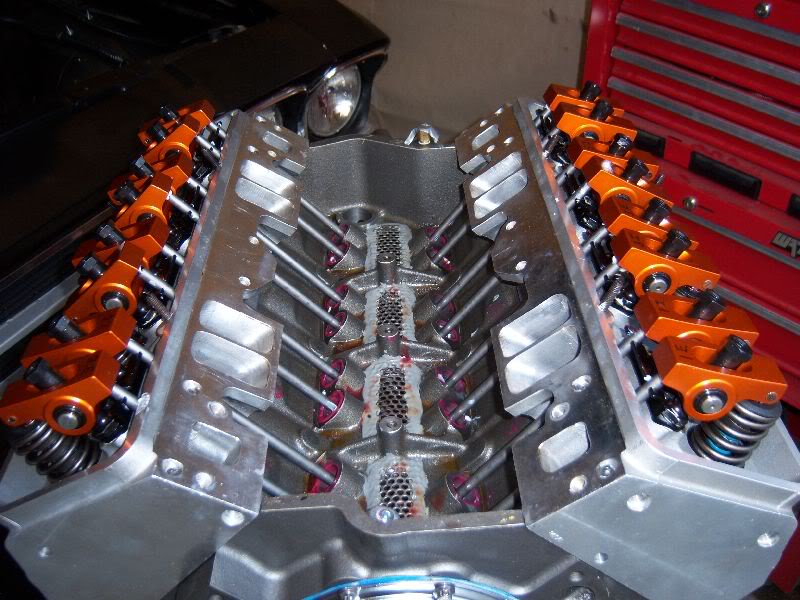
you can cut 4 individual shrapnel screens like the picture above and epoxy them in place or on some blocks a lifter gallery long single shrapnel screen can be fabricated
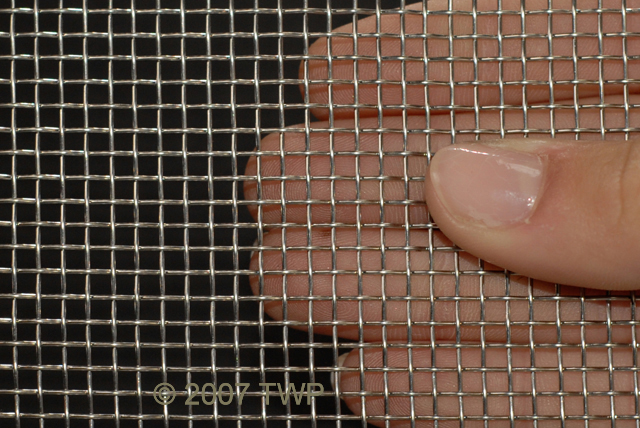
while I generally use stainless 6 or 8 mesh screens theres lots of options that will work just fine, just remember to keep the oil changed regularly or theres some potential for sludge to clog ANY size shrapnel screens
http://www.twpinc.com/twpinc/products/T ... 6T0350W36T
http://www.twpinc.com/twpinc/products/T ... 8S0280W36T
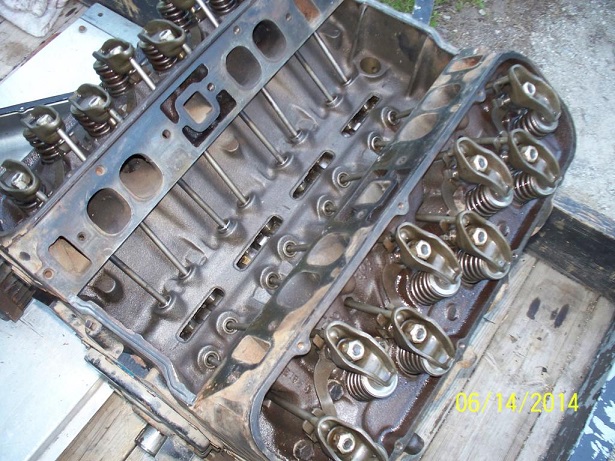
AS YOU MAY NOTICE DOING THIS ON A BIG BLOCKS A BIT EASIER
that stainless perforated steel should be fine, in fact nearly ideal as long as you fabricate a single plate shrapnel screen to lay over the lower lifter gallery floor area, making a single drop in shrapnel screen (usually with several magnets ) has the advantage of far more surface area and far easier cleaning than the typical epoxyed in individual screens and if you've never done that here's how you go about making the pattern easily.
first you place the block with a level on the block rails and move it around until the level indicates the block rails are level in all directions, next you place 3 full block length layers of tin foil in the lifter gallery floor over the oil drain areas and smooth them out, then you heat about 4 blocks of paraffin wax up, and pour it in to fill the lifter gallery floor up to the mid point on the lifter bores , on roller blocks the wax won,t cover the spider spring bosses
please pardon my rotten computer graphic skills
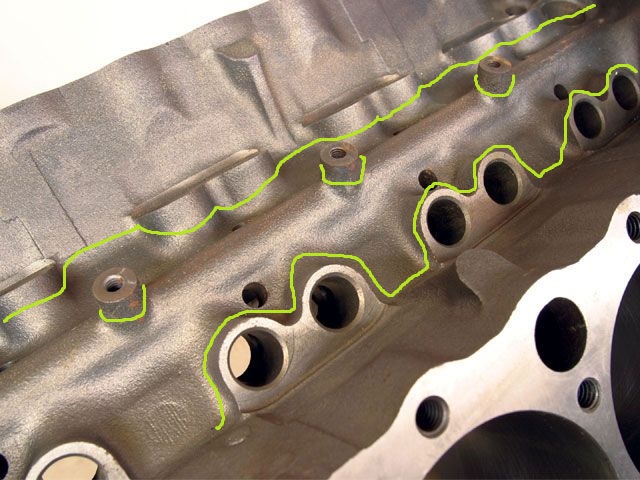
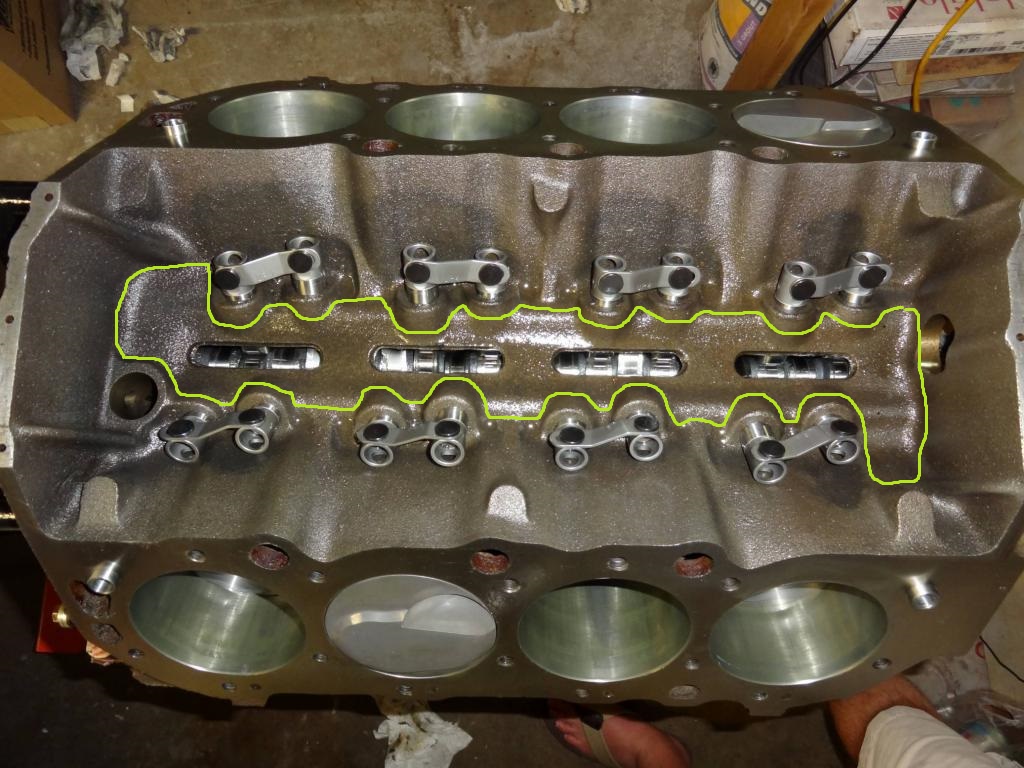
once the wax/paraffin hardens you lift it out , carefully flip it over on the perforated steel, remove the tin foil and spray the paraffin outer edge with black paint, allow it to dry then remove it, the result is a stenciled outline showing the shrapnel screen, pattern to cut out for a custom fit.
"Any source for the magnets Grumpy? "
http://www.kjmagnetics.com/proddetail.a ... SH&cat=167
Ive used these for years
http://www.magneticdrainplugs.com/
http://www.kjmagnetics.com/proddetail.asp?prod=D82SH
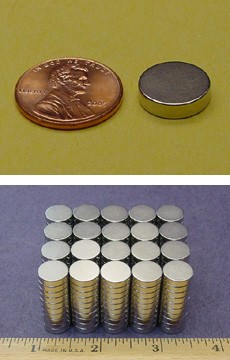
btw I generally bend my perforated steel or aluminum lifter gallery floor covering shrapnel screen in an arc to allow the center to be higher than the edges , and BTW aluminum and stainless won,t stick to magnets so use J&B WELD EPOXY
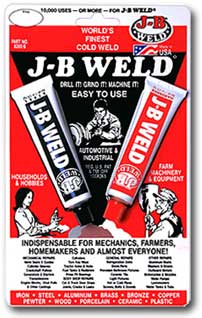