probably 90% of the timing sets being installed are installed with the crank gear flush with the shoulder on the crank snout and with never a single thought being given to proper alignment being an issue, and with thousands of those engines making well over 100K miles before the timing chains replaced, that doesn,t mean they are correctly aligned it just indicates that the basic design is rather forgiving as to the conditions it will continue to function in without causing major problems AND THAT in most cases the manufacturing tolerances are close enough to correct to have few issues with wear. but Id also point out that most engines are not running at near their full power potential and most engines have basic flaws costing them both some horse-power and durability problems
Chevy for years used NYLON gear teeth on aluminum gears, its not like they were concerned with getting the alignment correct to the last possible 2-5 thousands of an inch, they designed the timing sets to be easy to install and reasonably durable and run QUIETLY , and yes they eventually realized that was a HUGE mistake! but in this thread we are dealing with building an engine correctly, to gain all potential hp, and enhance durability here, not in merely allowing it to run once assembled
RELATED INFO
viewtopic.php?f=52&t=1793&p=4553#p4553
TRUE DOUBLE ROLLER TIMING CHAIN SETS FROM QUALITY MANUFACTURERS TEND TO BE MORE DURABLE
notice the more aggressive cam lobe acceleration rate on the roller cam lobes
notice the stepped cam nose to fit retainer plate
