Rear Gearset ....
I'm now starting to get into the pre-assembly to check clearances.
First up will be the rear gearset.
This is a great instructional video from Nick's Transmissions
Starting off really simple! I need to have a base to assemble the gearset - I'm using a cleaned out pool chemical bucket.
It's got a reinforced top that should hold the weight of the assembly.

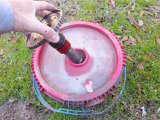
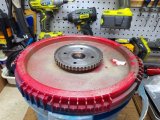
There's three Torrington bearing assemblies that I'll be using (all part of a Sonnax bearing kit). They are all slightly different, and I'm taking great pains to not mix them up. But, as a "just in case" I've done way overkill by engraving the ATSG part number on the races of each assembly. It's extremely light, won't mess up anything. I'm probably the only guy in the world that would do this.
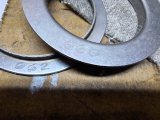
I'm now starting to get into the pre-assembly to check clearances.
First up will be the rear gearset.
This is a great instructional video from Nick's Transmissions
Starting off really simple! I need to have a base to assemble the gearset - I'm using a cleaned out pool chemical bucket.
It's got a reinforced top that should hold the weight of the assembly.

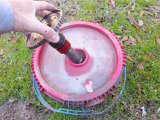
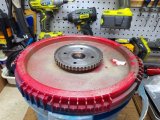
There's three Torrington bearing assemblies that I'll be using (all part of a Sonnax bearing kit). They are all slightly different, and I'm taking great pains to not mix them up. But, as a "just in case" I've done way overkill by engraving the ATSG part number on the races of each assembly. It's extremely light, won't mess up anything. I'm probably the only guy in the world that would do this.
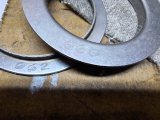
Last edited: