I went back to check the Piston-To-Valve clearance again using the clay method. This time with the dial indicator on the spring retainer so I could see if the valve moved, I adjusted the poly lock until the lifter stopped compressing and the valve retainer started to move. Then I backed up until the indicator read zero again. With this method I got roughly .530" lift out of the theoretical of .562/.567". I then turned the engine over 10 revolutions.
As you can see from the picture the valve is hardly even making an impression in the clay.
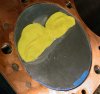
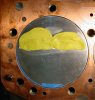
I also wanted to see how this compared to the other method that I tried earlier (Posted: Mon Dec 12, 2011 11:14 am). The clay method show that I have considerably more clearance than the other method. Since the valves and pistons don't move parallel to each other, the the actual clearance will be something greater than the measured value.
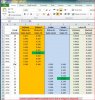
All checks were performed with the adjustable pushrod set to 7.45".
Last edited: