Before I add more progress I wanted to note some of my project organization methodology - I'm sure Rick is way ahead on this - but regardless, anything you do to keep track of things, specs, measurements, pictures, etc, yields much better end results.
All my car projects and "sub-projects" like the 454 and this transmission get a bag and tag at disassembly, along with pictures and notes pertaining to that part of disassembly.
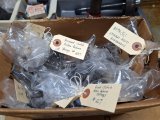
I also keep a binder on any project I do. I think it's especially important for specs and measurements, like on my engine build. But I also use it for parts listing, receipts, general info, etc. - and I use it all the time. Example is that I will list what parts are being ordered, from where/cost, then I'll check them off as they arrive and put the receipt into the binder.
I also keep a general work log as I go. Example for today: "coolant fill, change PCV valve, work on transmission". Nothing complicated but it's a good progress chart (I'm on page 13 of this entire car build lol).
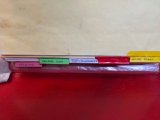
Grumpy always talks about HAVING A GAME PLAN! So true, and I do this initially so I can figure out where I'm heading, IMO especialy important on long-term complicated projects. But basically there's nothing that special about what I'm doing, it just really helps my old brain to clarify, document, and remember things.
All my car projects and "sub-projects" like the 454 and this transmission get a bag and tag at disassembly, along with pictures and notes pertaining to that part of disassembly.
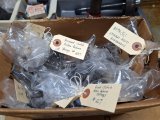
I also keep a binder on any project I do. I think it's especially important for specs and measurements, like on my engine build. But I also use it for parts listing, receipts, general info, etc. - and I use it all the time. Example is that I will list what parts are being ordered, from where/cost, then I'll check them off as they arrive and put the receipt into the binder.
I also keep a general work log as I go. Example for today: "coolant fill, change PCV valve, work on transmission". Nothing complicated but it's a good progress chart (I'm on page 13 of this entire car build lol).
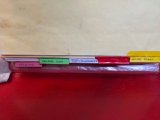
Grumpy always talks about HAVING A GAME PLAN! So true, and I do this initially so I can figure out where I'm heading, IMO especialy important on long-term complicated projects. But basically there's nothing that special about what I'm doing, it just really helps my old brain to clarify, document, and remember things.