Pump (Almost) Final Install .......
Before moving into the pump installation, the pump halves need to be aligned.
You can use a large specialty clamp or band - I elected to use another acceptable method, which is to use the case itself for alignmnent.
I had left myself a note back when I had cleaned up the pump.
The pump is placed upside down into the case, without gasket or o-ring. Pump body bolts are barely finger tight to allow movement.
Here you can see the pump in the case with a number of bolts and dowels aligning the pump halves.
Then the bolts are torqued to 18 ft/lbs in a cross pattern.
Next important step was to figure out the input shaft endplay. I had already done the same for the output shaft.
There were three plastic selective pump thrust washers in the rebuild kit, but I had also bought a complete set.
Selectives come in either number or letter series, and their thicknesses can vary a bit, so each number/letter is given a range.
The three selectives shown were letters A (.072), C (.094), and E (.117). The selectives in the bag covered letters A to E.
The pump gasket is about .0015 uncompressed, and about .0012 when compressed.
That number can be added to the selective washer thickness if you choose to install the pump without gasket/oring. It's a bit easier that way, but your final measurement should be verified after final pump installation.
Here's a black plastic selective in place along with new teflon scarf-cut pump stator seals.
I had left out the seals and pump o-ring while I was trying different selectives getting to the right endplay measurement.
Note - the scarf cuts are 90 degrees away from that fluid feed hole, one to the right, one to the left, so that the cuts are 180 degrees away from each other.
Spec endplay is .007 to .024, generally a tighter measurement is preferred to allow for break-in and future wear.
The original input shaft endplay was .029, very loose. The original plastic selective bushing was .093 thickness.
This is the general measurement setup - the vice-grips help to grip the input shaft when pulling up.
Assuming that the endplay would be tightened up with all the new parts and bushings, I tried a "C" selective (.094).
Measurement was taken with pump installed on gasket, bolts tightened - came out to .010, which is ideal. I think that the gasket will compress a bit further and that after break-in there will be a bit more clearance added. I'm happy with this setting.
Pump o-ring was installed, and pump set into place but not as final installation......
The reason that I can't call this final is due to 6 little washers .....
In this unit, this pump takes 6 bolts with sealing washers. Some pump bolts take an o-ring, but these are rubber coated sealing washers.
I can't re-use them and I want to use the right parts, so I ordered a new set. You can see the old ones were in crummy condition.
All in all, that's minor, when I get the new washers, I'll just loosen the bolts, install the washers, and re-torque (18 ft/lbs).
Glad to have the geartrain in place and measured out - now ready to move on to the valve body and peripherals.
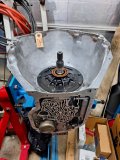