I'll probably just buy a length checker even though I've made a number of my shop tools, like my press and benders, along with a ton of smaller stuff. Sometimes though I'll just get lazy and buy it lol.
I'm really glad you posted that particular link section. There's a number of things I've been thinking about, including use of magnets and screens. I've always had a magnet on oil filters but I was looking at Grumpy's info on higher heat resistant magnets and valley screens. The pic he posted was good, I think it showed the right size mesh size. If you were to use a very dense screen you'd be creating a problem with oil collecting in the valley.
Thanks, I'll go through that section again.
Oh, here's the recipient of that happy horsepower with my grandson/helper....
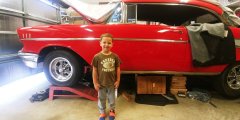
I'm really glad you posted that particular link section. There's a number of things I've been thinking about, including use of magnets and screens. I've always had a magnet on oil filters but I was looking at Grumpy's info on higher heat resistant magnets and valley screens. The pic he posted was good, I think it showed the right size mesh size. If you were to use a very dense screen you'd be creating a problem with oil collecting in the valley.
Thanks, I'll go through that section again.
Oh, here's the recipient of that happy horsepower with my grandson/helper....
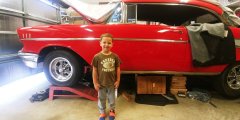