heres a darn impressive and logical custom welding project,
ONE MORE IN AN ENDLESS LIST OF GOOD REASONS TO OWN AND KNOW HOW TO USE A DECENT WELDER
I found posted on a different site and finding an older flex-plate or flywheel and a spare starter and gear for use with the engine stand as a gear drive and adding some custom crank handle, makes the stand more useable.
now I don,t know why I didn,t think of this, its a rather simple modification with easily obtainable components that would make using an engine stand easier.
the pictures, showing what needed to be done is rather self explanatory
YOU MIGHT WANT TO READ THRU THIS LINK
http://jniolon.classicpickup.com/enginestand/BDES.html
BTW most engine stand,s place an engine, fairly low so its not easy to tip over, but that also means you need to be bending over a good deal ,while working on the engine build-up. a mechanics seat that rolls easily , if its the correct height can be rather useful.
if you have a decent welder you might consider building a custom engine stand, or even engine crane, design. that makes mounting the engine easy.
HAVING A MILL AND LATHE, and DECENT MIG OR TIG WELDER MAKE A MILLION PROJECTS SO MUCH EASIER
IM SO JELOUS THAT I HAVE YET TO ACQUIRE A LATHE, AND WILL NEED TO REPLACE THE MILL I WAS FORCED TO SELL MOVING TO TEXAS
roseville carl
Did this a while back......
Material 1000 lb hand winch HF on sale 14.00, old chev timing chain and gears free, Alum stock 3.50 lb about 7 bucks worth, old cam slug free, and a days worth of my time, not worth much.......
first remove outer cable drum
drill out cam bearing to fit od of winch shaft and id of cam gear
Braise together
Cut inside and outside of coupling to match existing stand shaft
cam gear bolts to alum slug
Drill new pin hole and pin to shaft
assemble winch and gears and attach to stand with secure mounting points use at least 1/4" material
http://garage.grumpysperformance.com/index.php?threads/engine-leveler-and-swivel-hook.16160/
and wa la you have a cheap rotater for your engine stand
that will lock in either direction
<!-- / message --><!-- sig -->__________________
"Keep Em Between the Whites"........
ROSEVILLE CARL, SEP 12, 2012
Ive got two types of engine stands designs in my shop,(4 engine stands)but I added 4 of these wheels to each stand
http://www.northerntool.com/shop/tools/ ... _200442439
since the picture was taken,about 8 years ago, I added decent quality caster wheels to my engine stands in the shop, effectively doubling the cost of the stands but making them far FAR more user friendly, because they roll far easier, and you can lock the wheels when working on the engine making torquing the bolts far safer and easier, youll either weld the casters to the engine stand or use 8 squared u-bolts of the correct height and leg spacing to mount the casters.
www.zoro.com
http://www.harborfreight.com/8-inch-cus ... 46819.html
these are very similar to what I used (6) of on the engine crane, having 6 large diam. CASTERS rather than 4 small casters and two wheels that don,t change direction is a HUGE IMPROVEMENT in how easily the engine crane moves once an engines suspended from it
the guy in the videos, not very helpful or skilled at making videos,
but you might get a few tips watching anyway
the video below is a combo of engine stand and test stand
ONE MORE IN AN ENDLESS LIST OF GOOD REASONS TO OWN AND KNOW HOW TO USE A DECENT WELDER
I found posted on a different site and finding an older flex-plate or flywheel and a spare starter and gear for use with the engine stand as a gear drive and adding some custom crank handle, makes the stand more useable.
now I don,t know why I didn,t think of this, its a rather simple modification with easily obtainable components that would make using an engine stand easier.
the pictures, showing what needed to be done is rather self explanatory
YOU MIGHT WANT TO READ THRU THIS LINK
http://jniolon.classicpickup.com/enginestand/BDES.html
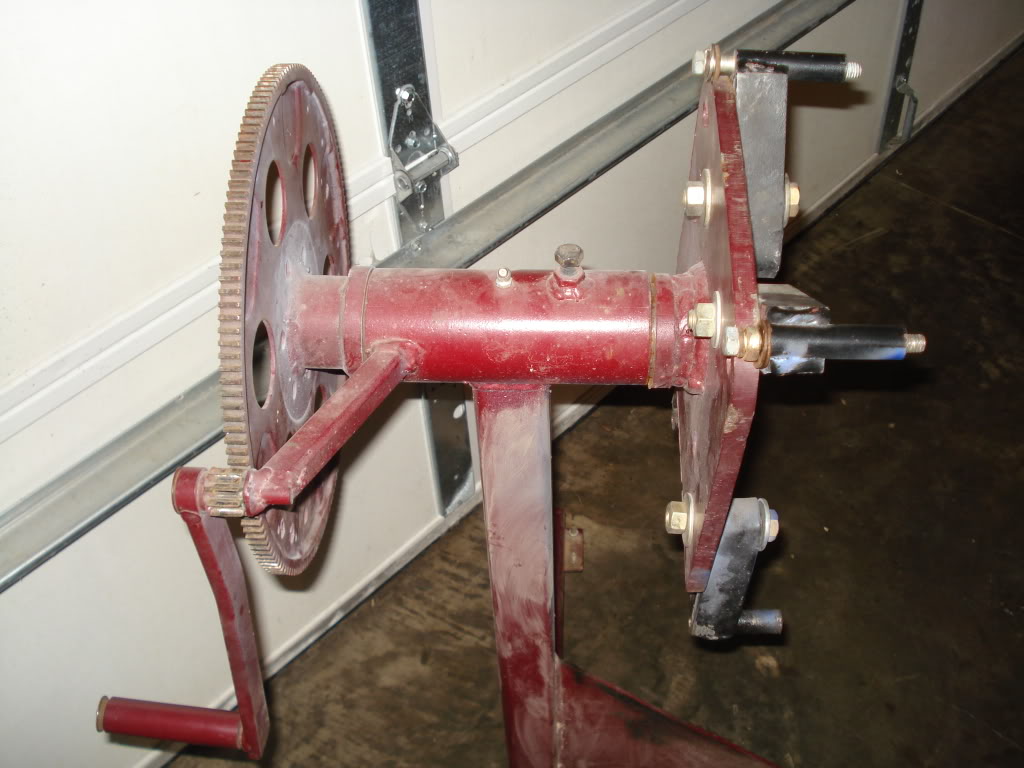
BTW most engine stand,s place an engine, fairly low so its not easy to tip over, but that also means you need to be bending over a good deal ,while working on the engine build-up. a mechanics seat that rolls easily , if its the correct height can be rather useful.
if you have a decent welder you might consider building a custom engine stand, or even engine crane, design. that makes mounting the engine easy.
HAVING A MILL AND LATHE, and DECENT MIG OR TIG WELDER MAKE A MILLION PROJECTS SO MUCH EASIER
IM SO JELOUS THAT I HAVE YET TO ACQUIRE A LATHE, AND WILL NEED TO REPLACE THE MILL I WAS FORCED TO SELL MOVING TO TEXAS
roseville carl
Did this a while back......
Material 1000 lb hand winch HF on sale 14.00, old chev timing chain and gears free, Alum stock 3.50 lb about 7 bucks worth, old cam slug free, and a days worth of my time, not worth much.......
first remove outer cable drum
drill out cam bearing to fit od of winch shaft and id of cam gear
Braise together
Cut inside and outside of coupling to match existing stand shaft
cam gear bolts to alum slug
Drill new pin hole and pin to shaft
assemble winch and gears and attach to stand with secure mounting points use at least 1/4" material
http://garage.grumpysperformance.com/index.php?threads/engine-leveler-and-swivel-hook.16160/
and wa la you have a cheap rotater for your engine stand
that will lock in either direction
<!-- / message --><!-- sig -->__________________
"Keep Em Between the Whites"........
ROSEVILLE CARL, SEP 12, 2012
Ive got two types of engine stands designs in my shop,(4 engine stands)but I added 4 of these wheels to each stand
http://www.northerntool.com/shop/tools/ ... _200442439
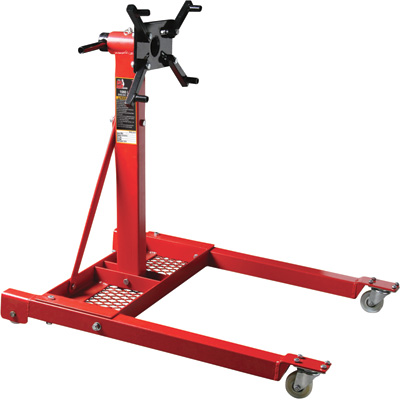
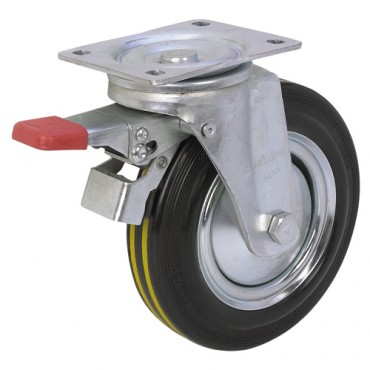
since the picture was taken,about 8 years ago, I added decent quality caster wheels to my engine stands in the shop, effectively doubling the cost of the stands but making them far FAR more user friendly, because they roll far easier, and you can lock the wheels when working on the engine making torquing the bolts far safer and easier, youll either weld the casters to the engine stand or use 8 squared u-bolts of the correct height and leg spacing to mount the casters.
Hampton Square U-Bolt, 3/8", 4 in Inside Ht, 3 in Inside Wd/Dia, Steel 02-3452-504 | Zoro
Order Hampton Square U-Bolt, 3/8", 4 in Inside Ht, 3 in Inside Wd/Dia, Steel, 02-3452-504 at Zoro.com. Great prices & free shipping on orders over $50 when you sign in or sign up for an account.


http://www.harborfreight.com/8-inch-cus ... 46819.html
these are very similar to what I used (6) of on the engine crane, having 6 large diam. CASTERS rather than 4 small casters and two wheels that don,t change direction is a HUGE IMPROVEMENT in how easily the engine crane moves once an engines suspended from it
the guy in the videos, not very helpful or skilled at making videos,
but you might get a few tips watching anyway
Last edited by a moderator: