The lower control arm mounting points holes in the 1st and 2nd gen frames are often worn or damaged. The design really isn't very good IMO. Forces from cornering, bumping parking blocks, hitting potholes, etc. is transferred to the frame through the LCA bolts to the edges of the holes in the sheet metal the frame is stamped out of. Thats not much surface area and making it worse the bolts are shouldered on one side but the other side of each bolt just has the tips of the threads hitting the frame. Since the bolts are hardened steel they deform the holes in the softer metal of the frame ovalizing them. I see it a lot on 2nd gens and since the 1st gens did the same thing I'm surprised the engineers at GM didn't come up with something better for 2nd gens.
Now some of us put stiffer springs, tubular control arms, solid bushings, wider modern sticky tires, and big fat sway bars on the car and then take the car out for spirited driving, auto-X, and even road track use. The force on the thin sheet metal bolt holes in the frame far exceeds what the engineers had in mind. Heck, radial tires weren't even standard on most American cars yet when the suspension was originally designed.
If the LCA mounting holes are ovalized (or you want to reinforce them) a piece of thick steel with a hole drilled in it or a thick washer(s) can be welded to the frame. Welding something to the frame should also reduce flexing theoretically allowing our cool new suspension & tires to perform their best. When possible, I like to use a long piece of all thread rod with nuts through the frame to line up the holes of the washers or metal being welded and hold them tight to the frame to tack weld in place. Then remove the rod and fully weld. If a rod won't slide through all 4 holes on one side because of crossmember interference I'll bolt the control arm in place with the pieces to be welded, tack in place, remove arm and then fully weld.
On the frame I'm currently preparing (81 subframe into a 70) I wanted to strengthen the frame, reduce flex, and reduce wear as much as possible within my budget. To complicate things I want to use my old control arms with the 1/2" bolts in a frame made for the larger diameter metric bolts.
Here's the 2 different bolts I'm aware of, Metric 81 on the left and 1/2" on the right. In the next pic note the shoulder where the frame sits on one side while the other side is on the bolt threads. Really GM? Couldn't think of a better way after seeing it didn't work well for the 1st gens?
So here's my plan for the current project where the LCA attaches. This will reduce the holes to 1/2", stiffen the area, and hopefully prevent ovalizing.
1. 1/2" ID 2 1/2" OD body washers 1/8" thick to stiffen the frame. Some are cut and bent to fit and welded into place.
2. 1/2" grade 8 bolts with a shank section about 3 3/8". The long shank section will keep the threaded part from transferring the shear forces to the edge of the frame sheet metal. New tapered thread locknuts will be used for final assembly, regular nuts for mock up etc. are seen in the pics below. Keep in mind kids those factory tapered thread locknuts are considered single use fasteners and should be replaced if removed.
3. 1/2" grade 8 washers welded to each other and welded to the big washers will take the forces that originally went to the edge of the frame sheet metal. This will spread out the force because the combined thickness of the washers is greater than the frame sheet metal. Also, because of the longer shank section both sides will have full contact rather than one side putting the force on the thread tips. With the large washers and 3 of the grade 8's on each side the nuts won't bottom on the shank when tightened. Grade 8 washers are being used because they are made to closer tolerances than cheap washers and fit the bolt shank tighter. I'm aware they'll lose their heat treating when welded.
Since I'm switching from the metric size frame holes to the smaller 1/2" holes there's a slight movement before everything is welded. I'll pull the LCA So any slight change in position will give me a little extra positive castor. I'll do some more weld grinding and polishing before sandblasting so the frame is pretty for body color paint. Next post is upper control arm/shock mount modification.
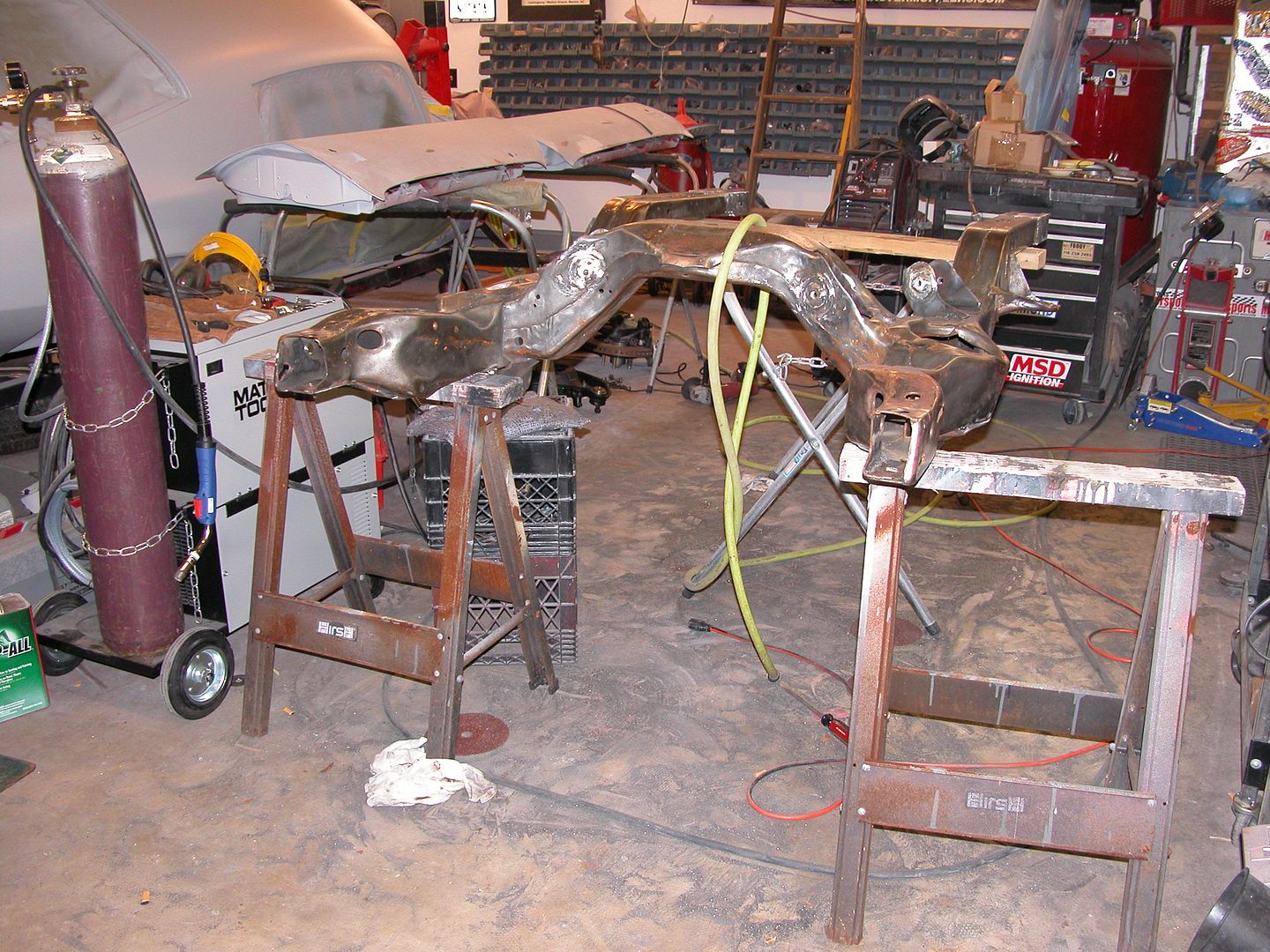