they usually use TORX SCREWS LIKE THIS on retainer plates
BTW IF your reading these threads READ THRU THESE RELATED LINKs
viewtopic.php?f=50&t=223&p=8024&hilit=damper+tool#p8024
viewtopic.php?f=52&t=966
viewtopic.php?f=52&t=90
viewtopic.php?f=52&t=196
viewtopic.php?f=52&t=399
Chevy for years used NYLON gear teeth on aluminum gears, its not like they were concerned with getting the alignment correct to the last possible 2-5 thousands of an inch, they designed the timing sets to be easy to install and reasonably durable and run QUIETLY , and yes they eventually realized that was a HUGE mistake! but in this thread we are dealing with building an engine correctly, to gain all potential hp, and enhance durability here, not in merely allowing it to run once assembled
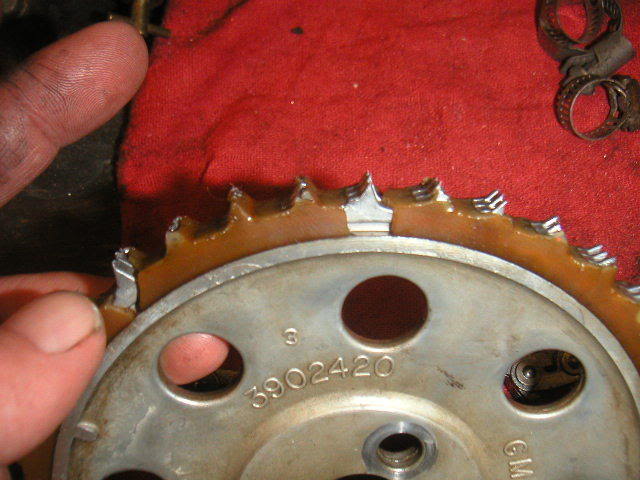
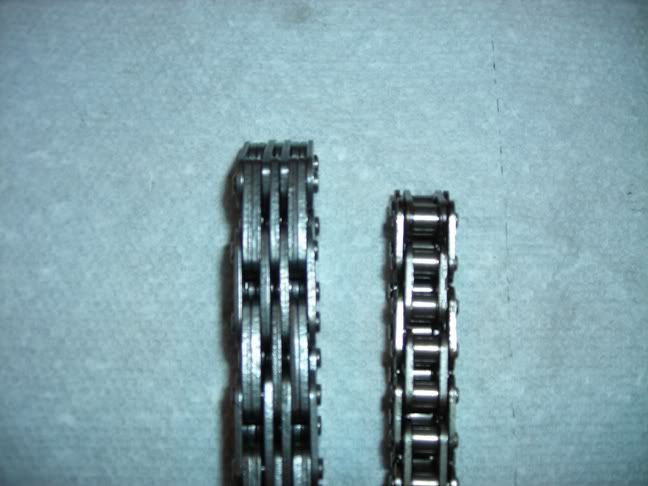
RELATED INFO
viewtopic.php?f=52&t=1793&p=4553#p4553
TRUE DOUBLE ROLLER TIMING CHAIN SETS FROM QUALITY MANUFACTURERS TEND TO BE MORE DURABLE
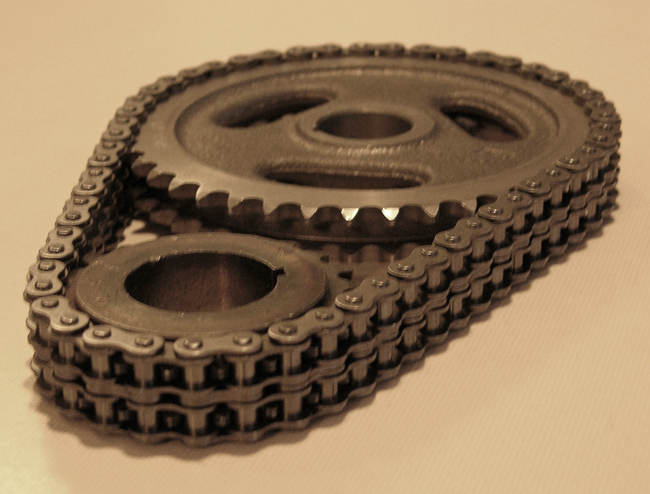

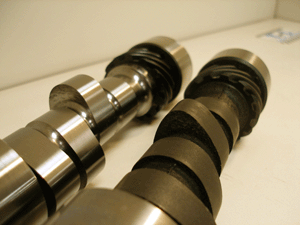
notice the more aggressive cam lobe acceleration rate on the roller cam lobes
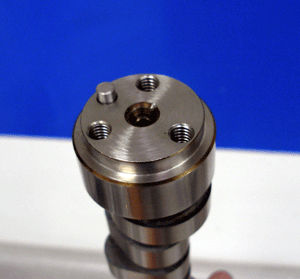
notice the stepped cam nose to fit retainer plate
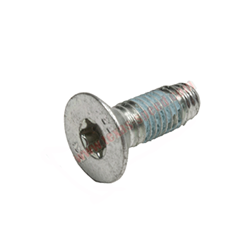
they usually use TORX SCREWS LIKE THIS on retainer plates
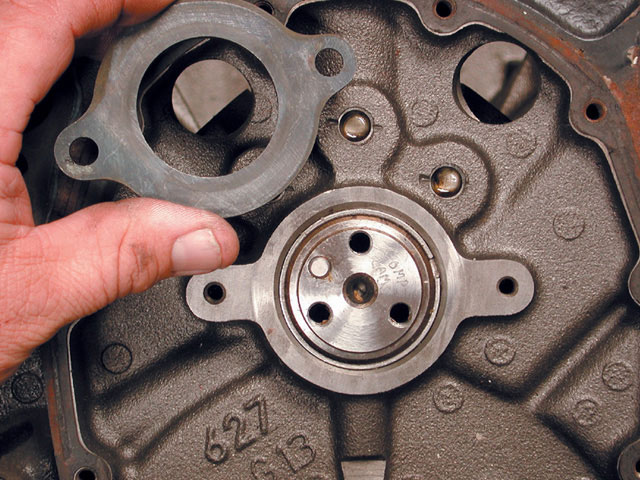
BTW IF your reading these threads READ THRU THESE RELATED LINKs
viewtopic.php?f=50&t=223&p=8024&hilit=damper+tool#p8024
viewtopic.php?f=52&t=966
viewtopic.php?f=52&t=90
viewtopic.php?f=52&t=196
viewtopic.php?f=52&t=399