let me try to explain quality in tig welders
heres the least expensive TIG Ive ever seen listed
http://www.harborfreight.com/cpi/ctaf/d ... mber=66787
imported dirt cheap, harbor freight welders,and similar low cost welder tend to give less than ideal results even in skilled hands
represented here
http://www.stockcarracing.com/techartic ... index.html
http://www.ehow.com/how_2266192_prepare ... lding.html
http://www.ehow.com/video_2327758_prepa ... lding.html
http://www.ehow.com/video_2327755_picki ... elder.html
http://www.ehow.com/video_2327756_setup-mig-welder.html
the higher quality welders from name brand suppliers tend to make even moderately skilled welders look good
miller, or lincoln,or HTP=
http://www.htpweld.com/
http://www.millerwelds.com/products/tig/
http://www.lincolnelectric.com/tig-welders.asp
viewtopic.php?f=60&t=72
viewtopic.php?f=60&t=1562
viewtopic.php?f=60&t=295
viewtopic.php?f=60&t=77
represented HERE!
heres the least expensive TIG Ive ever seen listed
http://www.harborfreight.com/cpi/ctaf/d ... mber=66787

imported dirt cheap, harbor freight welders,and similar low cost welder tend to give less than ideal results even in skilled hands
represented here

http://www.stockcarracing.com/techartic ... index.html
http://www.ehow.com/how_2266192_prepare ... lding.html
http://www.ehow.com/video_2327758_prepa ... lding.html
http://www.ehow.com/video_2327755_picki ... elder.html
http://www.ehow.com/video_2327756_setup-mig-welder.html
the higher quality welders from name brand suppliers tend to make even moderately skilled welders look good
miller, or lincoln,or HTP=
http://www.htpweld.com/
http://www.millerwelds.com/products/tig/
http://www.lincolnelectric.com/tig-welders.asp
viewtopic.php?f=60&t=72
viewtopic.php?f=60&t=1562
viewtopic.php?f=60&t=295
viewtopic.php?f=60&t=77
represented HERE!
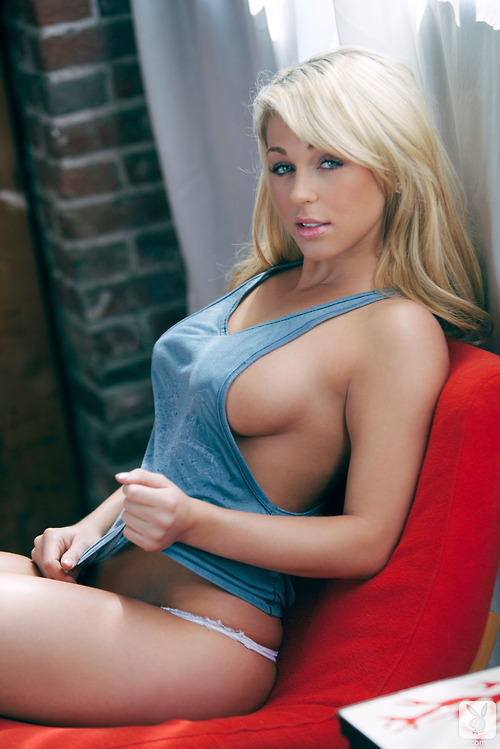