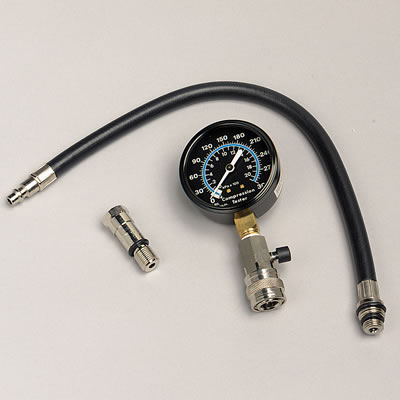
(yeah theres a differant method)
(1)disconnect the battery
(2) remove the spark plugs, and rocker arms
(3)turn the first cylinder to BDC BYE HAND or someplace close to that
(4) insert one end of 5 ft of 3/8" rope into the cylinder thru the sparkplug hole and be sure you tie a KNOT in the other end
(5) rotate BYE HAND,the engine until the rope compresses against the valves holding them in place
(6)REPLACE THE SPRINGS on that cylinder while the valves are held to the combustion chamber roof
(7)rotate the cylinder back to BDC
(8)pull out the rope
(repeat 7 more times)
yeah! the air USUALLY works but I don,t trust it EITHER, I want those valves locked from falling into the cylinder PHYSICALLY
BTW youll want one of these or something similar
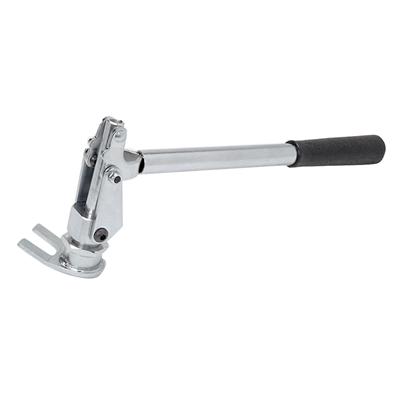
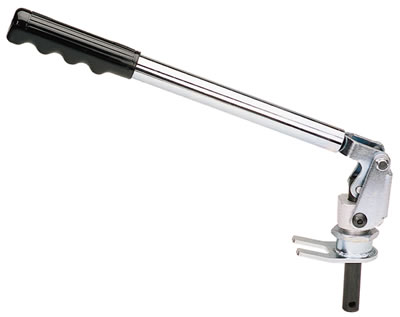
http://store.summitracing.com/partdetail.asp?part=SUM-906784&autoview=sku
IVE done it both ways many times, Ive never trusted the air alone but Ive used it without problems in the past, the ropes usually not a problem,, and yeah theres the potential for it to tangle but I have not had that happen either
The first method involves using about 10’ piece of 3/16 nylon rope that you can get at the hardware store. Do not use binding twine or any type of rope that easily breaks apart. Simply remove all the spark plugs and, with the piston at its lowest point of its travel, insert at least 5-6 feet of rope into the cylinder through a spark plug hole:
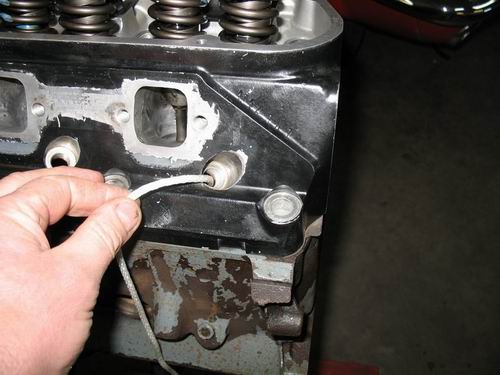
Then slowly and gently hand-rotate the motor in the direction of normal travel until it won’t turn anymore. Give a slight tug on the rope and it should not want to easily pull out of the cylinder. Then you can install your valve spring compressor and confidently remove the keepers and springs. Once the work is done, turn the motor by hand in the reverse direction and you should have no problem pulling the rope out of the cylinder. This is a very cheap and effective solution.
The second method utilizes a compression tester hose and an air compressor. You only need the hose part and it normally will attach to your compressor air hose fitting. If you determine that your fittings will indeed match, you will need to take one additional step. You must remove the Schrader valve that is found on the “screw-in end†of the compression tester hose. Luckily the valve is the same type as is found in a tire valve stem so the same tool is used for removal:
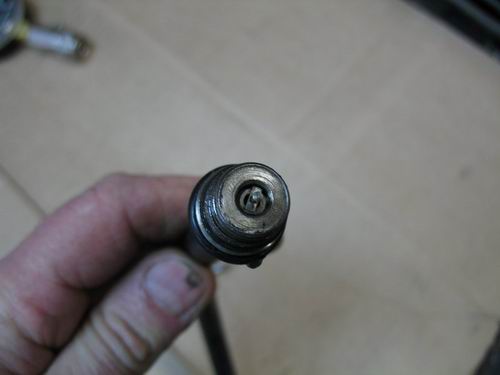
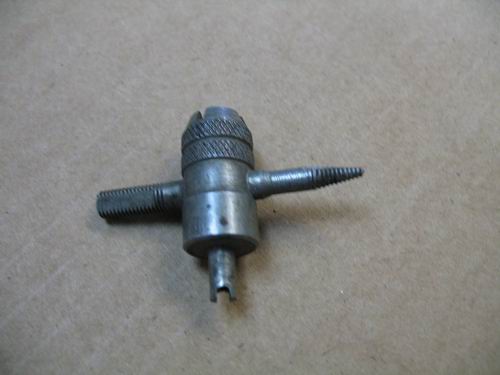
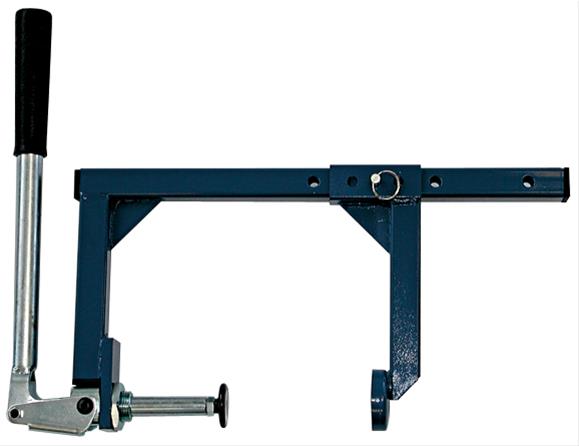
Proform Parts 66832 Proform Heavy-Duty Valve Spring Compressors | Summit Racing
Free Shipping - Proform Heavy-Duty Valve Spring Compressors with qualifying orders of $109. Shop Valve Spring Compressors at Summit Racing.
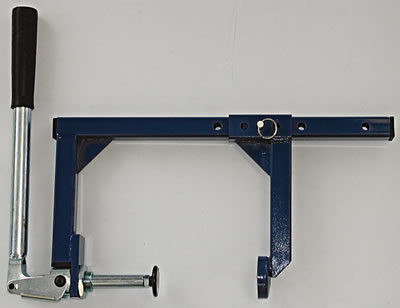
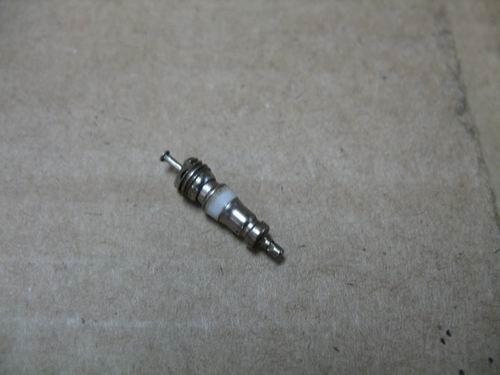
Now you are set. Remove a spark plug and bring that cylinder to TDC (top dead center.) In this method, I normally leave all other spark plugs in their appropriate cylinders until it is time to work with that particular cylinder. This helps to keep the whole motor from spinning over easily in the next step. Now screw the compressor fitting hose (and adapter, if required) into the spark plug hole and then connect the hose to your compressor air hose:
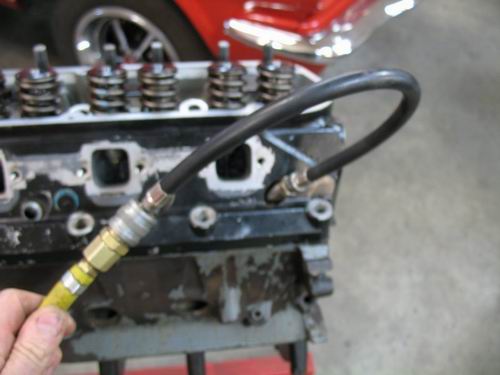
If you are lucky, the air pressure will not rotate the motor and the piston will remain at TDC. Irregardless, the air pressure will help keep the valves in the upright closed position. When the work is done and the valves are once again supported by their springs and valve locks, you can disconnect the air hose and relieve the air pressure found in the cylinder.
The air hose method can also be considered a poor man's leak-down tester. With the rockers backed off the valves and air pressure applied, listen for air rush at the car and at the exhaust. There should be no sound of air rushing from those 2 areas. A little leakage is normal from the crankcase, but the true amount lost can't determined without using a leak-down tester.
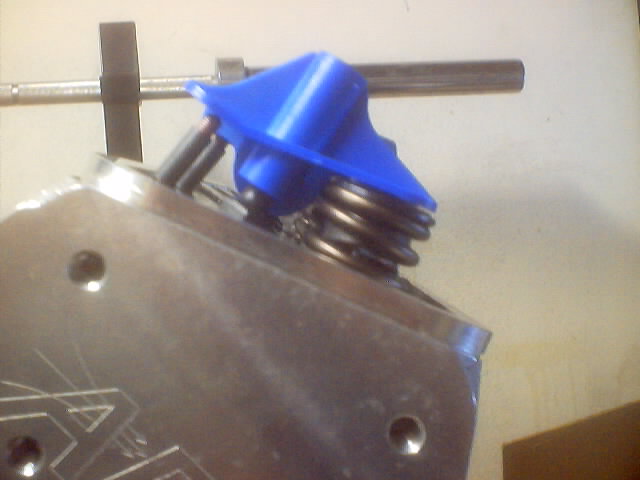
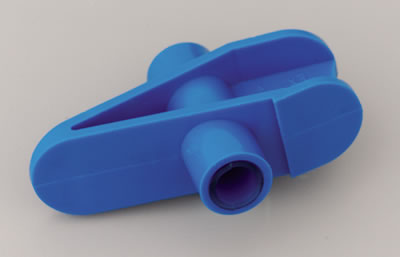
Proper push rod length is absolutely critical for peak performance—minimizing bent or broken valve stems, guide wear, and energy-wasting valve side-loading friction. IF YOU CHANGE VALVE TRAIN COMPONENTS VERIFY YOUR ROCKER GEOMETRY, AND ALL RELATED CLEARANCE ISSUES
With the lifter located on the round base circle, position the Push Rod length Checker (make sure you have the Checker with the proper diameter hole) over the stud. Ideally the Checker should contact the top of the push rod and the valve tip evenly at the same moment, should the Checker contact the push rod first, measure the gap between the front of the checker and the valve tip, and purchase a shorter push rod of the correct length. Should the Checker contact the valve tip first, measure the gap between the back of the Checker and the top of the push rod, and purchase a longer push rod
Last edited by a moderator: