Note - a lot of my pics may not be that important as build info, but just like my 454 build, they are part of my documentation and are a great benefit if and when I need to refresh my memory or to verify what the heck I did.
Besides a couple of different sets of bearing/bushing drivers, a lot of hand tools, measuring tools, etc. I also have some homemade tools that have worked pretty well. These include a piston retainer compressor tool, bushing remover tool, accumulator compressor and an assortment of round things on a threaded rod that are used to install (and remove) bushings from more difficult to reach units. I don't like to beat bushings into place so wherever possible I try to use some sort of threaded installer to ease them into place. Similar to a harmonic balancer installer tool concept. I also have a 20T shop press that I use for parts whenever I can, such as with the piston retainer compressor, bushings, seals etc.
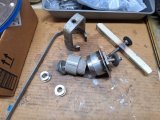
I finished up the tailshaft housing with the rear seal. The bushing and the seal were installed using my shop press. I know the red stuff on seals is intended to help avoid seepage, my preference is to add a thin smear of Permatex #2. Never have had a problem. The obvious M10 lettering is to remind me NOT to try to thread in 3/8" SAE bolts from the rear mount.
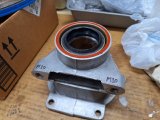
Shifter shaft seal (say that 3 times fast) installed into the case, also with a thin wipe of Permatex. All seals get a light coating of blue transmission assembly lube.
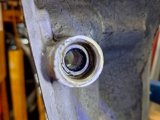
Pump tolerances have been checked, next was to give the pump body exterior side a coat of paint, just for corrosion resistance. That's the extent of the paintwork on the unit - it's buried up under the car and doesn't need a paintjob. But it is clean. Pic below is just before I gave it a light coat of primer.
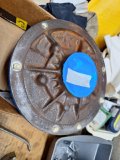
Pump bushing was replaced - I'm not sure what that dark stuff is, the bushing was clean when I installed it.
Very important! Picture below is from the front side of the pump - bushing is at same level as the bore surface. It could even be slightly proud of the surface on this side, because the gear side of the bushing MUST be below the gearset.
Front side - placement not that critical.
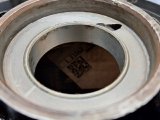
Gear side - placement is critical. Bushing must be below surface where gearsets rotate. You'll notice a few rub marks on the bushing - that's not a big deal, it's from fitting the pump body onto the converter hub to ensure there's no binding. It rotates nicely on the hub, and the marks are from the initial "set" onto the hub. There's a light coating of blue lube on the surface of installed bushings too.
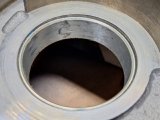
Pump body finished, seal installed. Same deal with the light smear of Permatex on the seal frame.
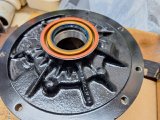
I'm waiting on some Sonnax parts for the pump pressure regulator.
After that, the pump is ready to align its two halves together - I'll use the case itself to do this.
Besides a couple of different sets of bearing/bushing drivers, a lot of hand tools, measuring tools, etc. I also have some homemade tools that have worked pretty well. These include a piston retainer compressor tool, bushing remover tool, accumulator compressor and an assortment of round things on a threaded rod that are used to install (and remove) bushings from more difficult to reach units. I don't like to beat bushings into place so wherever possible I try to use some sort of threaded installer to ease them into place. Similar to a harmonic balancer installer tool concept. I also have a 20T shop press that I use for parts whenever I can, such as with the piston retainer compressor, bushings, seals etc.
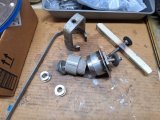
I finished up the tailshaft housing with the rear seal. The bushing and the seal were installed using my shop press. I know the red stuff on seals is intended to help avoid seepage, my preference is to add a thin smear of Permatex #2. Never have had a problem. The obvious M10 lettering is to remind me NOT to try to thread in 3/8" SAE bolts from the rear mount.
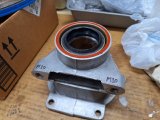
Shifter shaft seal (say that 3 times fast) installed into the case, also with a thin wipe of Permatex. All seals get a light coating of blue transmission assembly lube.
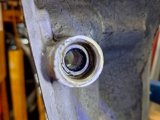
Pump tolerances have been checked, next was to give the pump body exterior side a coat of paint, just for corrosion resistance. That's the extent of the paintwork on the unit - it's buried up under the car and doesn't need a paintjob. But it is clean. Pic below is just before I gave it a light coat of primer.
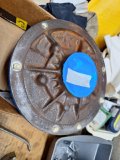
Pump bushing was replaced - I'm not sure what that dark stuff is, the bushing was clean when I installed it.
Very important! Picture below is from the front side of the pump - bushing is at same level as the bore surface. It could even be slightly proud of the surface on this side, because the gear side of the bushing MUST be below the gearset.
Front side - placement not that critical.
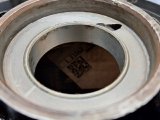
Gear side - placement is critical. Bushing must be below surface where gearsets rotate. You'll notice a few rub marks on the bushing - that's not a big deal, it's from fitting the pump body onto the converter hub to ensure there's no binding. It rotates nicely on the hub, and the marks are from the initial "set" onto the hub. There's a light coating of blue lube on the surface of installed bushings too.
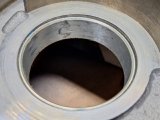
Pump body finished, seal installed. Same deal with the light smear of Permatex on the seal frame.
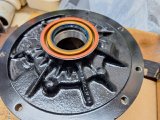
I'm waiting on some Sonnax parts for the pump pressure regulator.
After that, the pump is ready to align its two halves together - I'll use the case itself to do this.