mathd said:Nice, did you check the header to spark plug wire for clearance? i know you will anyway, just asking because they look very well routed right now![]()
Thanks!
There shouldn't be any problem, every exhaust header comes straight out for 12".
You can also see how close the firewall is and my reason for wanting more bolted support for the plug wires.
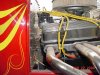
Last edited: