To install the Valve Body (VB), start with the check balls that go in the worm
casting of the case. Use lube to keep the balls from moving. From the factory
it has 7 balls, but I’m only going to put in the 5 balls according to CKP shift
kit instructions. Even the CKP book calls for 7 check balls, so I had to pay very
close attention to what I was doing and both pieces of documentation. The
book is maybe 6-8 years old now and Chris has made updates to his hard
components and processes.
Also goes in is the 3-4 accumulator piston and spring. The spring is a
CKP replacement.
4355
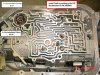
There are two gaskets and they are different, but you can tell which one
goes where by looking for the letters cut into the gasket. Letter “C” is for
the case and letters “VB” are for the VB side. It’s hard to see, but the “VB”
is pointed out in the photo below.
Put the case gasket on, then the separator plate and then the VB gasket.
Use 4 VB bolts to keep everything aligned while you are installing the
pieces to the 1-2 accumulator.
4363
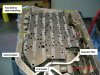
Next goes the accumulator plate and gasket, 1-2 spring (from CKP) and 1-2
housing with piston installed. Torque the 5 bolts to 18 ft/lbs.
4367
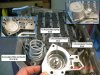
Next is the VB assembly, but first you need to install the check balls in the
locations shown in the photo below. Again you need to use Vaseline or a
transmission lube. If you are working in summer temps of 80° F and above,
I would recommend the GREEN lube. It’s stable up to 130° F, where Vaseline
is getting pretty thin.
4370
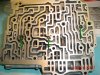
You will have to remove the 4 bolts from above first, then put the VB on and
add the other pieces that have to be bolted in place with the VB bolts ….
TV linkage, shifter detent and signal oil pipe.
I haven’t torqued my VB bolts since I still have to figure out my wiring for
the TC lockup system. It's also held in place with the VB bolts.
4376
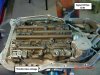
All the check balls installed are made from a Viton material according to the
parts counter person at OTS. I think they were about $1.25 each.
4361
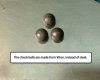
Last edited: